Valve Seats OEM & ODM Supplier - BLUE
BLUE offers a wide range of standard valve seats without mold fees, excellent wear resistance, low friction, and heat resistance. We various valve seats, applied in multiple gasoline and diesel engines Cummins, Weichai, Ford, Toyota, Honda, etc.
Why Choose BLUE?
BLUE offers top-quality valve seats with tight tolerances, excellent wear resistance, and heat resistance – your trusted OEM and ODM supplier
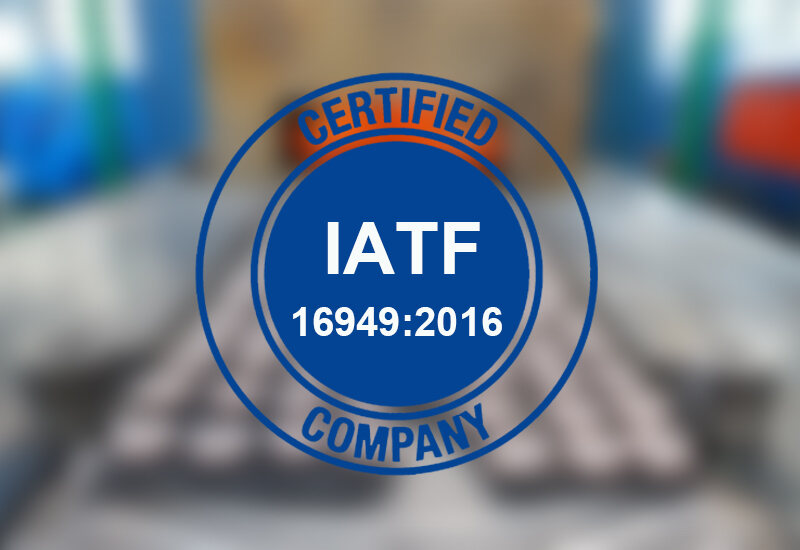
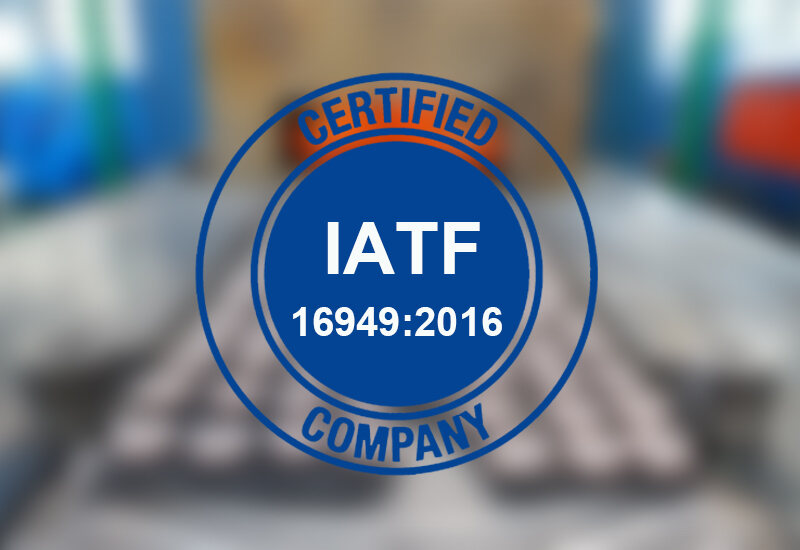
BLUE High Quality Standards
BLUE assure the quality of your valve seats with an IATF 16949: 2016 certified quality management system. Free samples are available for testing.
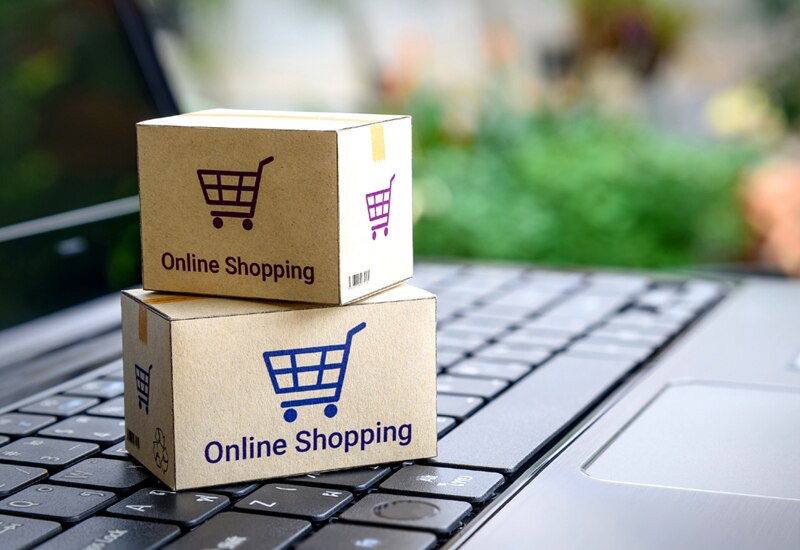
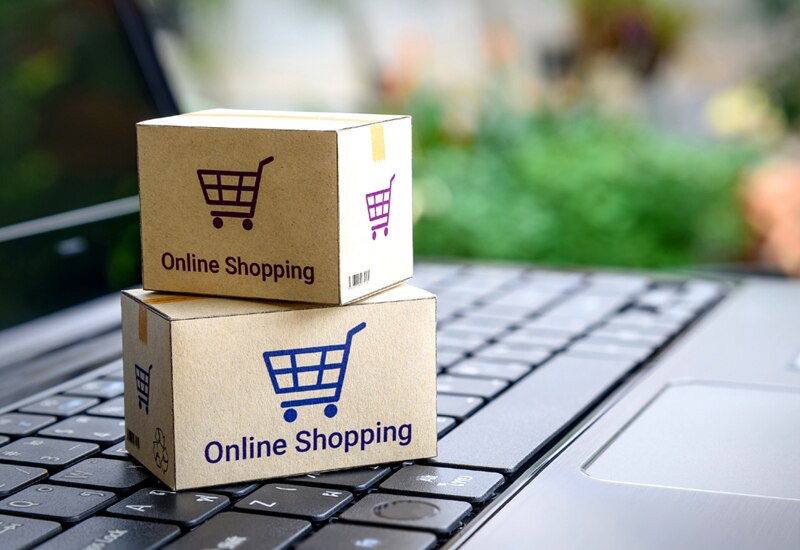
Standard PM Parts Shop
BLUE has a full range of standard sintered parts in stock for fast delivery. Visit our standard parts shop to find the exact match for your applications.
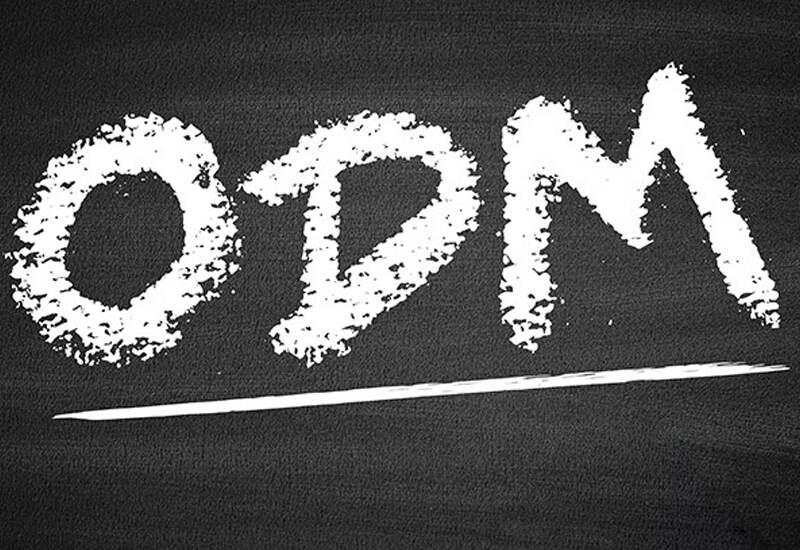
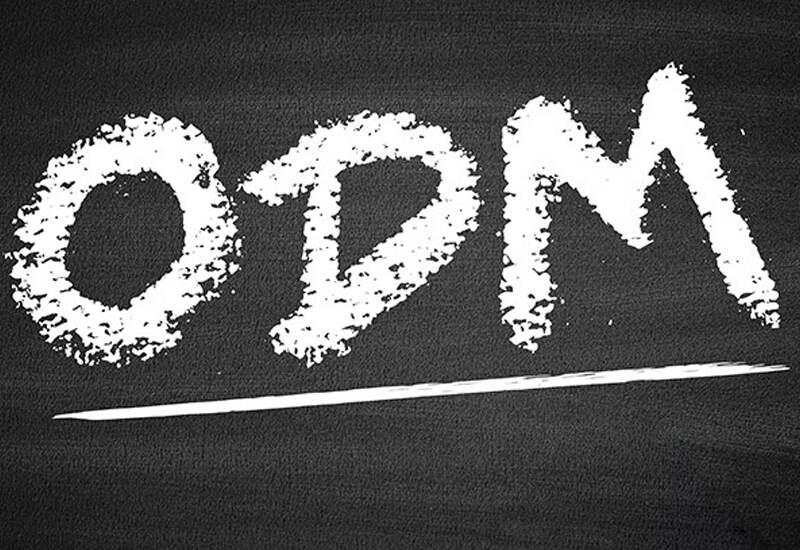
OEM & ODM Services
With over 20 years of expertise in designing and manufacturing powder metallurgy parts, BLUE provides OEM and ODM services for you.
BLUE Valve Seats in China
BLUE offers a wide range of valve seats for petrol and diesel engines, featuring low friction and resistance to high impact loads.
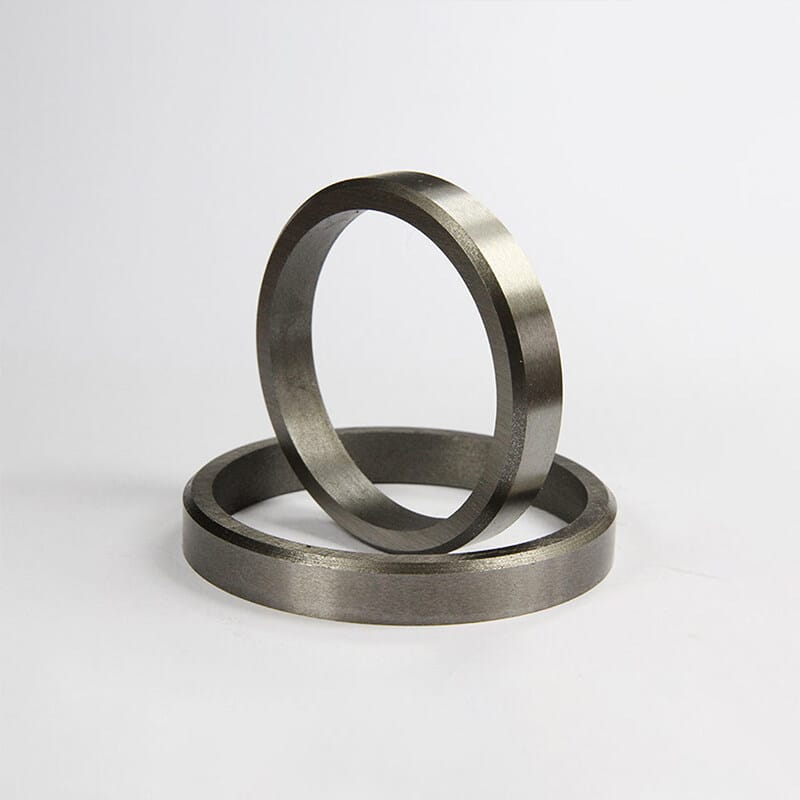
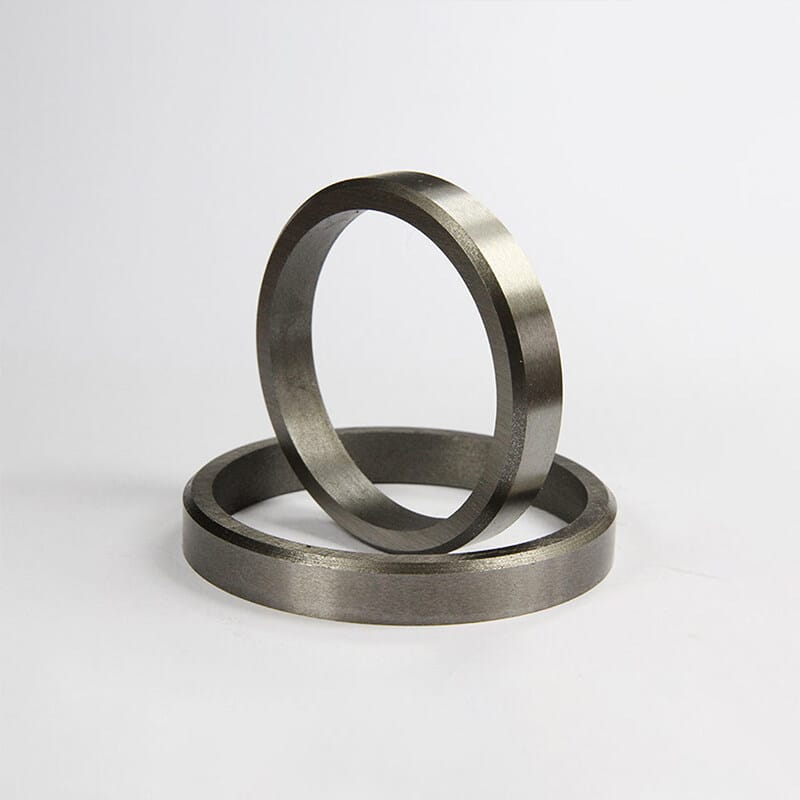
Engine Valve Seat
Engine valve seat works with the valve to open and seal the combustion chamber of an internal combustion engine
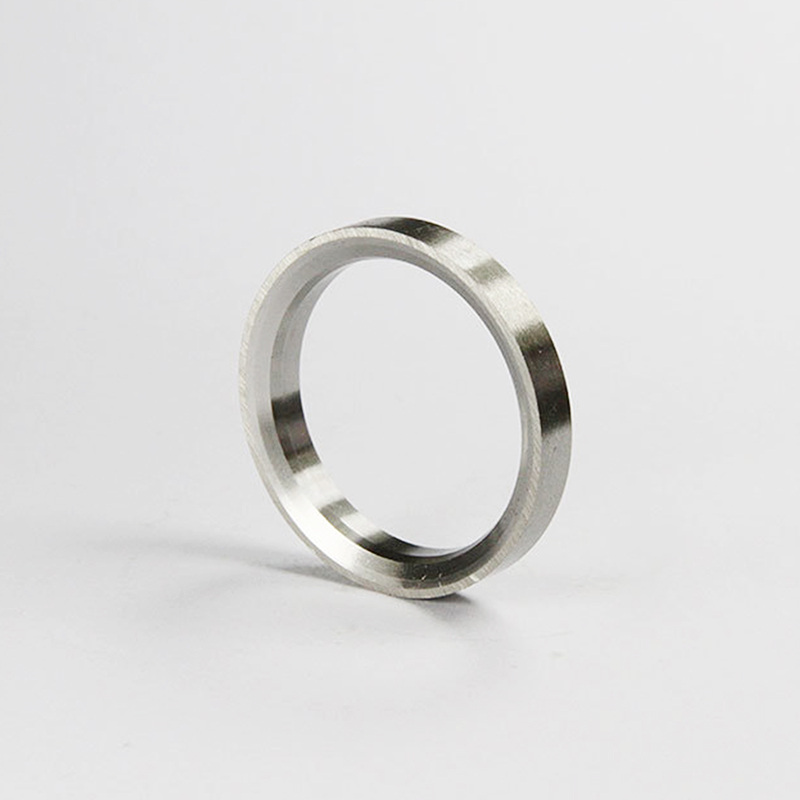
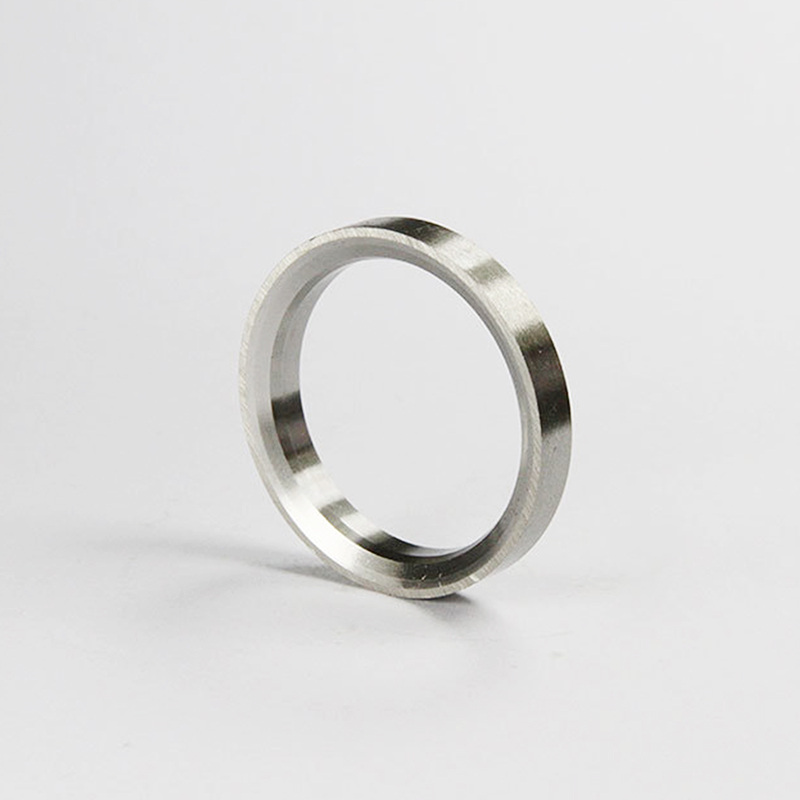
Intake Valve Seat
BLUE intake valve seat has advantages of good lubricity, mechanical strength and corrosion resistance.
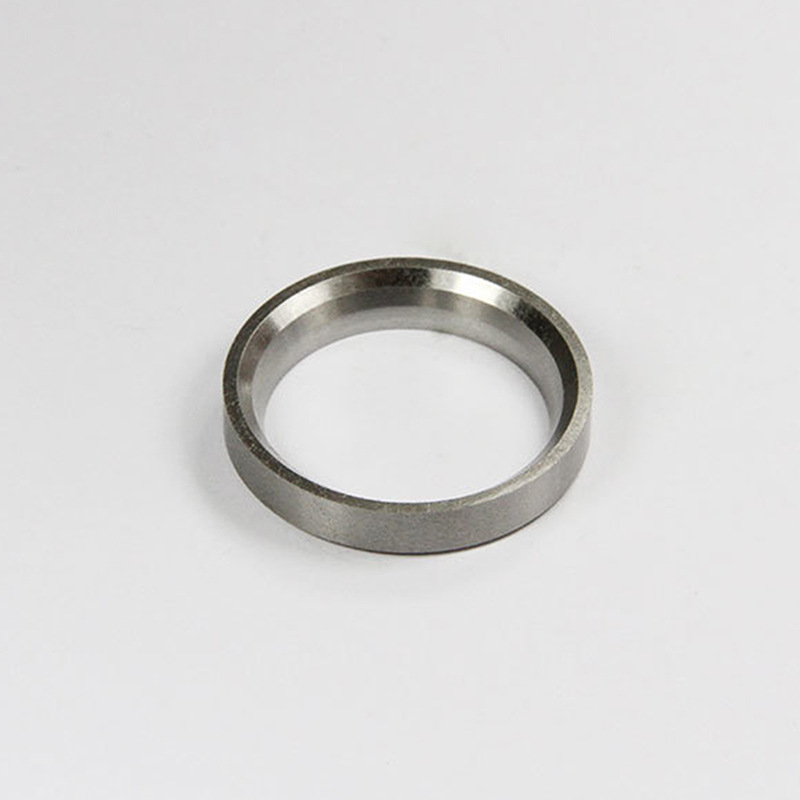
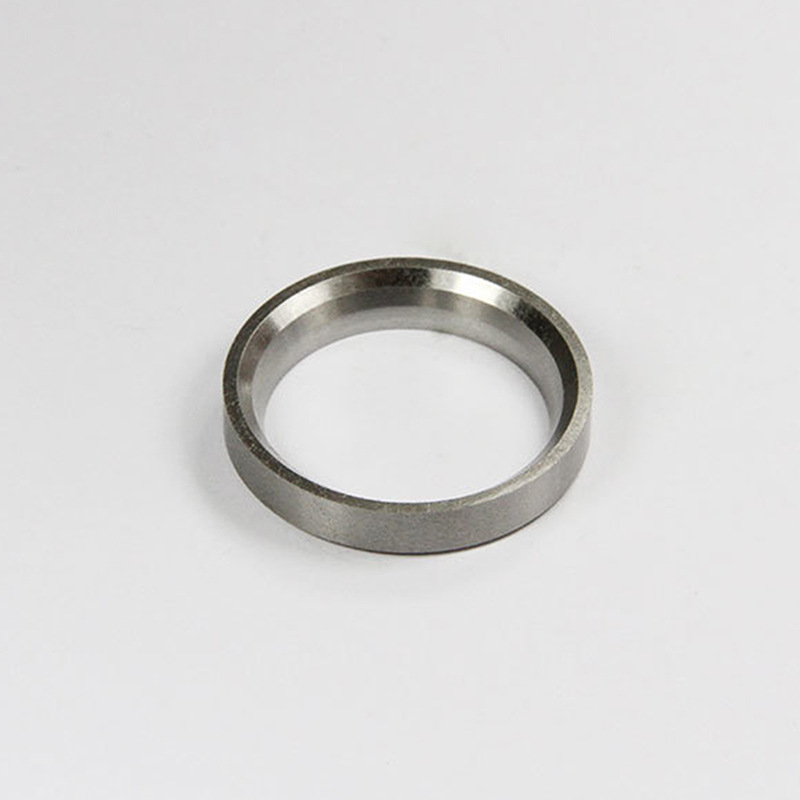
Exhaust Valve Seat
BLUE exhaust valve seat has high load impact resistance, high temperature resistance and good thermal conductivity.
BLUE Valve Seat Advantages
BLUE’s valve seat are manufactured under the supervision of IATF 16949:2016, assuring high quality.
Our sintered valve seats can add anti-friction materials to achieve good self-lubrication and anti-friction effects.
BLUE’s valves are not only applied in ordinary engines, but also in heavy-duty diesel engines and engines running on compressed natural gas, alcohol fuel and liquefied petroleum gas.
The hardness of the BLUE valve seat after heat treatment exceeds 40HRC.
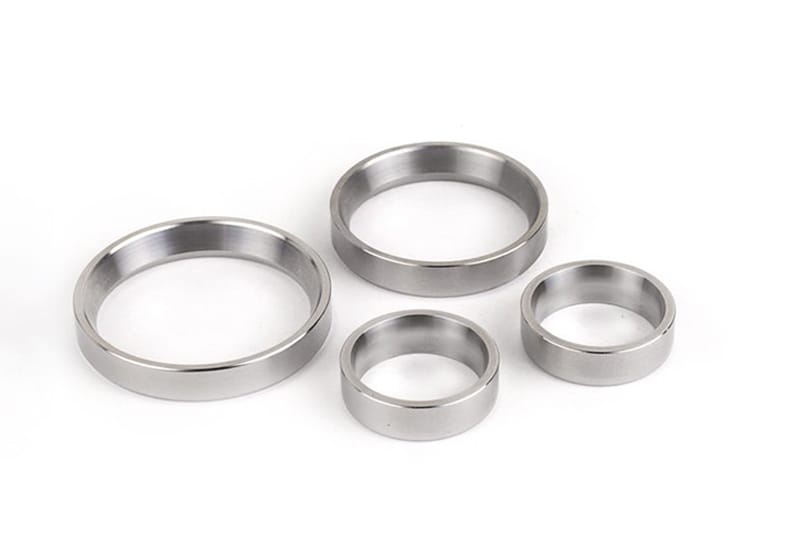
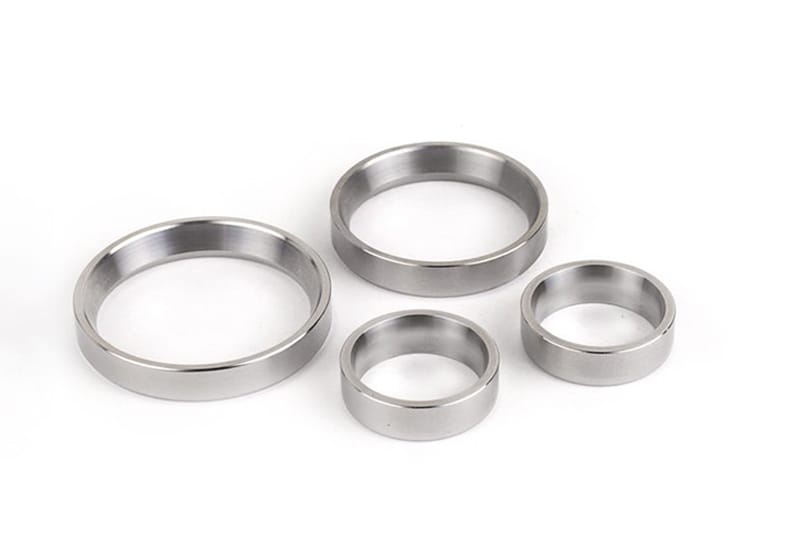
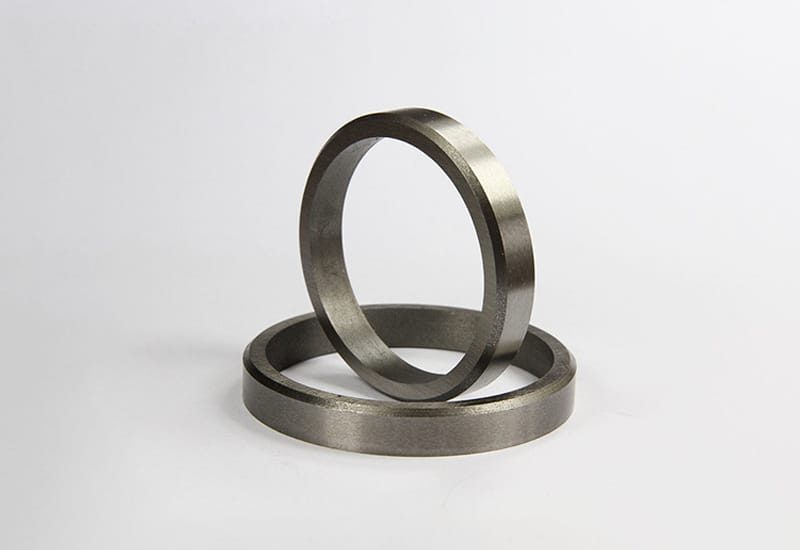
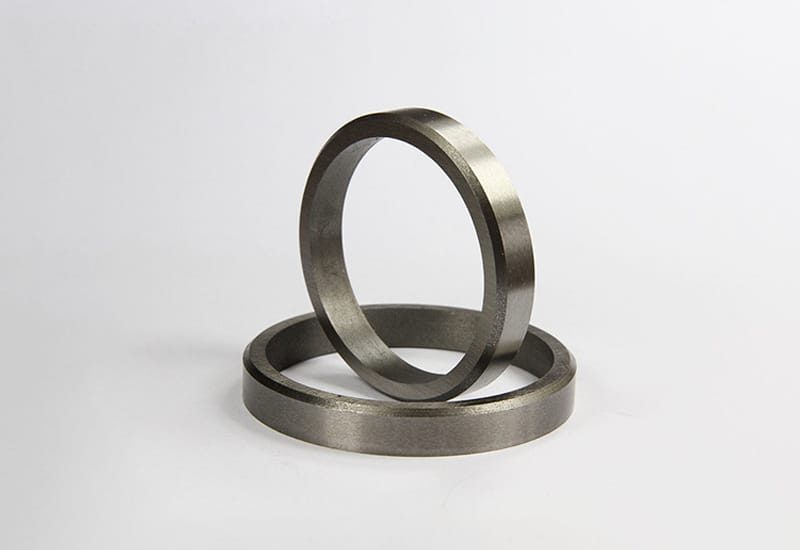
Enhanced Mechanical Properties
BLUE has a professional team of engineers and advanced production equipment with full powder metallurgy process manufacturing capabilities.
We provide copper infiltration, heat treatment, and steam treatment to enhance the mechanical properties of your PM parts.
BLUE’s copper-infiltrated valve seats feature a density of 7.5 g/cm³, a hardness of 50 HRC, and a compression strength of 699 MPa.
Valve seats subjected to heat treatment effectively improve wear resistance, density, yield strength, etc.
Advantages of Sintered Valve Seat
Precision and Consistent Quality
Sintered valve seats have tight tolerances and uniform material properties, delivering consistent quality.
Cost-Effectiveness
Powder metallurgy minimizes material waste, enabling efficient, high-volume production.
Optimized Material Properties
The PM process allows for the addition of alloying elements, enhancing the strength, wear resistance, and other key properties of the valve seats.
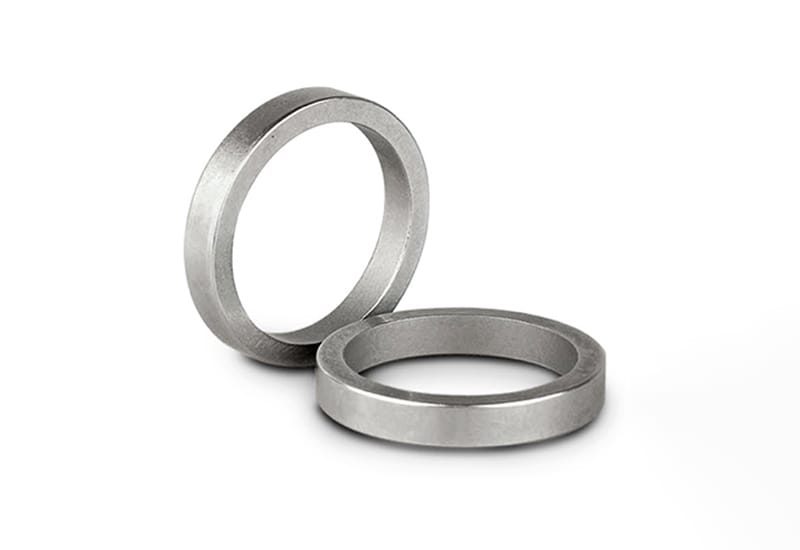
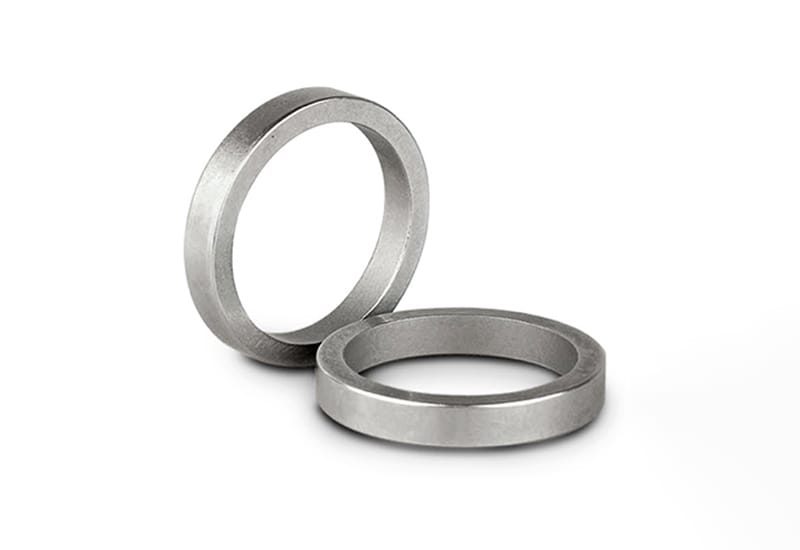
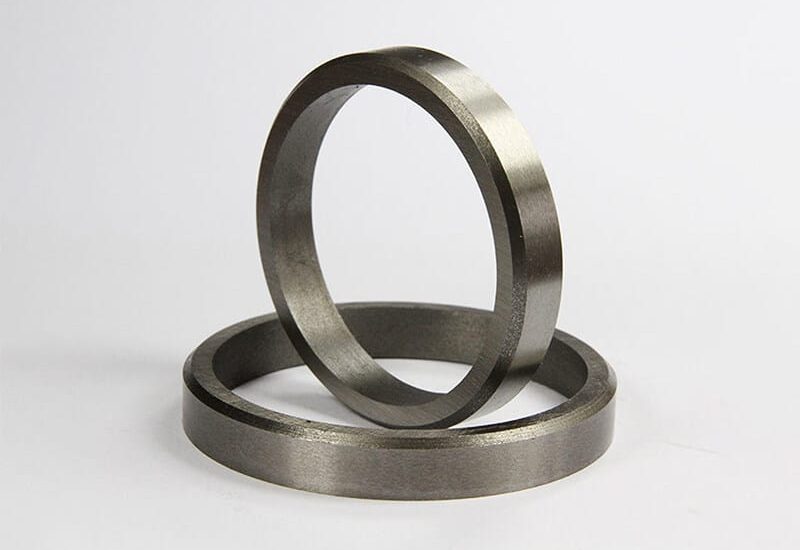
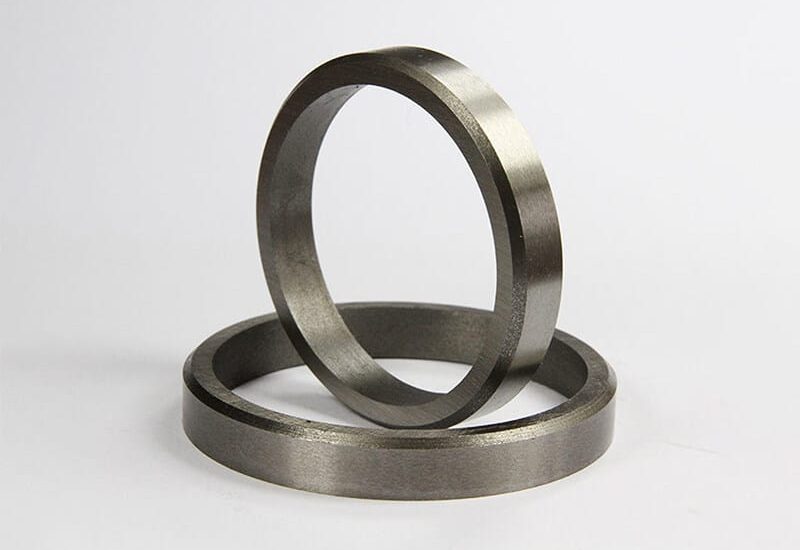
What is a Valve Seat?
The valve seat is a key component of an internal combustion engine’s combustion chamber.
It absorbs the high-speed impact of the valve while providing a durable, heat-resistant surface that ensures proper sealing for valves.
Working in conjunction with the engine valve, the valve seat enables the combustion chamber to open and seal correctly, controlling the intake of air-fuel mixture (intake valve seat) and the expulsion of exhaust gases (exhaust valve seat).
Custom Valve Seat Specifications
The table shows our manufacturing capabilities for customized valve seats, including material, density, hardness, tolerance, and surface treatment.
Attribute | Value |
---|---|
Material | Sintered Iron Alloy |
Sintered Density | 6.6-7.0g/cm3 |
Sintered Hardness | 65-90 HRB |
Hardened Hardness | 40 HRC Min. |
Tolerance | ±0.01 mm |
Diameter | 20-60mm |
Length | 6-20mm |
Powder Metal Valve Seat Manufacturing Process
Powder metallurgy is a precision manufacturing process with a continuing and stable accuracy of up to 0.01mm, which requires strict control at each stage to ensure the quality of the final part. Any deviation or error during the process may result in the rejection of the entire batch.
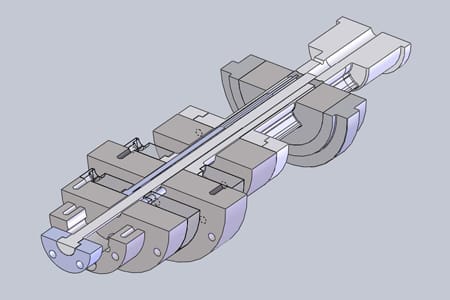
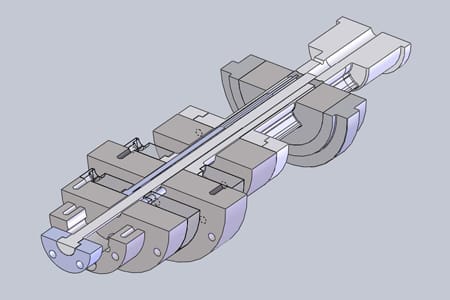
Designing
Mold design is a critical process that must consider the desired part geometry, material properties, production volume, and cost-effectiveness.
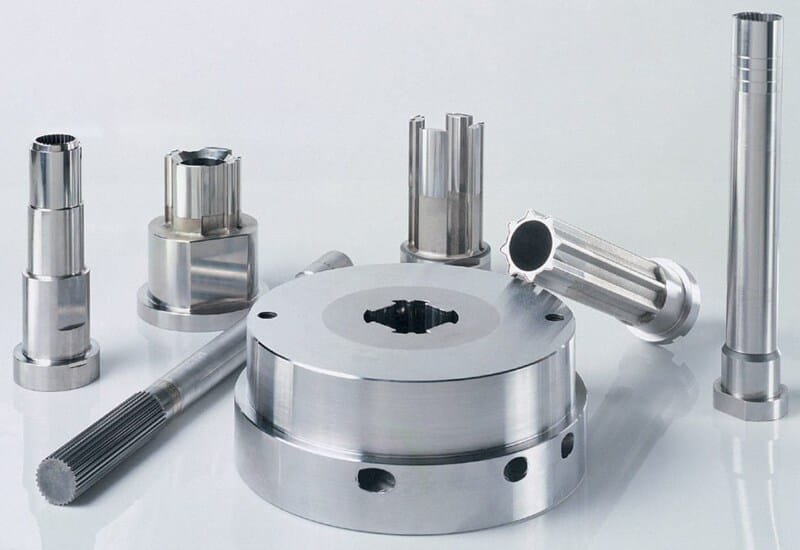
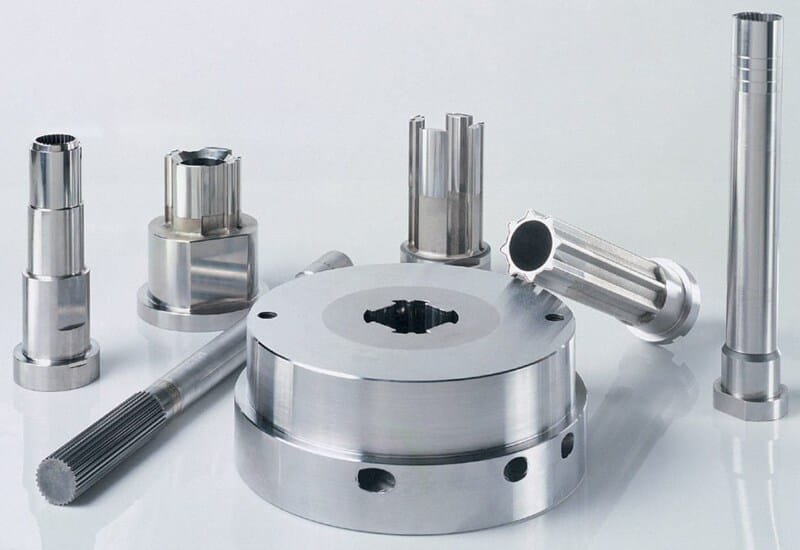
Tooling
Powder metallurgy tooling includes upper and lower punches, die, and core rod. The mold needs to have excellent strength, hardness and wear resistance.
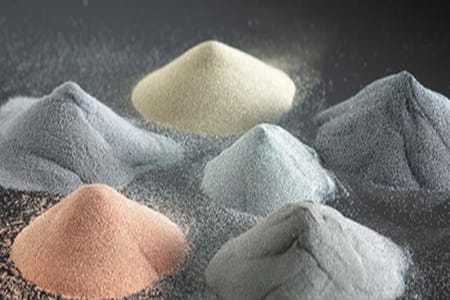
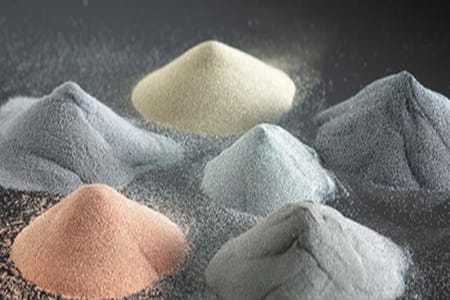
Mixing
Mixing is the process of blending metal powder with binders to improve its uniformity and fluidity, promoting better material consistency.
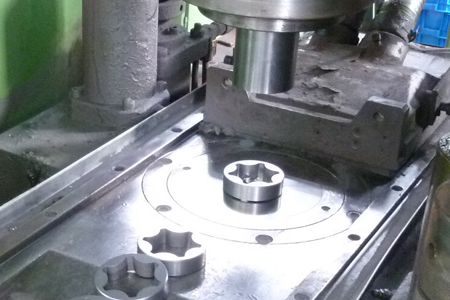
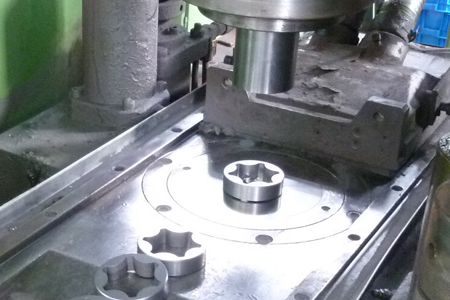
Compacting
Conpacting is a process that presses metal powder into mold cavity through powder compaction machine to get a green compact part.
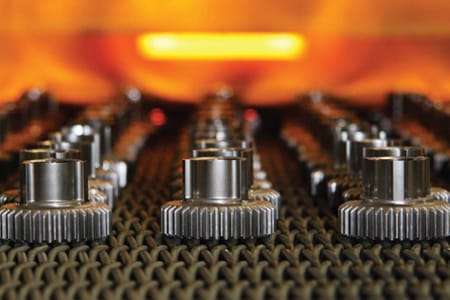
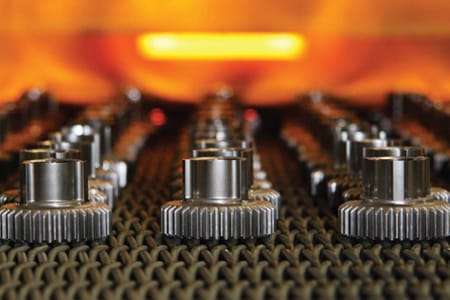
Sintering
Sintering heats the green compact to a temperature below its melting point in a controlled atmosphere to obtain the desired mechanical properties.


Sizing
Sizing corrects dimensional deviations after sintering and enhances product accuracy. It requires an additional, simpler set of molds compared to the forming mold.
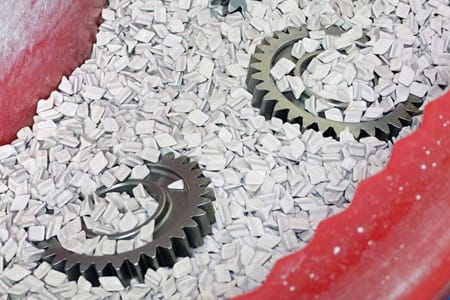
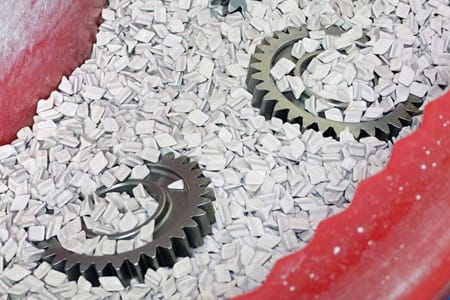
Tumbling
Tumbling removes burrs and flash from a part's surface by vibrating it with abrasive media, such as stone or ceramic, resulting in a smoother finish.
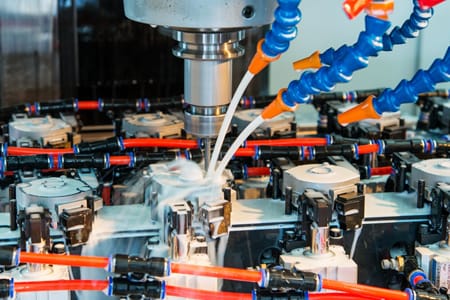
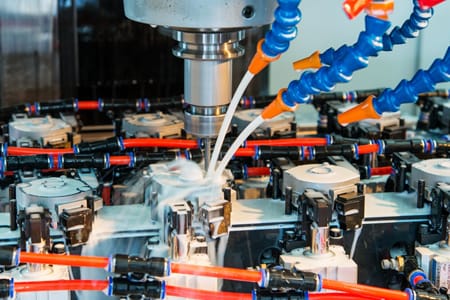
Machining
Machining can achieve complex shapes that cannot be pressed by powder metallurgy, such as transverse holes and screw threads.
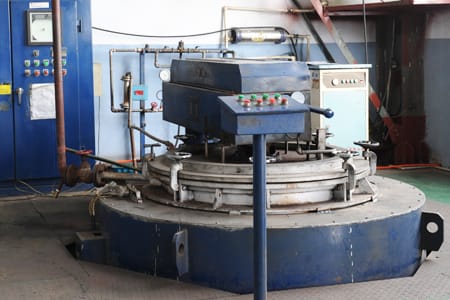
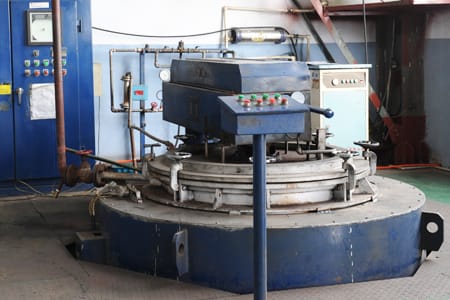
Blackening
Blackening process, or steam treatment, forms an oxide layer to prevent rust and increase hardness, offering a cost-effective solution.
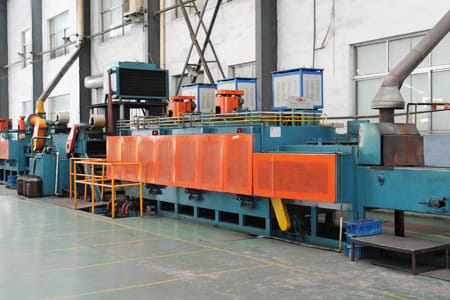
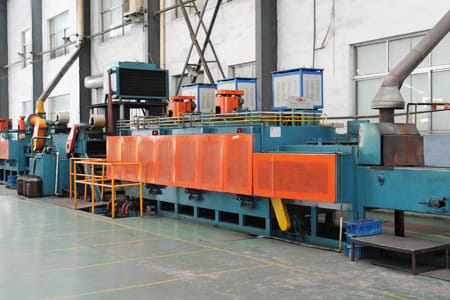
Hardening
Hardening enhances the material's strength and hardness through carburizing or nitriding, resulting in improved wear resistance and fatigue life.
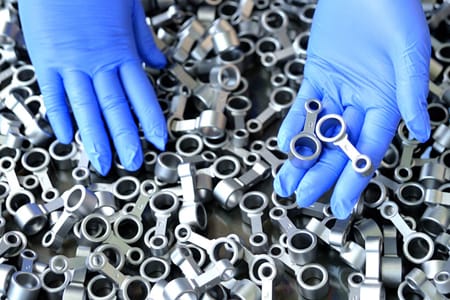
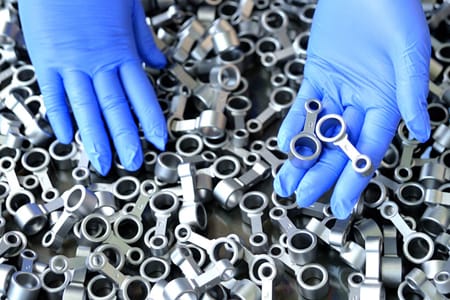
Inspecting
The inspecting process is always a critical step that ensures quality and performance through BLUE inspection standards before shipping.
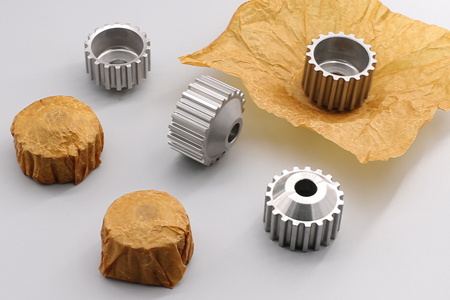
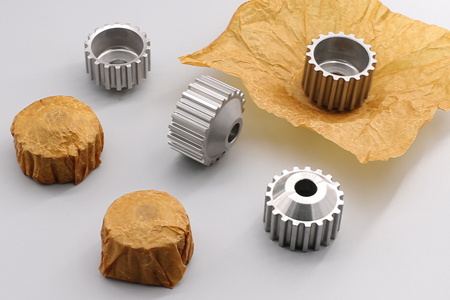
Packaging
BLUE's packaging process uses anti-rust paper, vacuum, blister and other methods to ensure that the product is intact during transportation.
BLUE's Powder Metallurgy Manufacturing Equipment
BLUE has a complete range of advanced powder metallurgy production equipment, including 25T to 1000T compaction press, conveyor belt sintering furnace, vacuum sintering furnace, sizing press, CNC machining equipment, hardening furnace, etc.
Related Sintered Auto Parts
As a leading powder metallurgy company in China, BLUE offers a variety of standard PM parts, including valve guides, water pump pulleys, timing chain sprockets, and oil pump rotors—all with no tooling fees.
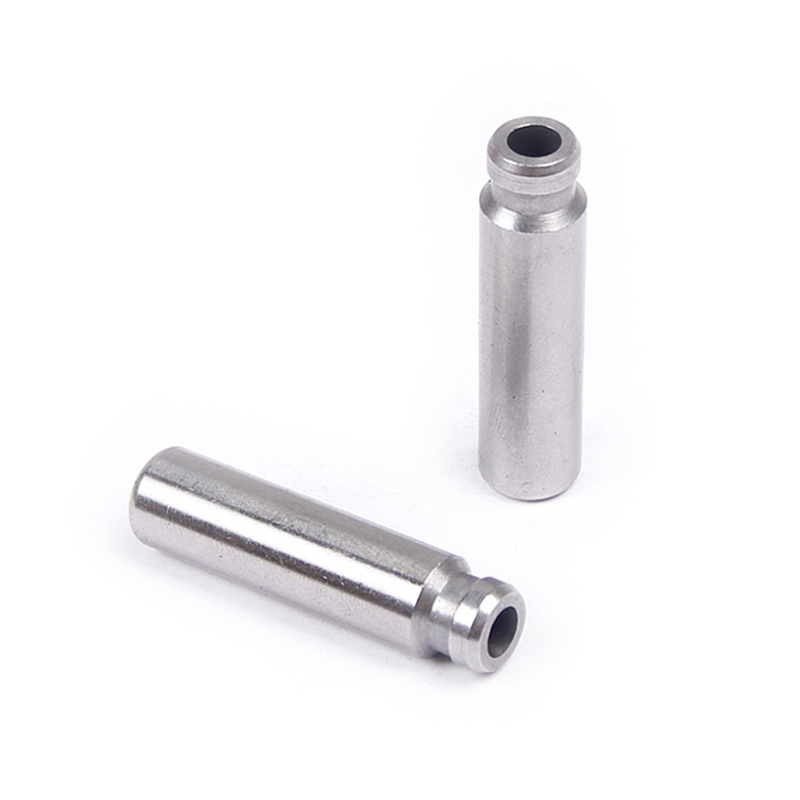
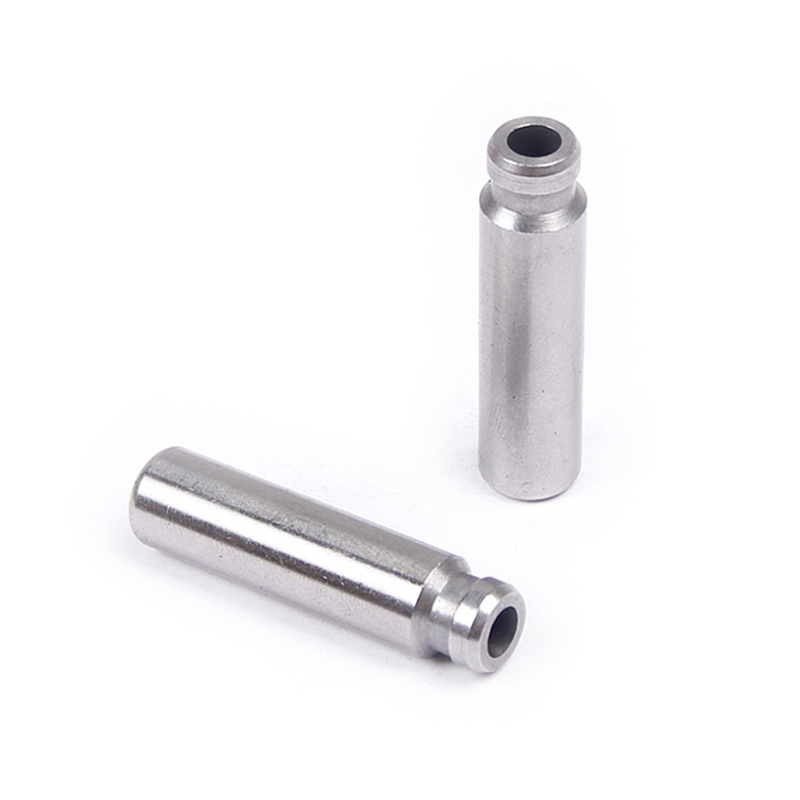
Valve Guide
Vlve guide directs the valve's movement while transferring heat from the valve stem to the cylinder head, aiding in heat dissipation.
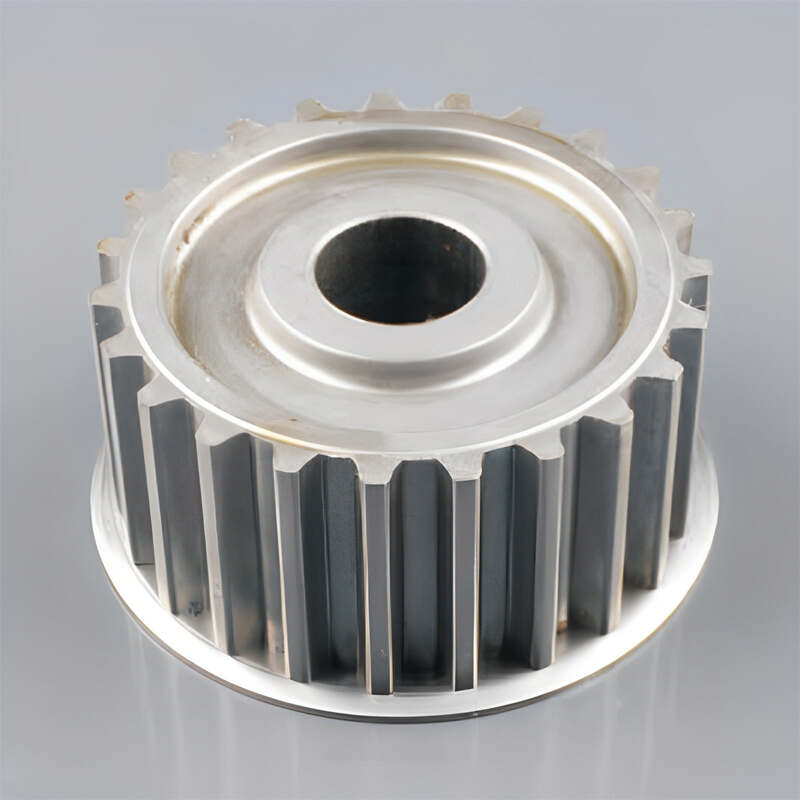
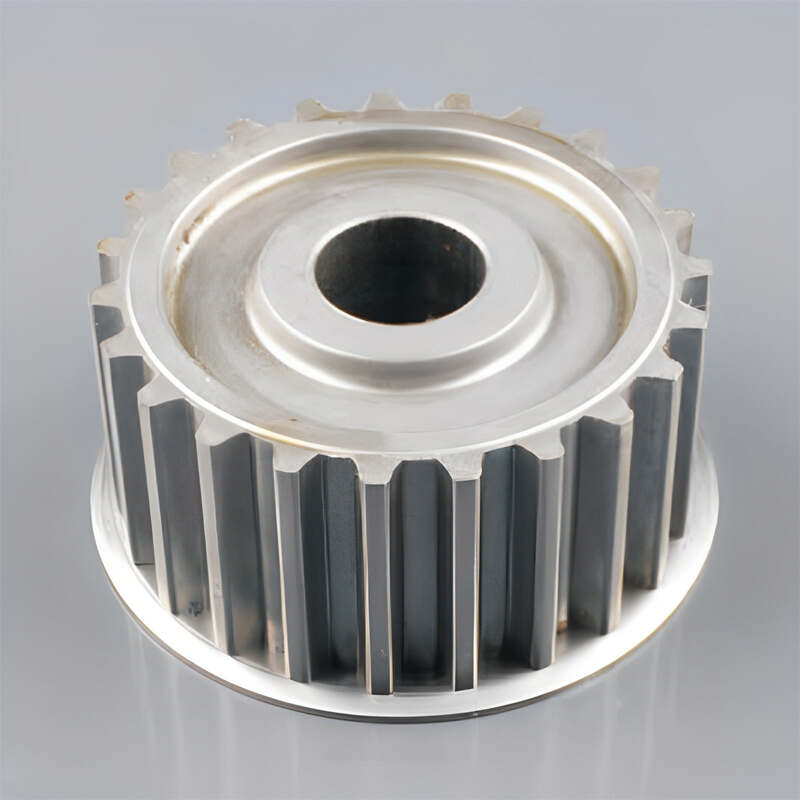
Water Pump Pulley
Our water pump pulleys feature tight tolerances, high apparent density, and superior mechanical strength.
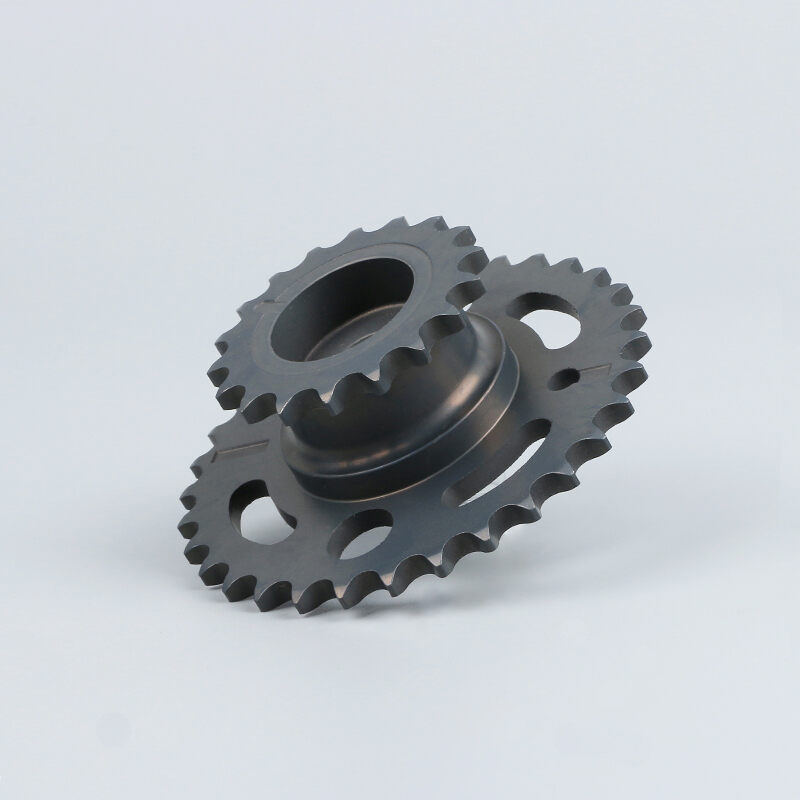
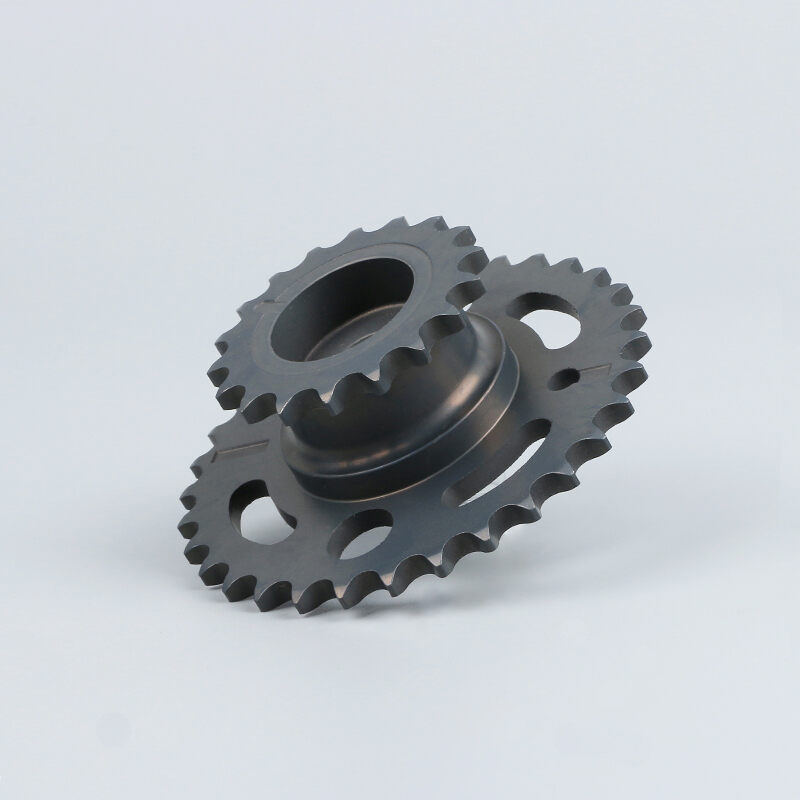
Timing Chain Sprocket
BLUE timing chain sprockets with precision teeth profile and holes, which fit perfectly with your chain and timing sprocket.
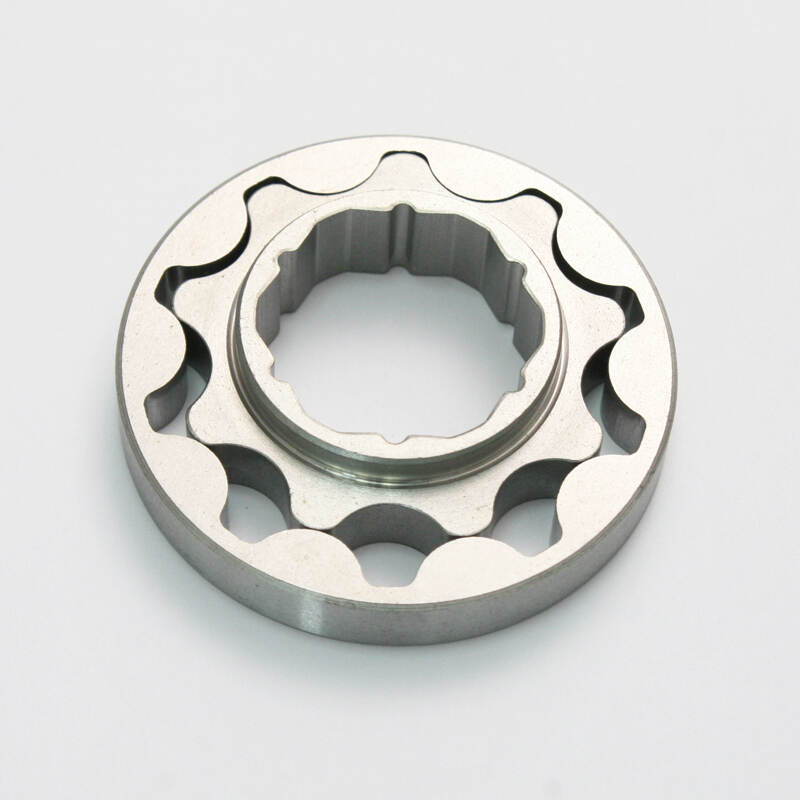
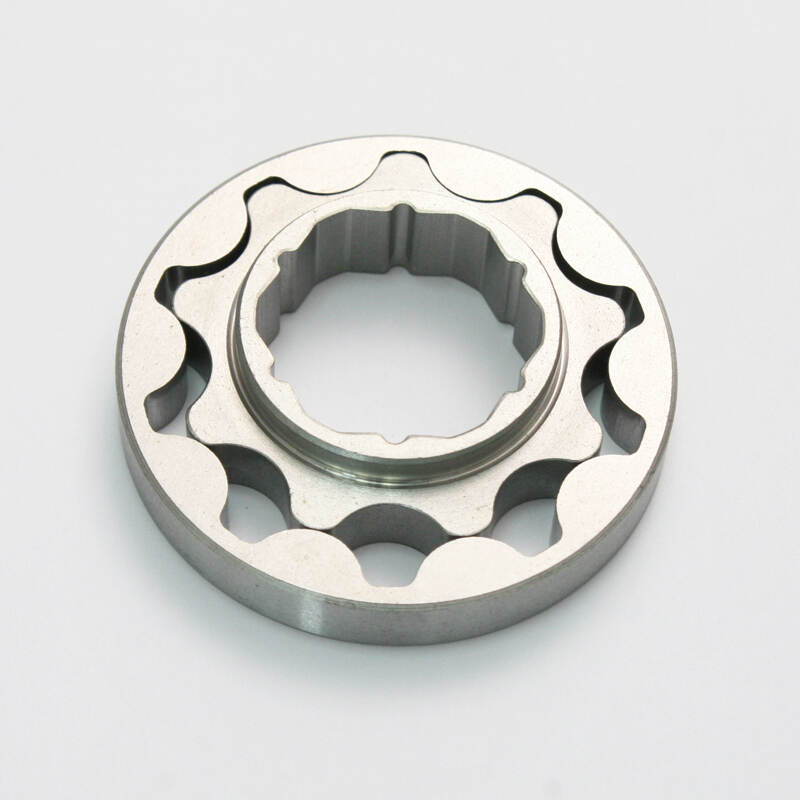
Oil Pump Rotor
Our oil pump rotors have good surface finish, tight dimensional accuracy and excellent position tolerances to deliver optimal engine performance.
FAQ's
Here are some of the questions we get asked often. If yours isn’t answered, don’t hesitate to contact us, we’re happy to help!
Here are some of the main causes of valve seat failure:
- The high-temperature environment of the valve seat during operation can reduce its hardness and cause thermal stress fatigue, leading to deformation.
- It endures the impact load from the valve, which causes wear.
- Additionally, the valve seat may fail due to exposure to corrosive gases discharged by the engine.