Custom Powder Metallurgy Part in China
BLUE are ISO 9001:2015 certified, providing free mold design services, free samples, and advanced production equipment to meet your customized requirements. Easy to custom powder metallurgy parts with BLUE—simply contact with our team to get started!
Why Choose BLUE?
BLUE offers a high-level quality control system, advanced PM machines, and free mold design, delivering top-quality, custom solutions across the entire range of powder metallurgy parts.
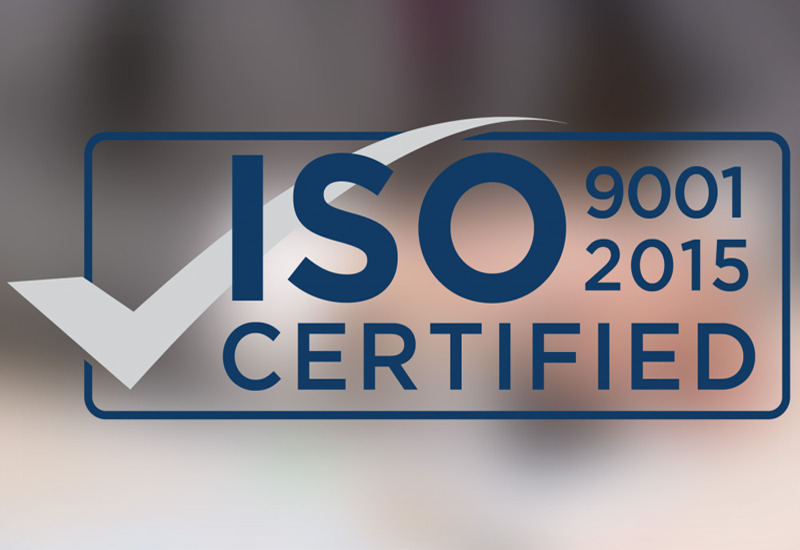
BLUE Quality Standards
BLUE assures your product quality with ISO 9001:2015 certified quality management system. We provide a one-year warranty on your products.
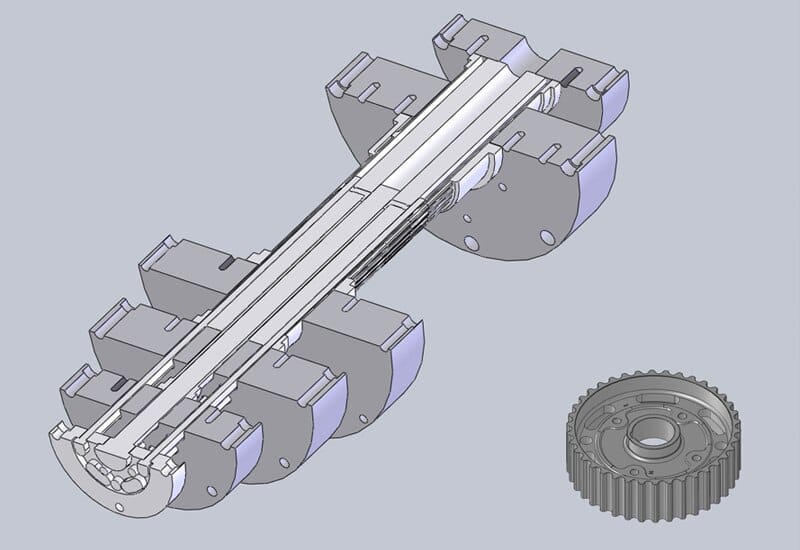
Free PM Mold Design
With over 20 years of expertise in mold design, BLUE offers free, high-precision mold design services to meet your customized needs. Let our experience work for you!
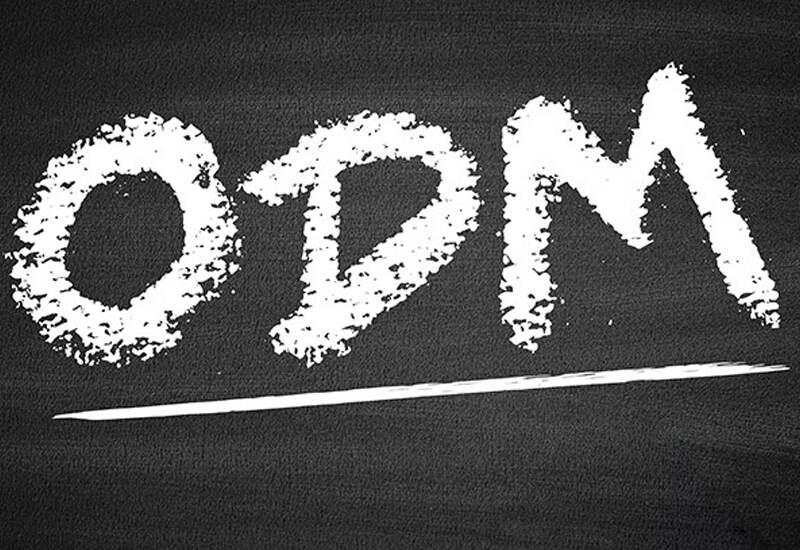
OEM/ODM Services
Using advanced equipment, we provides free mold design based on your drawing and offers assistance with your cotomized product processing.
Custom Powder Metallurgy Parts Capabilities
BLUE covers the full range of powder metallurgy processes, providing one-stop customization for powder metallurgy parts, MIM parts, sintered filters, and sintered ceramic components with strict quality control.
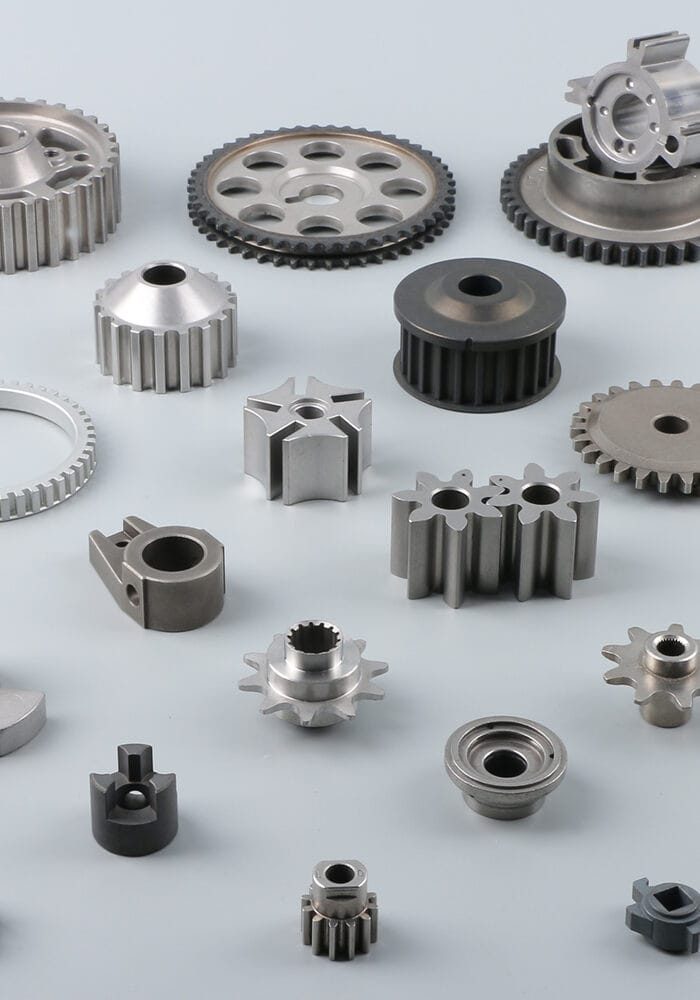
PM Parts
BLUE offers high-precision, strong powder metallurgy parts, customized to meet strict quality standards for various applications.
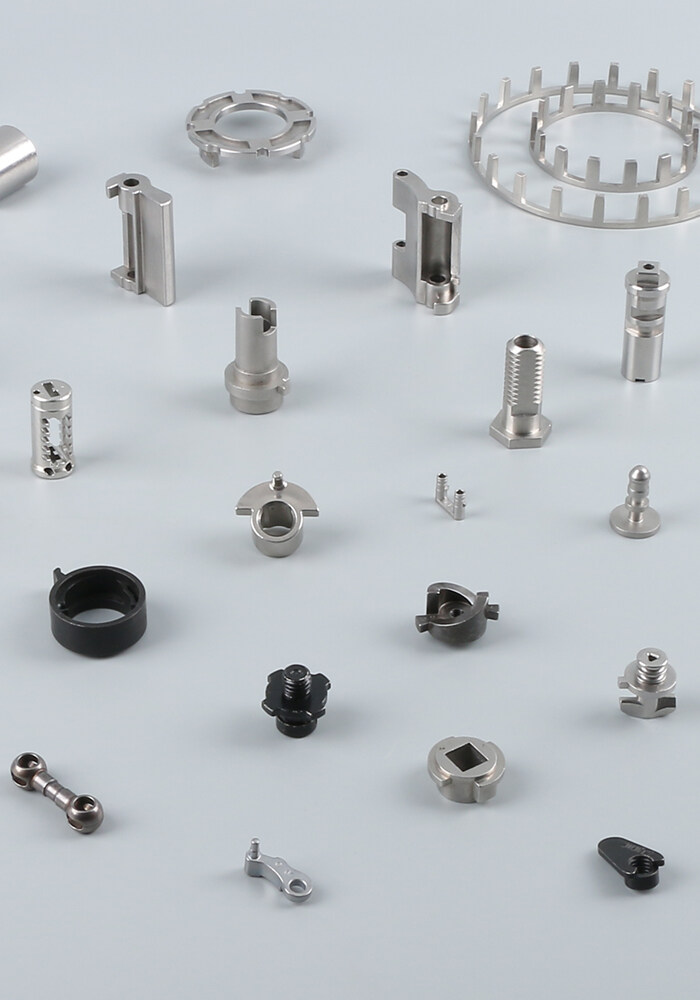
MIM Parts
BLUE's MIM parts feature flexible designs and top strength, produced with consistent quality for complex requirements.
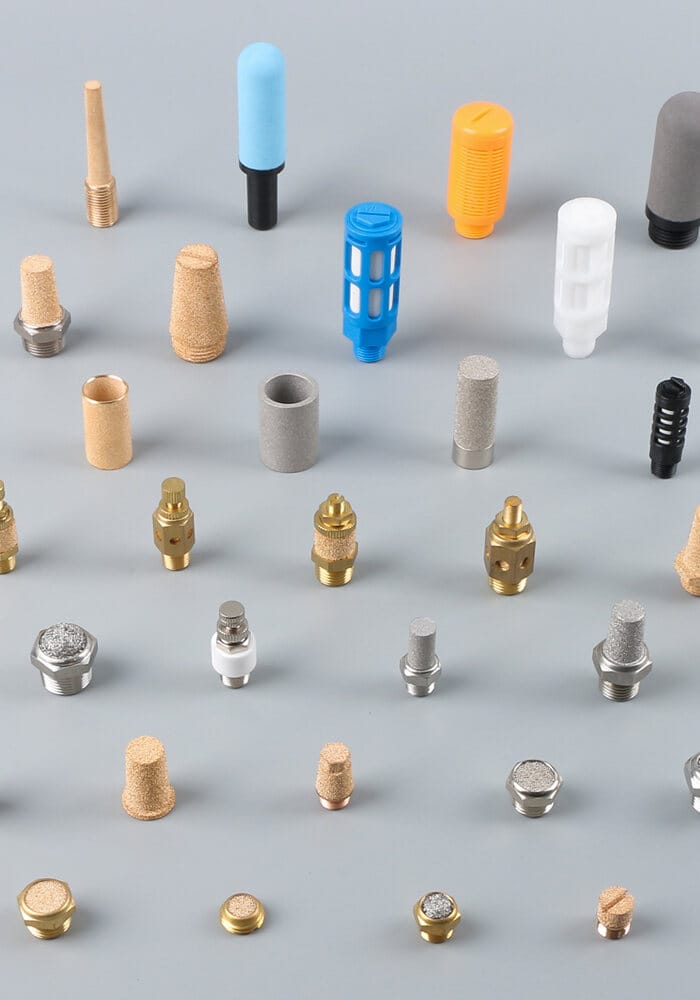
Sintered Filters
BLUE's sintered filters are designed to resist corrosion, so it can perform reliably and durable even in harsh chemical environments.
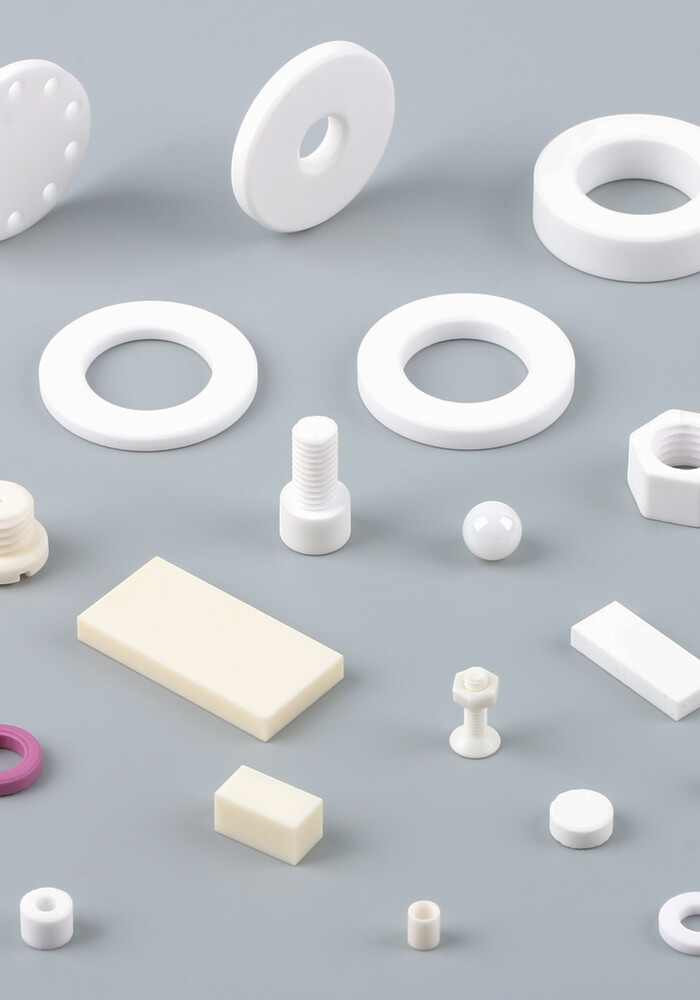
Sintered Ceramics
BLUE's sintered ceramics offer excellent resistance to high temperatures and corrosion, along with good strength, hardness, and surface finish.
Custom Powder Metallurgy Parts Gallery
Here are some BLUE’s customized powder metallurgy parts, including water pump pulleys & flange, oil pump rotors & gears, sintered metal filters, shock absorber parts, oil-impregnated bearings, etc.
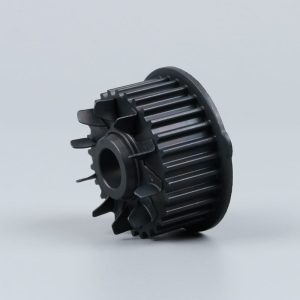
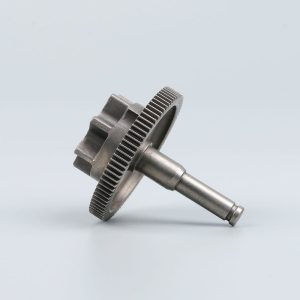
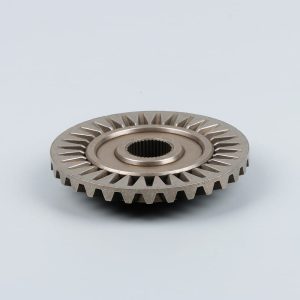
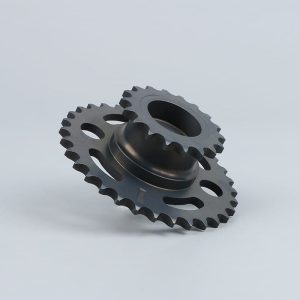
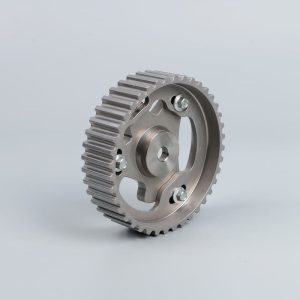
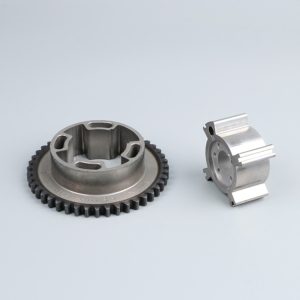
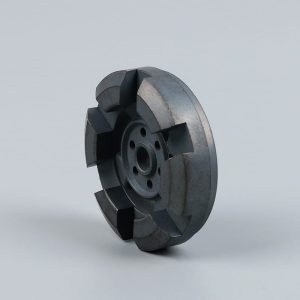
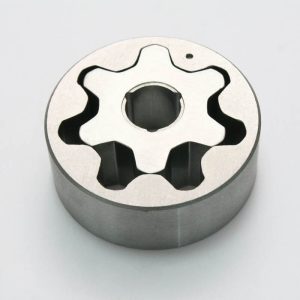
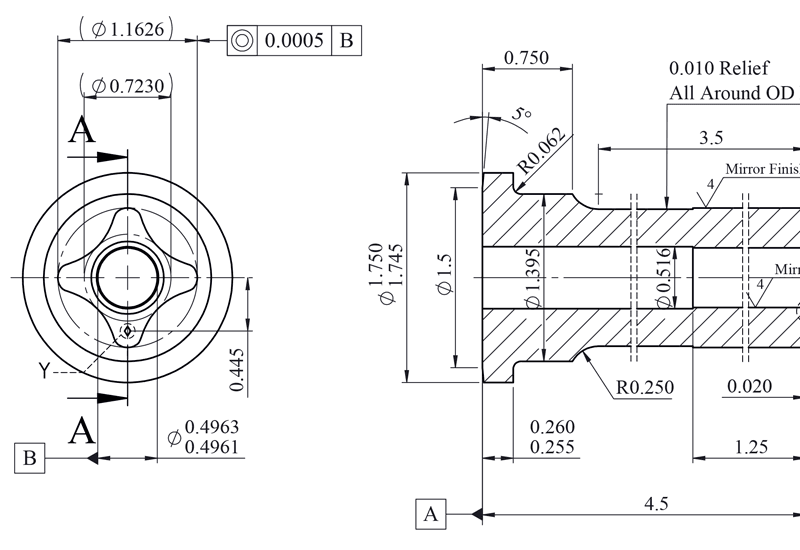
PM Design Guidelines
- Size: Customized powder metallurgy parts with radial dimensions ranging from 5 to 250 mm and heights up to 200mm are available.
- Chamfer: Customized PM part edges should be chamfered rather than rounded, and the chamfer angle is generally 30°-45°.
- Sharp corners: To prevent punch breakage, avoid sharp corners in your design and finish with a small step, at least 0.20mm wide.
- Wall thickness: Too thin wall thickness will cause components cracks during pressing, and the minimum is 1.50mm.
- Taper angle, or draft angle, is the slight slope added to the mold and punch for easier part removal after pressing, typically ranging from 1 to 3°.
- Side holes usually require secondary processing after sintering.
Custom Powder Metallurgy Parts Materials
BLUE’s powder metallurgy materials strictly comply with MPIF Standard 35. We source partial metal powders from top European and American suppliers, like Höganäs and Rio Tinto, to ensure your parts meet the same high-quality standards as local suppliers.
We provide you with a wide range of PM materials to choose from, such as:
- Iron-based mixed powders: FC-0205, FN-0205, FD-0205, FLC-4608, and more.
- Copper-based mixed powders: 660 Bronze, 663 Bronze, CT-1000, etc.
- Iron & copper mixed powders: FX-1005, FX-2005.
- Stainless steel mixed powders: SS 304, SS 316, SS 410, and others
Feel free to contact our engineers if you have any questions about PM materials.
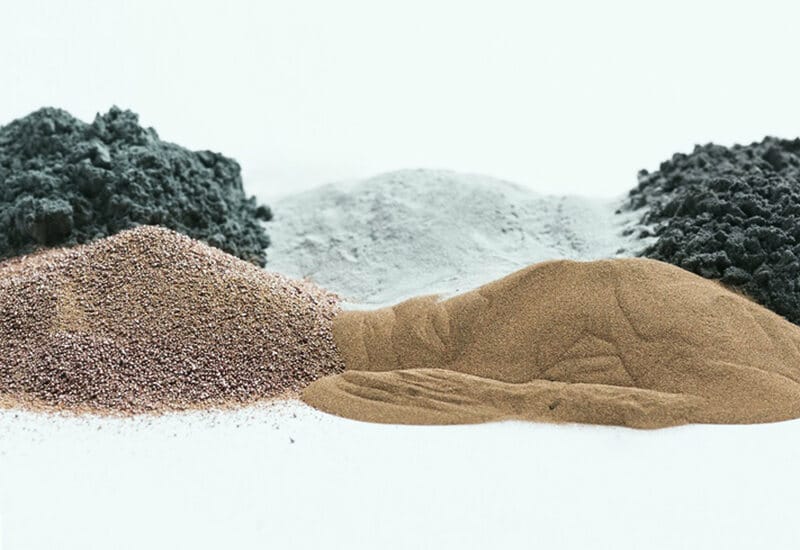
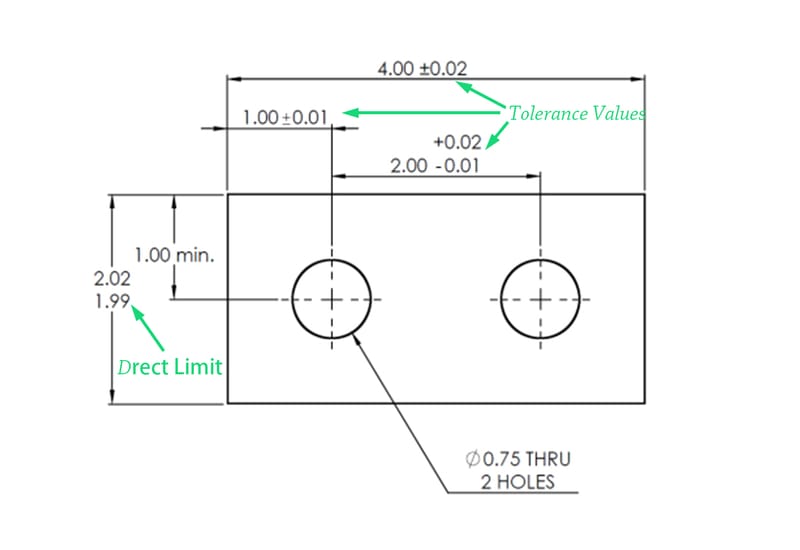
Powder Metallurgy Tolerances
As a leading powder metal parts manufacturer, BLUE produces your parts with tight tolerances of up to ±0.01 mm, in compliance with ISO 2768.
BLUE’s sintered products can achieve radial tolerances of IT8-IT9. After the sizing process, our customized powder metallurgy parts can reach tolerances of T5-IT7. This is made possible by our highly precise molds and advanced production process management.
PM form and orientation tolerances: roundness ±0.03mm, concentricity ±0.05mm, verticality ±0.05mm.
CNC Machining
CNC machining allows us to achieve the final tolerances, complex shapes, and high-precision features that compacting and sintering alone can’t deliver.
While powder metallurgy produces complex shapes, certain features—like threads, undercuts, or transverse holes—are difficult to form during compacting.
With CNC machining, we can add these features post-sintering.
For sintered parts with rough surfaces, such as burrs or flashes, our grinding capabilities provide the smooth, refined surface finish.
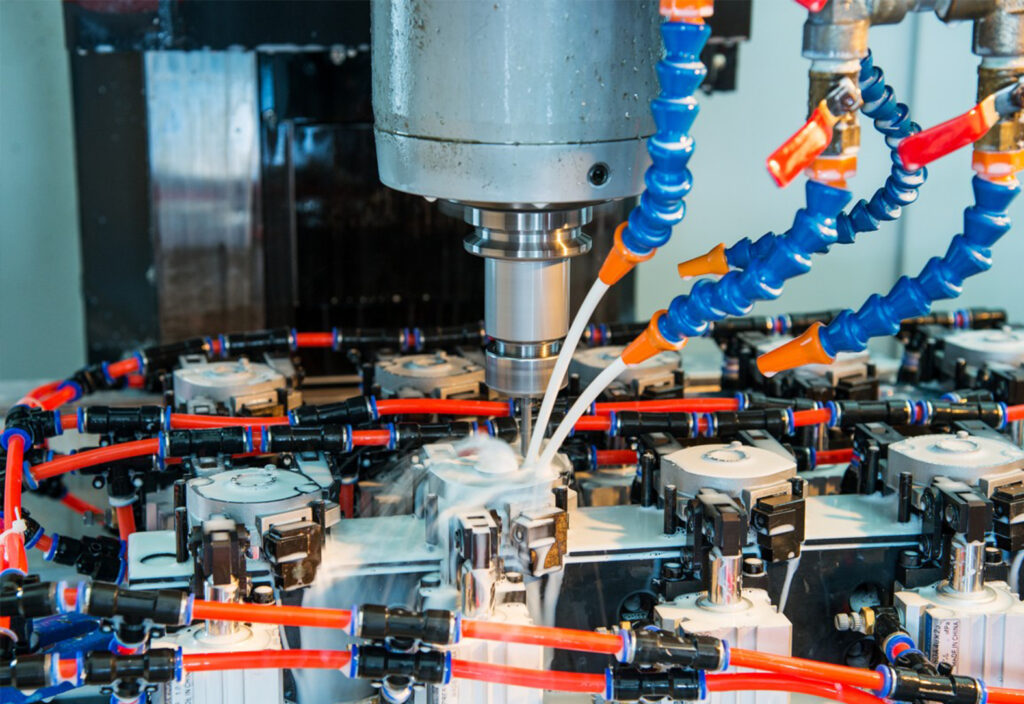
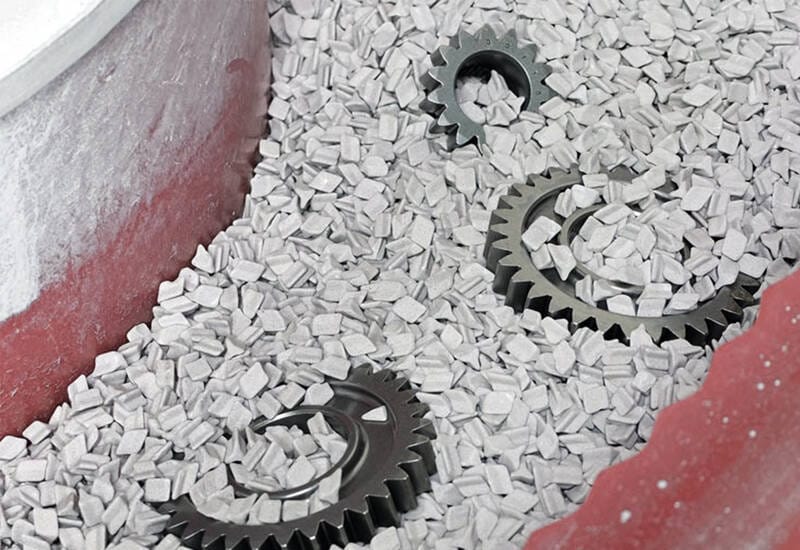
Various Surface Treatments Available
BLUE offers a range of surface treatment processes to enhance surface finish, durability, and performance of your sintered parts, including:
- Steam treatment is an economical rust prevention method for iron-based parts, and it can also increase hardness to HRB 60-90.
- Electroplating is commonly used to improve corrosion resistance. Commonly used are nickel plating, chrome plating, zinc plating.
- Dacromet process offers superior corrosion resistance compared to electroplating, with very stable anti-rust performance.
- Tumble finishing can remove burrs and flash of powder metallurgy parts to improve their surface smoothness.
For powder metallurgy products, internal pores must be sealed before electroplating, as the solution can easily cause internal corrosion. Dacromet avoids this issue, making it the recommended choice.
Equipment for Customizing Powder Metallurgy Parts
BLUE has a complete range of advanced powder metallurgy production equipment, including 25T to 1000T compaction press, conveyor belt sintering furnace, vacuum sintering furnace, sizing press, CNC machining equipment, Machine Center, hardening furnace, etc.
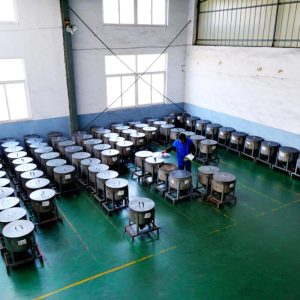
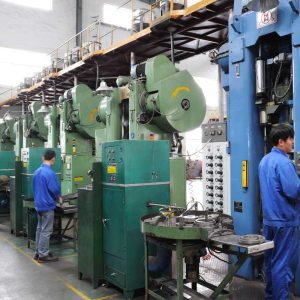
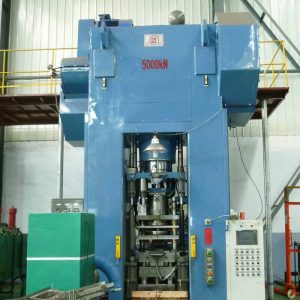
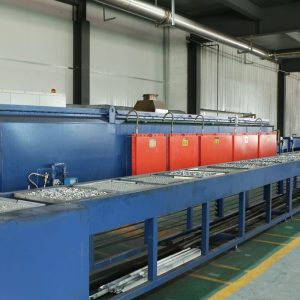
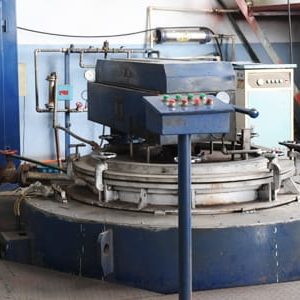
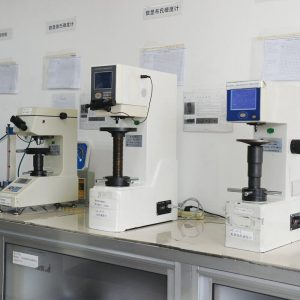
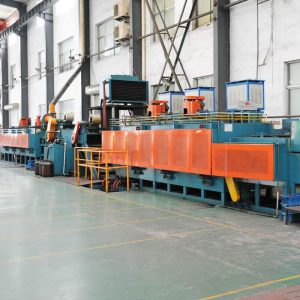
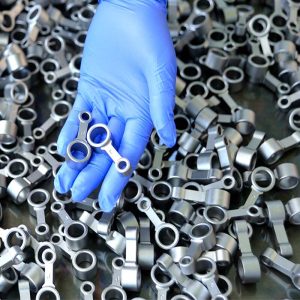
BLUE Custom Powder Metallurgy Part Processes
Powder metallurgy is a precision manufacturing process with a continuing and stable accuracy of up to 0.01mm, which requires strict control at each stage to ensure the quality of the final part. Any deviation or error during the process may result in the rejection of the entire batch.
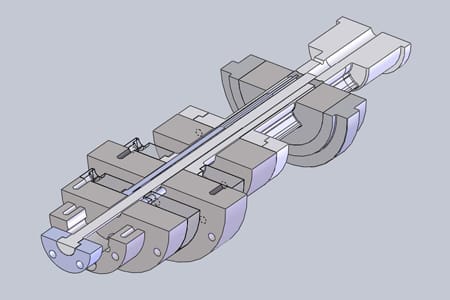
Designing
Mold design is a critical process that must consider the desired part geometry, material properties, production volume, and cost-effectiveness.
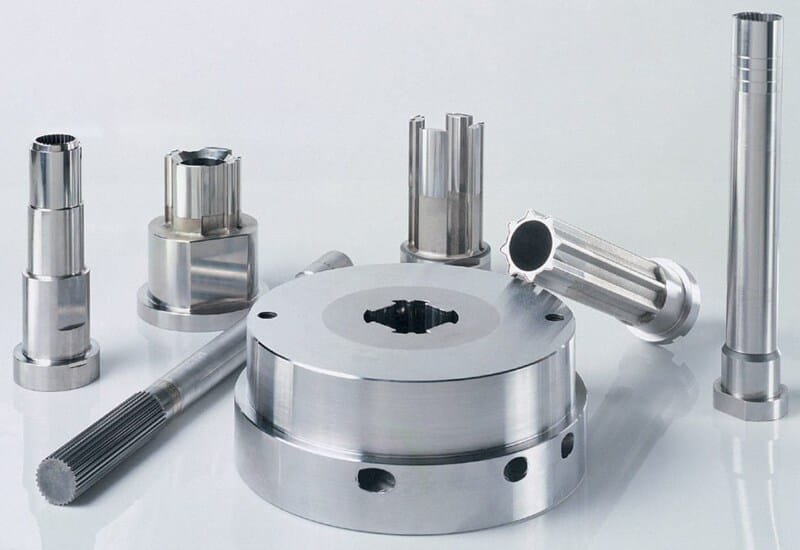
Tooling
Powder metallurgy tooling includes upper and lower punches, die, and core rod. The mold needs to have excellent strength, hardness and wear resistance.
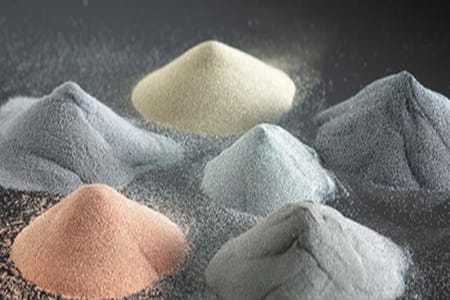
Mixing
Mixing is the process of blending metal powder with binders to improve its uniformity and fluidity, promoting better material consistency.
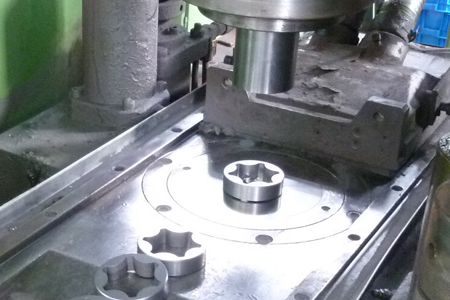
Compacting
Conpacting is a process that presses metal powder into mold cavity through powder compaction machine to get a green compact part.
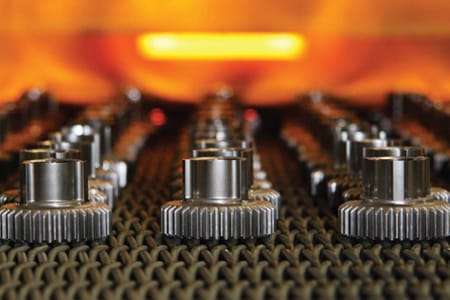
Sintering
Sintering heats the green compact to a temperature below its melting point in a controlled atmosphere to obtain the desired mechanical properties.

Sizing
Sizing corrects dimensional deviations after sintering and enhances product accuracy. It requires an additional, simpler set of molds compared to the forming mold.
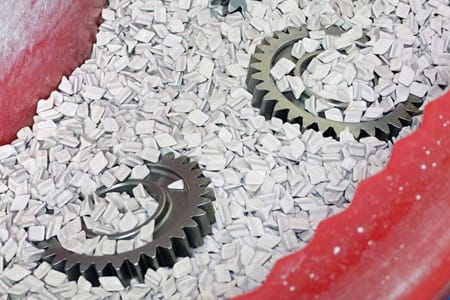
Tumbling
Tumbling removes burrs and flash from a part's surface by vibrating it with abrasive media, such as stone or ceramic, resulting in a smoother finish.
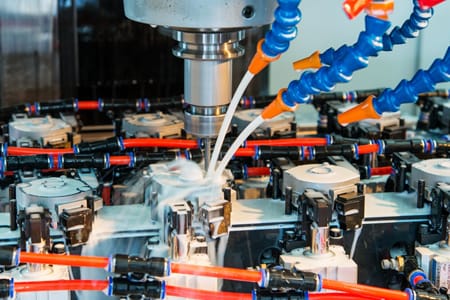
Machining
Machining can achieve complex shapes that cannot be pressed by powder metallurgy, such as transverse holes and screw threads.
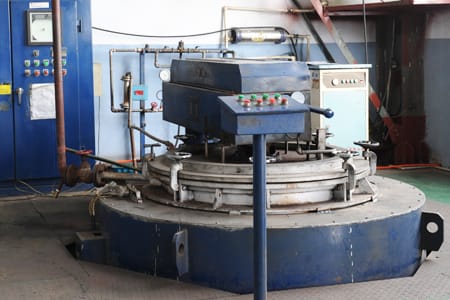
Blackening
Blackening process, or steam treatment, forms an oxide layer to prevent rust and increase hardness, offering a cost-effective solution.
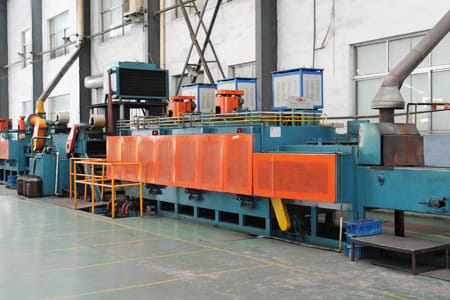
Hardening
Hardening enhances the material's strength and hardness through carburizing or nitriding, resulting in improved wear resistance and fatigue life.
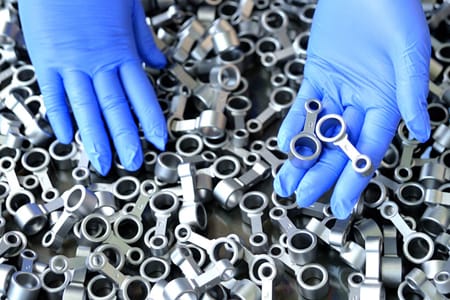
Inspecting
The inspecting process is always a critical step that ensures quality and performance through BLUE inspection standards before shipping.
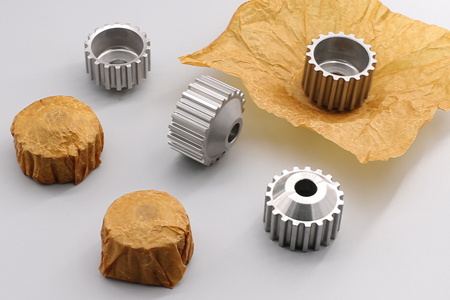
Packaging
BLUE's packaging process uses anti-rust paper, vacuum, blister and other methods to ensure that the product is intact during transportation.
Applications of Customized Powder Metallurgy Parts
Powder metallurgy parts have a wide range of applications, including automobiles, motorcycles, aerospace, medical fields, powder tools, household appliances, etc.
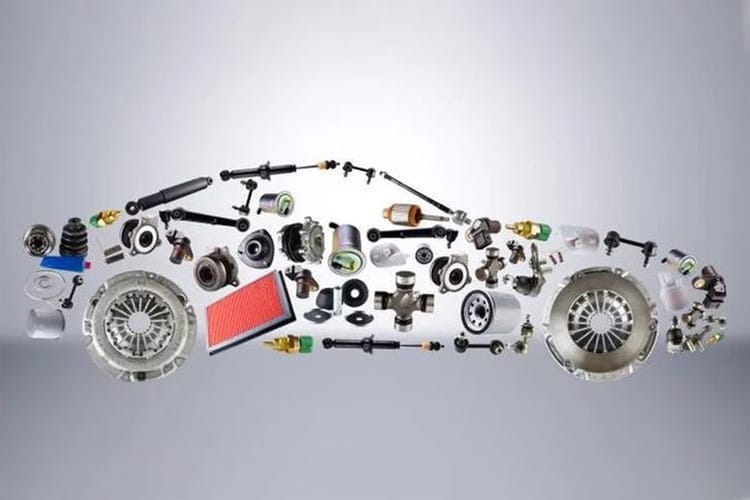
Powder Metallurgy in Automotive Applications
With the advancement of technology, powder metallurgy in automotive applications is becoming more widespread. Do you know how many powder metal parts are in an
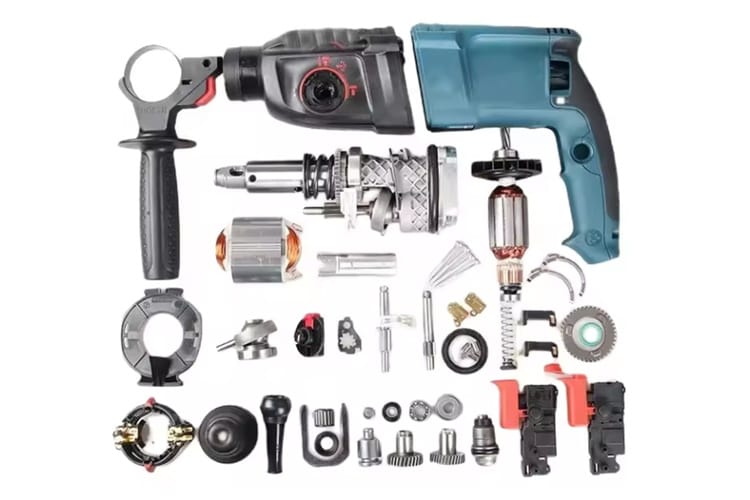
Powder Metallurgy Applications in Power Tools
Power tools make everyday work tasks a lot easier. Today, power tools are moving towards being compact, lightweight, and safe. This naturally goes hand in
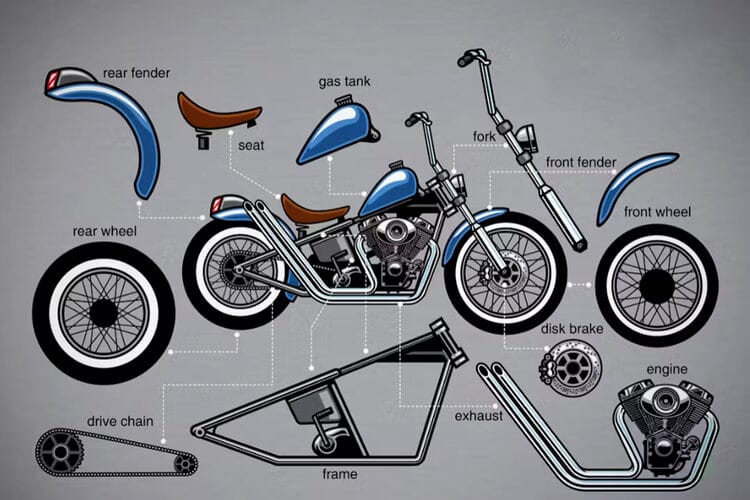
Powder Metallurgy Applications in Motorcycles
Motorcycling is closer to nature and easier to maneuver than driving. Many young people like this cool and exciting mode of transportation. Motorcycles are also
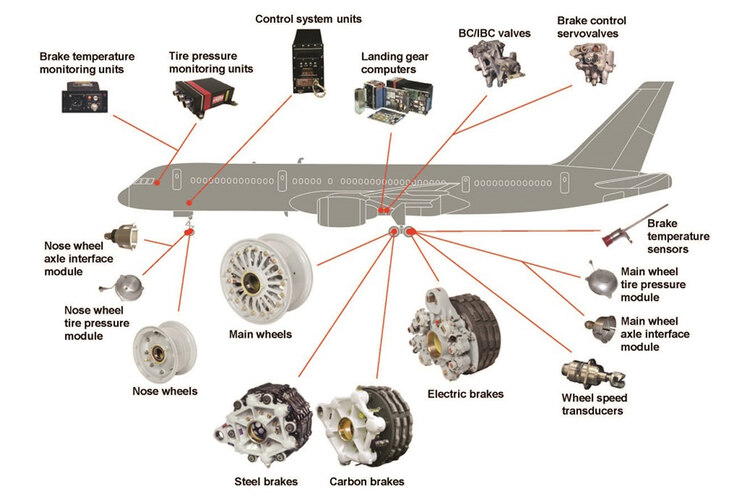
Powder Metallurgy Applications in Aerospace
You may have heard that powder metallurgy (PM) is widely applied in the mechanical industry. But do you know about powder metallurgy applications in aerospace?
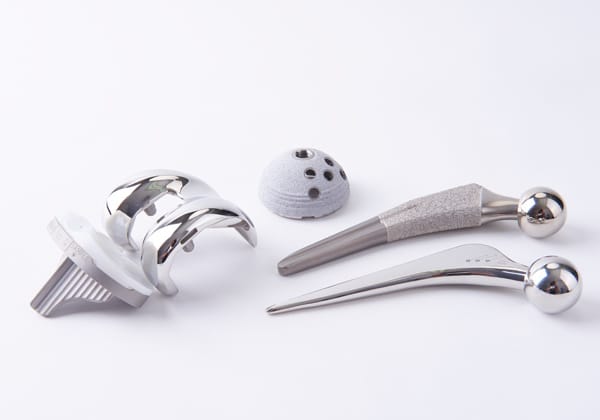
Metal Injection Molding (MIM) Medical Applications
As the population ages, the health of the elderly deserves more attention. This is inseparable from advanced medical technology and equipment. It goes without saying
FAQ's
Here are some of the questions we get asked often. If yours isn’t answered, don’t hesitate to contact us, we’re happy to help!
Powder metallurgy is a cost-effective way to mass produce parts.
Moreover, custom powder metallurgy parts can be made with high precision and complex shapes.
PM has less secondary processing and high material utilization, and is a green manufacturing process.
If BLUE is required to provide mold design, it will take about 3 days. Mass production of customized powder metallurgy parts, including mold manufacturing, typically takes around 20-30 days.
Powder metallurgy standard parts are developed collaboratively by BLUE and various powder metallurgy factories, eliminating the need for new mold development. This not only saves on mold costs but also speeds up production time.