Synchronizer Sleeve OEM & ODM Company - BLUE
BLUE synchronizer sleeves offer high surface hardness, precise internal splines, excellent strength, and durability. Manufacture for the aftermarket, our standard synchronizer sleeves come with no mold fees.
Why Choose BLUE?
BLUE provides top quality synchronizer sleeves with high strength and good durability, and free mold design services—your trusted OEM & ODM supplier.
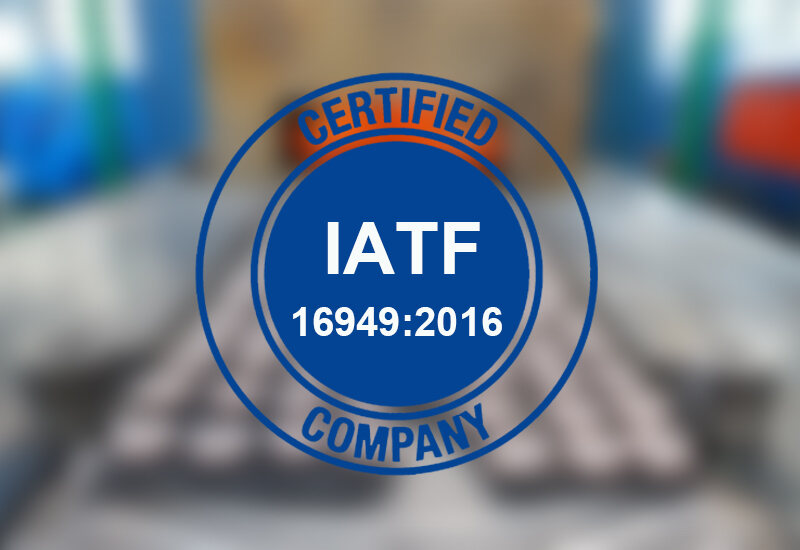
BLUE High Quality Standards
BLUE guarantee the quality of your sintered synchronizer sleeves with an IATF 16949: 2016 certified quality management system. Free samples are available for testing.
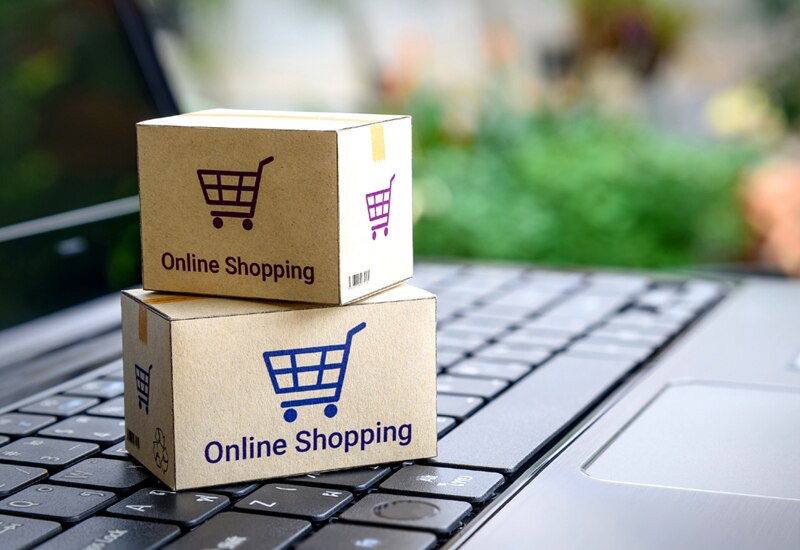
Standard PM Parts Shop
BLUE has a full range of standard PM parts in stock for fast delivery. Visit our standard parts shop to find the exact match for your applications.
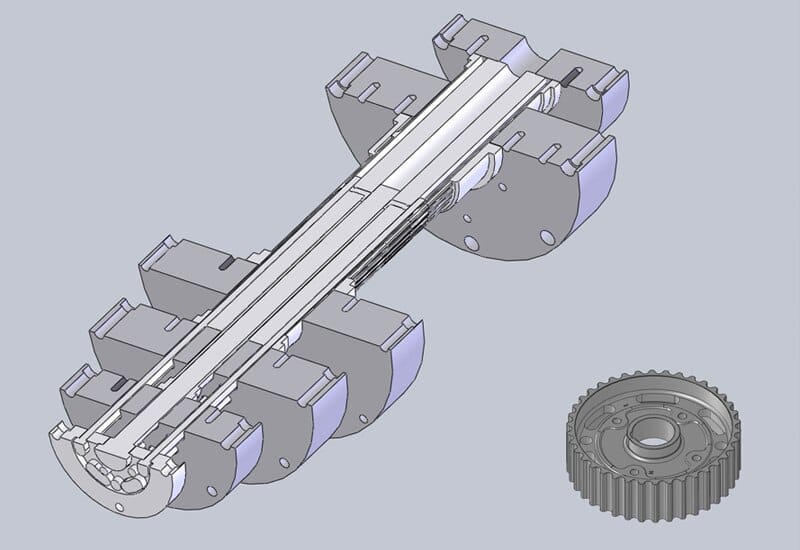
Free Mold Design Service
With over 20 years of expertise, BLUE provides free, high-precision mold design services tailored to your needs. Trust our experience to deliver for you!
BLUE Synchronizer Sleeve in China
BLUE offers a wide range of synchronizer sleeves for manual and automatic transmissions.
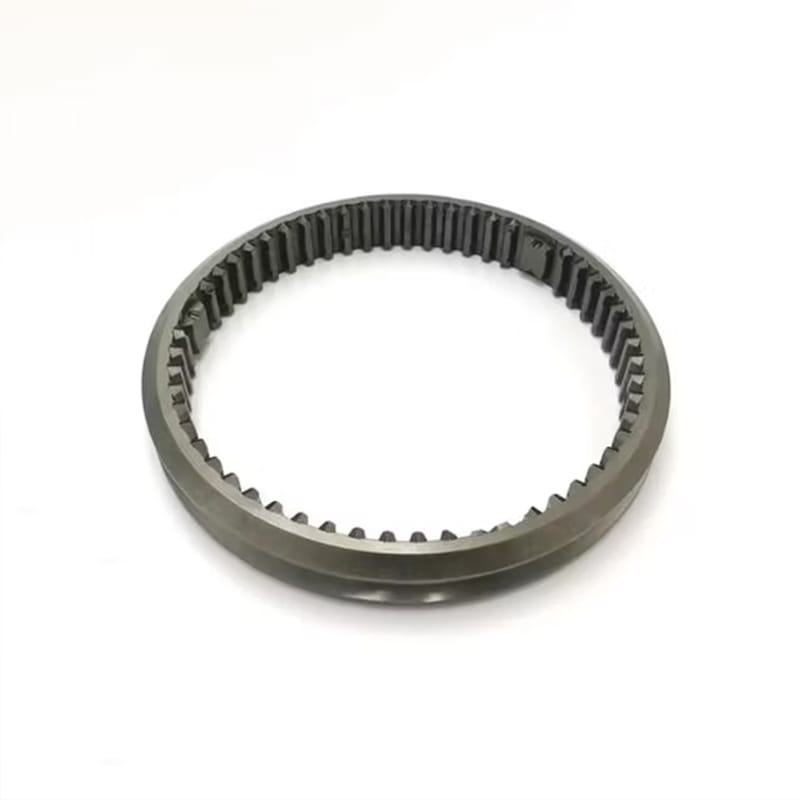
Powder Metallurgy Synchronizer Sleeve
Powder metallurgy synchronizer sleeves have the advantages of near net shape, tight tolerance and high tooth profile accuracy.
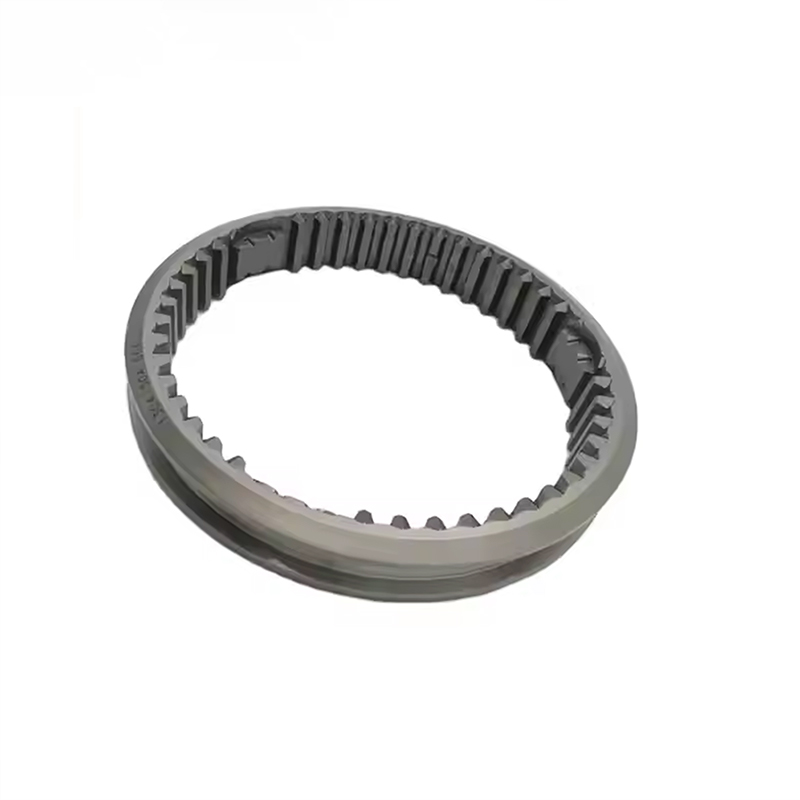
Sintered Synchronizer Sliding Sleeve
Sintered synchronizer sliding sleeves are made from metal powder raw materials and formed into its final shape through single compaction.
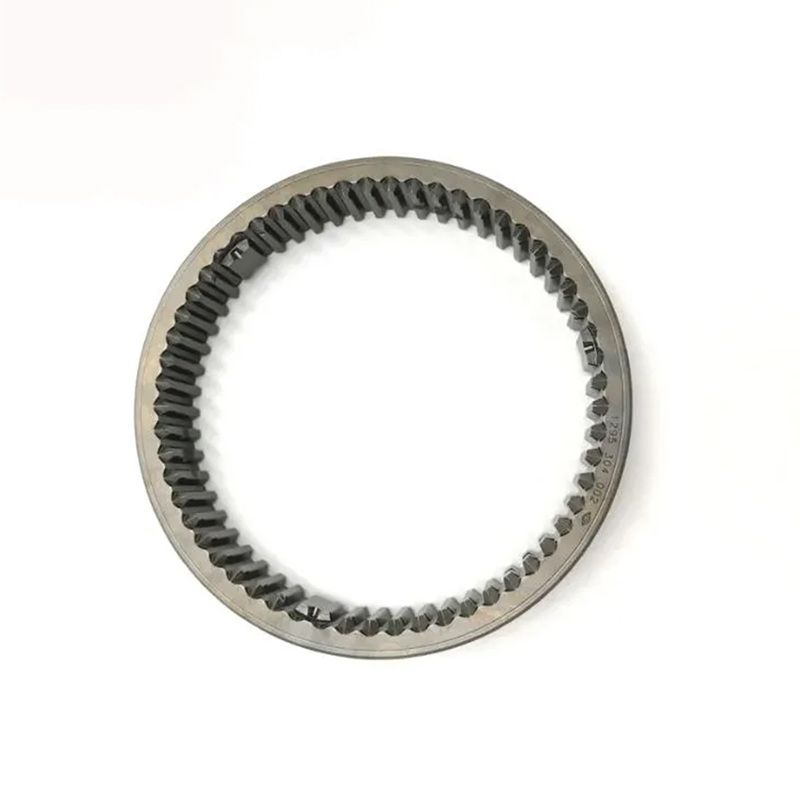
Powder Metal Synchronizer Sleeve
BLUE powder metal synchronizer sleeves have precise internal splines and ensure smooth speed changes with other synchronizer parts.
BLUE Synchronizer Sleeve Features
BLUE synchronizer sleeves are manufactured under the control of the IATF 16949:2016 system.
Our sintered synchronizer sleeves are available in various types for manual and dual-clutch transmissions.
BLUE’s sintered synchronizer sleeves feature a density of up to 7.2 g/cm³ and good mechanical strength.
Our synchronizer hubs are manually deburred and vibrated to achieve good surface roughness.
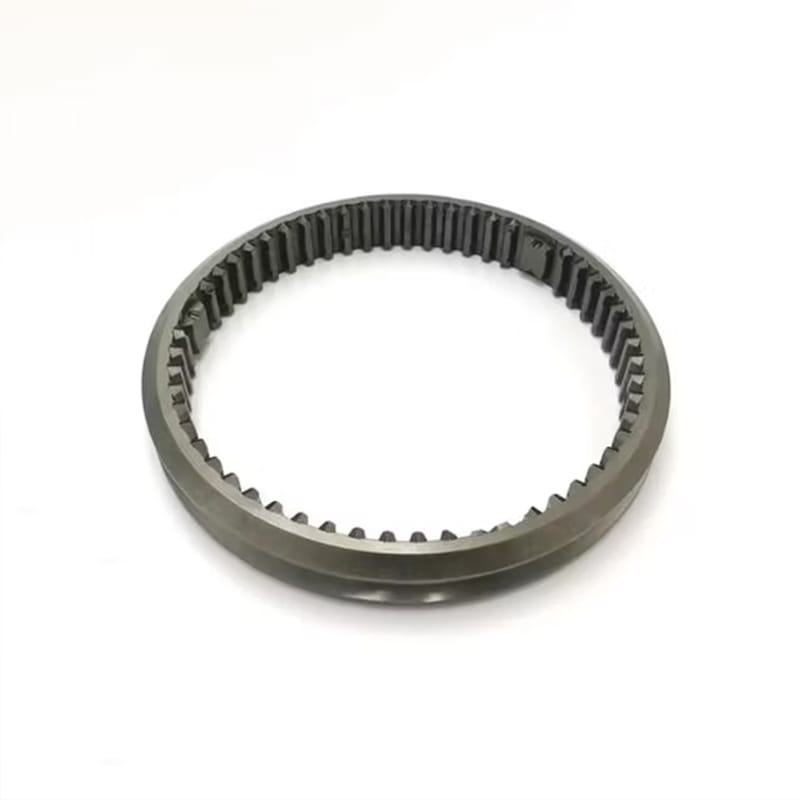
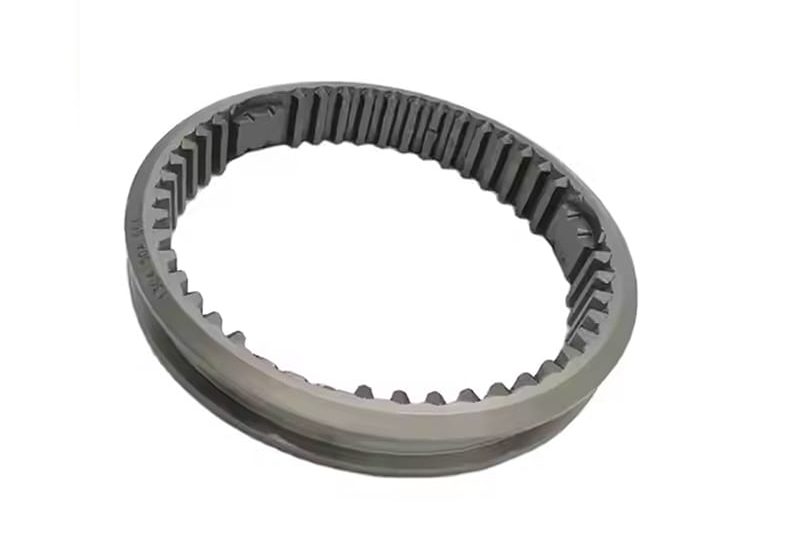
Post-Sintering Processes
BLUE offers the following post-sintering processes to enhance the mechanical and physical properties of synchronizer sleeves.
- Heat Treatment: Alters the internal microstructure of the material to improve hardness, strength, toughness, and ductility.
- Copper Infiltration: Fills the pores of sintered sliding sleeves with molten copper, increasing density, strength, and wear resistance.
- Steam Treatment: Commonly applied to iron-based parts, it forms a thin oxidized surface layer (Fe3O4), enhancing wear resistance, corrosion protection, and surface hardness.
Adavantages of PM Synchronizer Sliding Sleeve
Near-Net Shape
Powder metallurgy enables the direct formation of the internal spline shape of the synchronizer sleeve through pressing, minimizing the need for secondary processing.
Tight Tolerances
Sintered synchronizer sliding sleeves feature precise dimensional tolerances and high tooth profile accuracy.
Consistent Quality
Powder metallurgy assures excellent quality consistency for synchronizer sliding sleeves in large-scale production.
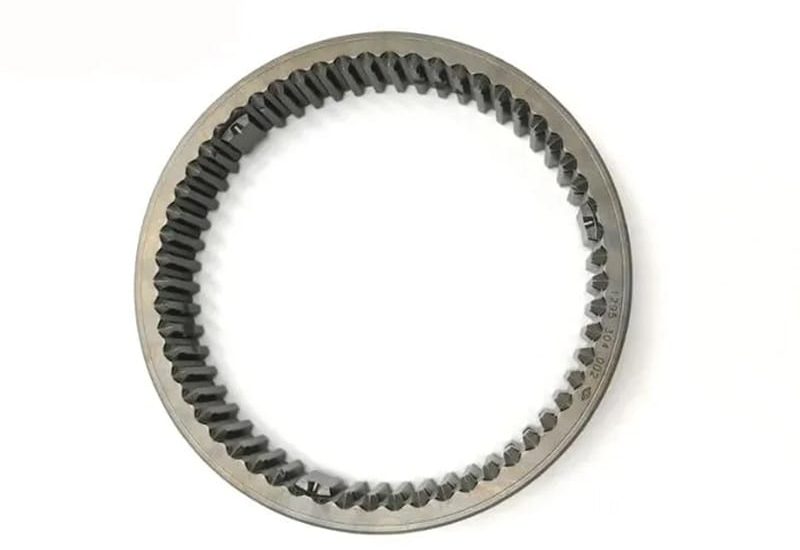
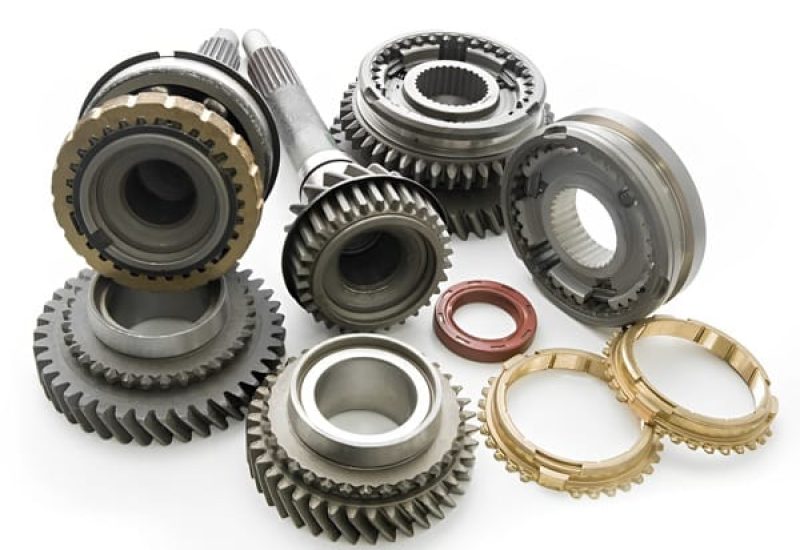
What is a Synchronizer Sleeve?
The synchronizer sliding sleeve is a component of the vehicle’s transmission system.
It slides along the synchronizer hub to engage the selected gear, locking it to the transmission shaft.
Sliding sleeve works with the synchronizer ring to match the gear and shaft speeds, ensuring smooth and wear-free meshing.
Once engaged, it transfers torque from the gear to the shaft.
Custom Synchronizer Sleeve Specifications
This table shows our manufacturing capabilities for customized synchronizer sleeves, including material, density, hardness, tolerance, and surface treatment.
Attribute | Value |
---|---|
Material | FC-0205, FN-0205, SMF4040, SMF9060, D39 |
Density | 6.8-7.0g/cm3 |
Hardened Hardness | Min. 40 HRC |
Tolerance | ±0.01 mm |
Tooth Accury | DIN/ISO 6 – 8 |
Powder Metallurgy Manufacturing Process
Powder metallurgy is a precision manufacturing process with a continuing and stable accuracy of up to 0.01mm, which requires strict control at each stage to ensure the quality of the final part. Any deviation or error during the process may result in the rejection of the entire batch.
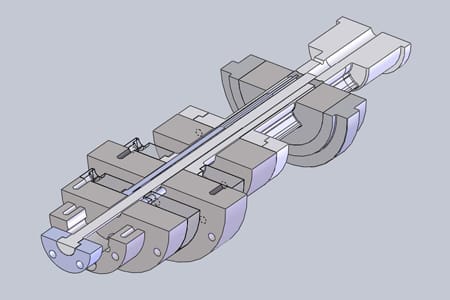
Designing
Mold design is a critical process that must consider the desired part geometry, material properties, production volume, and cost-effectiveness.
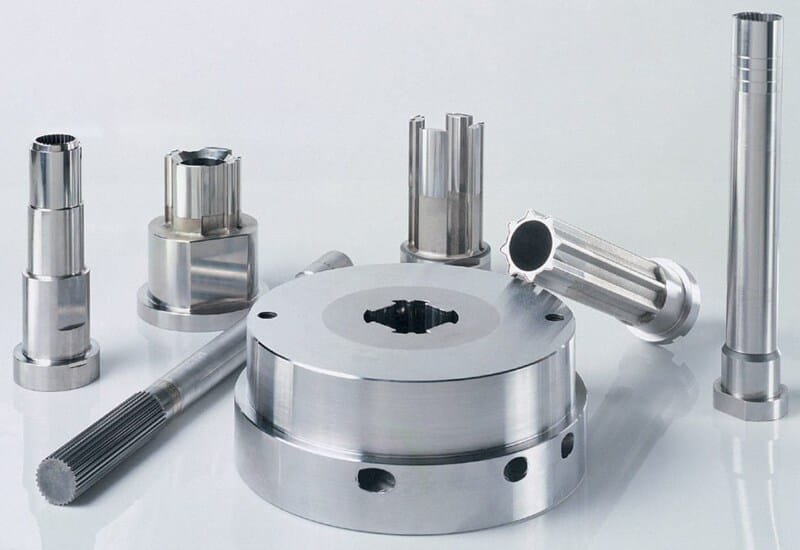
Tooling
Powder metallurgy tooling includes upper and lower punches, die, and core rod. The mold needs to have excellent strength, hardness and wear resistance.
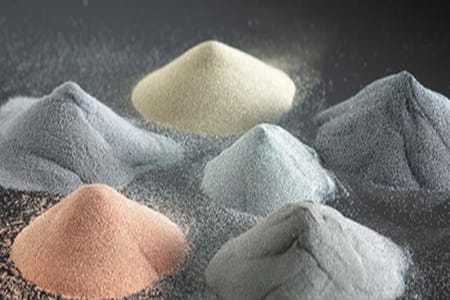
Mixing
Mixing is the process of blending metal powder with binders to improve its uniformity and fluidity, promoting better material consistency.
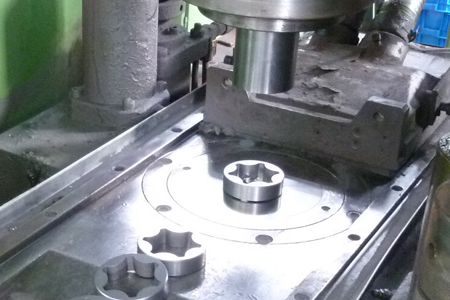
Compacting
Conpacting is a process that presses metal powder into mold cavity through powder compaction machine to get a green compact part.
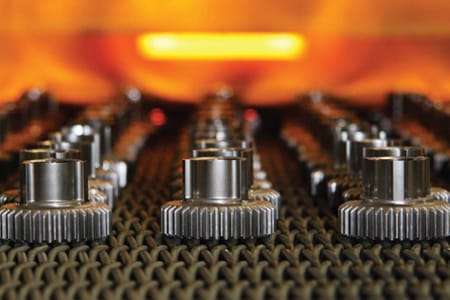
Sintering
Sintering heats the green compact to a temperature below its melting point in a controlled atmosphere to obtain the desired mechanical properties.

Sizing
Sizing corrects dimensional deviations after sintering and enhances product accuracy. It requires an additional, simpler set of molds compared to the forming mold.
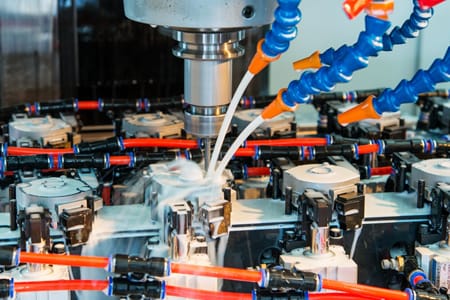
Machining
Machining can achieve complex shapes that cannot be pressed by powder metallurgy, such as transverse holes and screw threads.
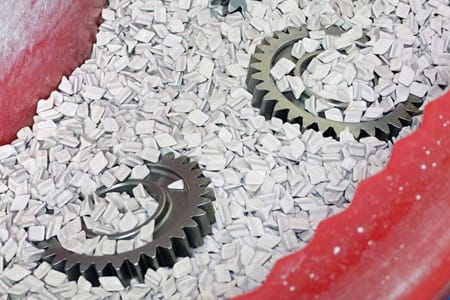
Tumbling
Tumbling removes burrs and flash from a part's surface by vibrating it with abrasive media, such as stone or ceramic, resulting in a smoother finish.
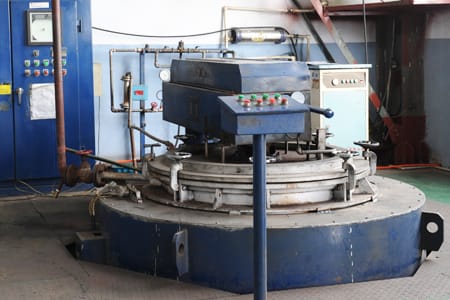
Blackening
Blackening process, or steam treatment, forms an oxide layer to prevent rust and increase hardness, offering a cost-effective solution.
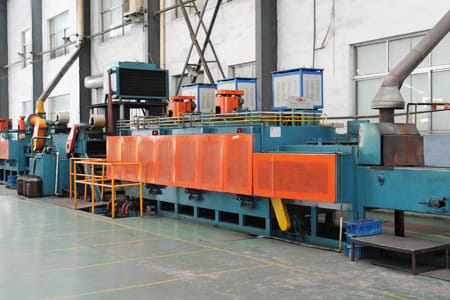
Hardening
Hardening enhances the material's strength and hardness through carburizing or nitriding, resulting in improved wear resistance and fatigue life.
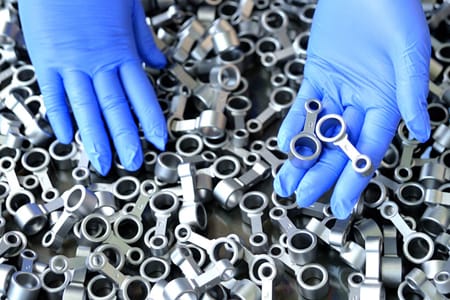
Inspecting
The inspecting process is always a critical step that ensures quality and performance through BLUE inspection standards before shipping.
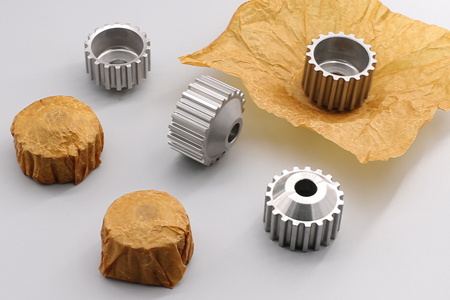
Packaging
BLUE's packaging process uses anti-rust paper, vacuum, blister and other methods to ensure that the product is intact during transportation.
BLUE's Powder Metallurgy Manufacturing Equipment
BLUE has a complete range of advanced powder metallurgy production equipment, including 25T to 1000T compaction press, conveyor belt sintering furnace, vacuum sintering furnace, sizing press, CNC machining equipment, hardening furnace, etc.
Related Powder Metallurgy Auto Parts
As a leading powder metallurgy supplier in China, BLUE provides a variety of standard PM parts, including valve seats, oil pump rotors and gears, synchronizer hubs, and timing chain sprockets, all without tooling fees.
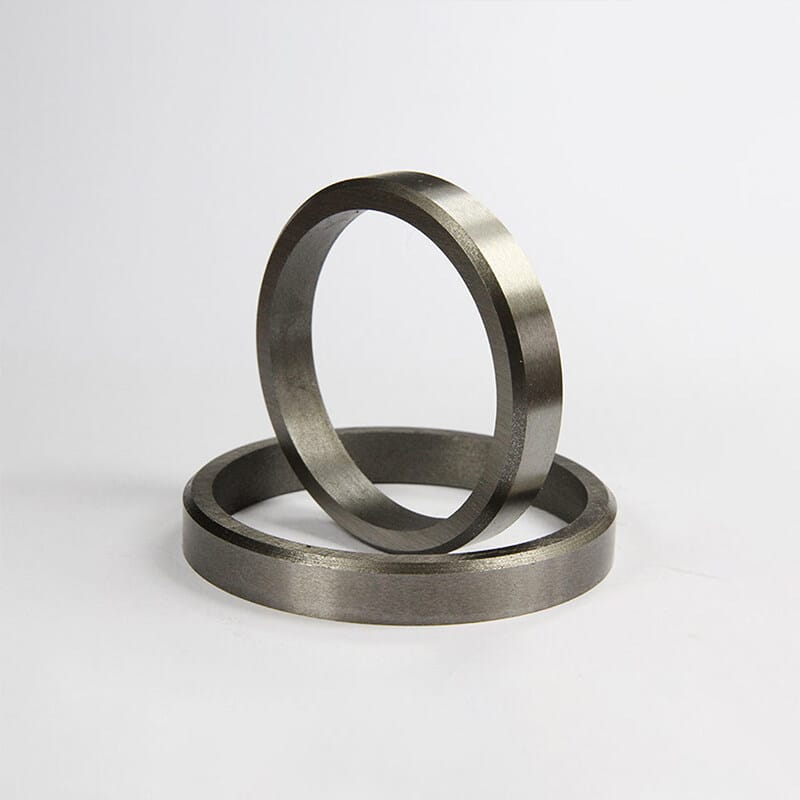
Valve Seat
Valve seat absorbs high speedimpact of the valve while providing a durable, heat-resistant surface that ensures proper sealing for valves.
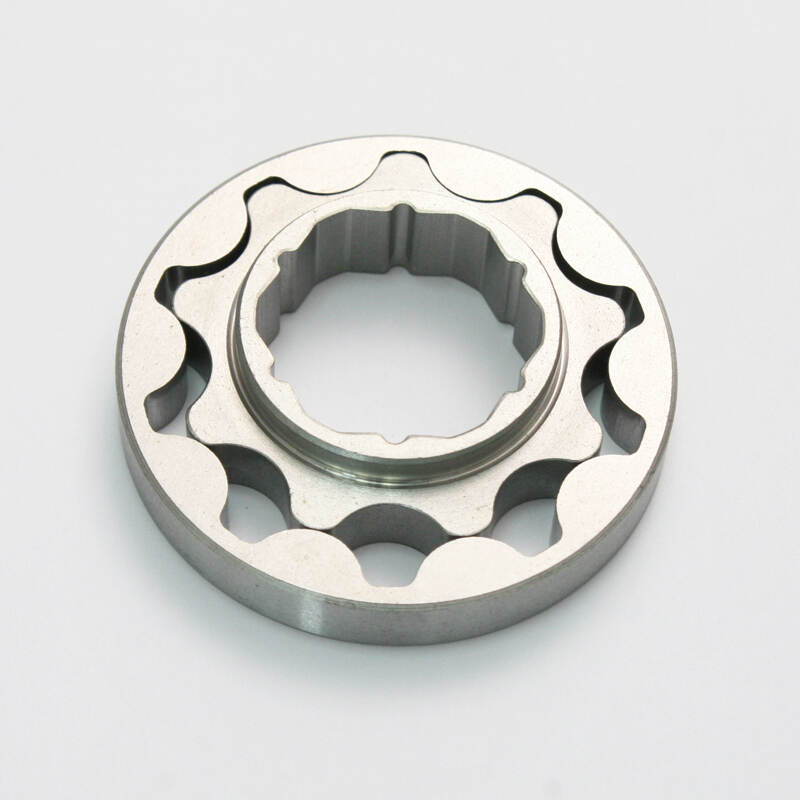
Oil Pump Rotor
Our oil pump rotors have good surface finish, tight dimensional accuracy and excellent position tolerances to deliver optimal engine performance.
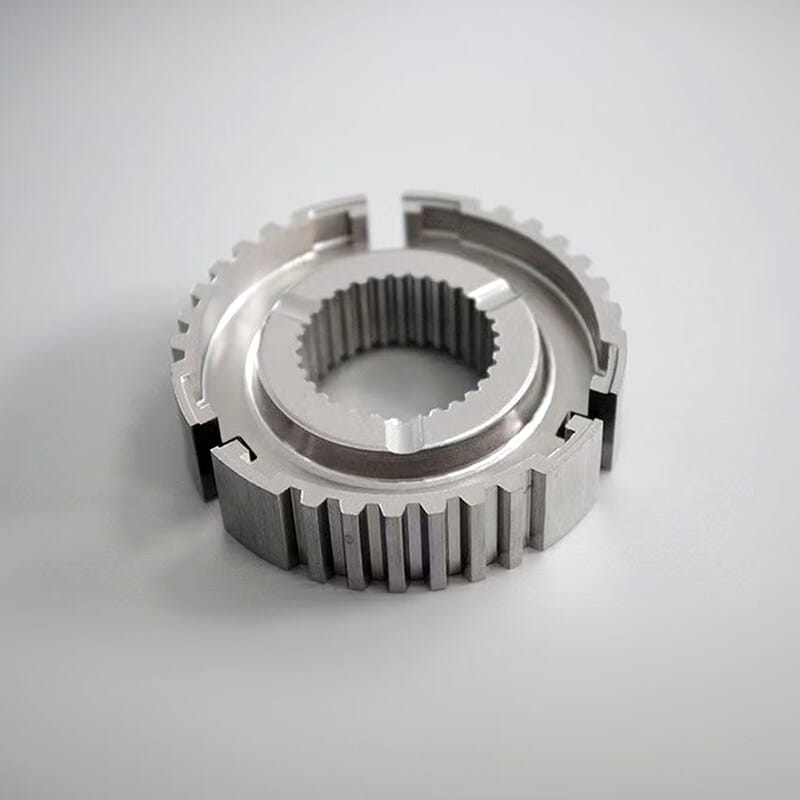
Synchronizer Hub
BLUE synchronizer hubs feature precise internal and external spline tooth profiles, good durability and high strength.
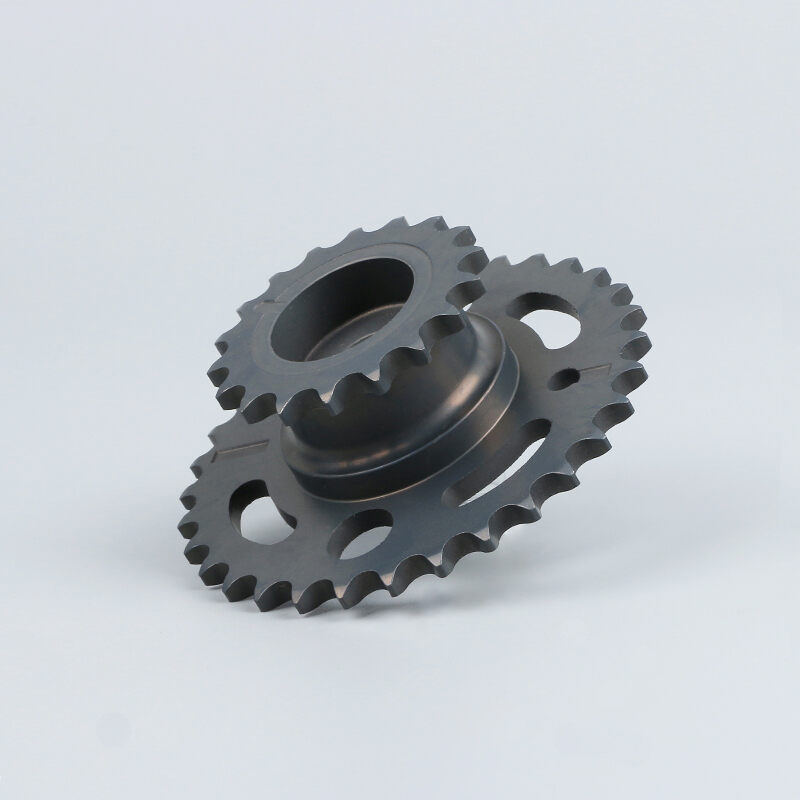
Timing Chain Sprocket
BLUE timing chain sprockets with precision teeth profile and holes, which fit perfectly with your chain and timing sprocket.