Sintering is a great way to boosts parts strength.
However, it is not perfect.
You may require addition features through secondary operations in powder metallurgy (PM).
Secondary processing helps products increase wear resistance, prevent corrosion, control component size, and improve the appearance. We will explore these secondary processes below.
Contents
Common Secondary Operations in Powder Metallurgy
Machining
Machining in powder metallurgy refers to the use of various techniques to shape, finish or refine powdered metal components. Main operations include:
- Drilling is the creation or finishing of holes in powder metal parts.
- Tapping creates threaded holes in components.
- Milling is ideal to remove material from a surface to obtain the desired size and shape.
- Turning shapes part by rotating it relative to a cutting tool, usually done on a lathe.
- Grinding contributes to achieve high precision and smooth surface finish.
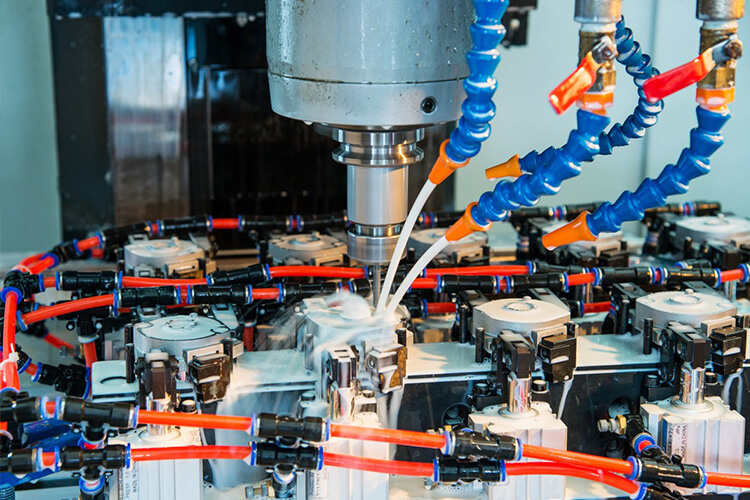
Sizing
Parts coming out of the sintering furnace may undergo size changes. So you need sizing process to improve part accuracy.
Sizing is a repressing process that allows parts achieve tighter tolerances and a better surface finish. Sometimes, sizing can achieve 50% higher accuracy than sintering process alone.
Impregnating
When applied to bearings and bushings, impregnation aids in lubrication. It reduces friction and wear during operation of the part.
Impregnation uses oil or resin to fill the pores of sintered metal parts.
After impregnation, you should seal the parts to prevent oil leakage and ensure long-term stability.
Deburring
Burrs are small, rough edges or projections that form on sintered component during manufacturing. These imperfections are typically found along the edges.
You have to remove these burrs, or they will cause serious problems.
- Sharp burrs may pose a risk of injury to workers handling the components.
- Burrs can lead to increased friction, wear and potential failure in the product’s functionality.
- They may interfere with the assembly of product.
Powder metal parts suppliers tend to clear these burrs during secondary operation. They usually utilize rotary brushes with abrasive bristles to remove burrs from surfaces and edges.
Sandblasting
Sandblasting means pushing abrasive materials like sand, silicon carbide, or steel grit through onto a part’s surface at high speed. When the abrasive hits the surface, it clears oxides and burrs.
It features the following advantages:
- Effective cleaning
Sandblasting thoroughly extracts surface contaminants and improves components cleanliness.
- Enhanced appearance
Sandblast gives components an even and attractive surface finish.
- Versatility
It works well with a variety of materials and part sizes.
Vibratory Finishing
Vibratory finishing works well for enhancing the surface finish and functional properties of sintered parts.
Place your parts into a vibrating container filled with grinding media (metal, ceramic, or stone). Introduce oil and anti-rust water to protect the surface of product. Then you start Vibratory machine and let media against the parts.
You could take advantage of vibratory finishing for the following purposes:
- Smooth Surface
Vibrations remove rough edges, burrs, and surface defects left by sintering to achieve a smooth surface.
- Polishing
Vibrations create a shiny, polished surface that enhances the appearance of your product.
- Improved Functionality
The frequency and amplitude of the machine determine the roughness of the part. The frequency range is 900 to 3600 cycles per minute (CPM). Use high frequency and small amplitude for fine machining or delicate parts, and high amplitude for heavier cuts.
Plating
Plating is a surface finishing process that adds a thin metal layers to powder metallurgy parts.
You immerse parts in a solution containing metal ions. Through the use of electric current and reducing agents, metal ions are deposited onto the surface of the parts.
Plating process offers such benefits.
- Improved corrosion resistance
- Enhanced abrasion resistance
- Improved conductivity
Steam Treatment
Steam treatment, also known as blackening, can help eliminate or reduce corrosive effect. For iron-base sintered components, steam treatment produces a thin and protective oxide layer that prevents rusting.
Expose parts to high-temperature vapors, usually between 510°C and 570°C (950°F and 1060°F), to form a protective oxide layer, typically Fe3O4, on the surface. This oxide layer can improve:
- Corrosion resistance
It acts as a barrier against corrosion, significantly extending the lifespan of the part.
- Wear Resistance
Steam treatment hardens the surface of components, improving wear resistance.
- Sealing Pores
It is beneficial to seal the surface pores.
Dacromet
In powder metallurgy process, plating and blacking have limited applications. If you want better corrosion protection and appearance, you can apply Dacromet coating. It is a type of sacrificial coating in powder metallurgy with excellent corrosion resistance. This water-based, zinc-rich coating provides a protective barrier for your product.
First, clean the components to remove contaminants like oil, oxides, and dirt. Next, dip the components into the Dacromet solution and spin them to remove excess coating. Finally, dry the parts at room temperature or in a ventilated area to remove moisture.
You can apply Dacromet coating to your product through methods such as dip-spinning, spraying, or dip-draining. It typically comes in the following materials:
- Metal powders
- Zinc provides galvanic protection to the underlying metal.
- Aluminum enhances barrier protection and reflects heat.
- Chromium Compounds
It act as a binder and delivers additional corrosion resistance.
Benefits of Dacromet.
- This coating supplies excellent protection against rust and corrosion for your parts, especially in harsh environments.
- It could withstand high temperatures above 300°C without degradation.
- Dacromet is eco-friendly and does not contain harmful substances such as hexavalent chromium.
- It has excellent adhesion. It bonds well to a variety of substrates, including steel, aluminum and other metals.
Hardening
Hardening is a process that increases the hardness of metals.
- Carburization
Exposing components to carbon-rich environments, typically containing methane (CH4) or carbon monoxide (CO). The method is done in a furnace with a controlled atmosphere.
Carbon atoms diffuse to the surface of the part at high temperatures, forming a high-carbon, hard outer layer. The temperature typically between 850°C and 950°C (1562°F to 1742°F).
Carburization increases the surface hardness of metal parts while keeping the core tough and ductile. This process is especially beneficial for parts like gears and bearings.
- Nitriding
Nitriding generally heats the part to a lower temperature than carburizing, between 500°C and 600°C (932°F and 1112°F).
Then you expose powdered metal parts to a nitrogen-rich environment. It is usually performed in a furnace in an ammonia (NH3) atmosphere or in a plasma nitriding unit. Nitrogen atoms diffuse to the surface, forming hard nitrides (e.g. iron nitride, alloy nitrides).
Nitriding produces a hard, wear-resistant surface with excellent fatigue strength and corrosion resistance. It is ideal for parts that operate under high-stress conditions and need a durable surface, such as crankshafts and camshafts.
- Tempering
In order to refine the grain structure and reduce internal stress, you can use processes such as quenching and tempering.
Powder metal components have pores both inside and outside. If the electroplating solution remains in these pores after plating, it could cause corrosion. Therefore, surface sealing is performed before plating. In China, Steam Treatment and Dacromet are commonly used surface finishing processes in powder metallurgy.
FAQ
Which is More Expensive in Powder Metallurgy, Dacromet Coating or Steam Treatment?
Dacromet costs more.
Steam Treatment is a basic surface finishing process commonly used on iron-based parts.
Dacromet coating is more widely applied. It offers better corrosion resistance and comes at a slightly higher price.