Zinc Plating refers to the electrodeposition of zinc metal on the surface of different components to enhance their physical and mechanical properties. The purpose of this coating is to build a barrier between substrate surface and environmental factors causing corrosion and damage such as oxygen and moisture. Zinc plating is not only reliable but also economically favorable, making it a priori choice for manufacturers.
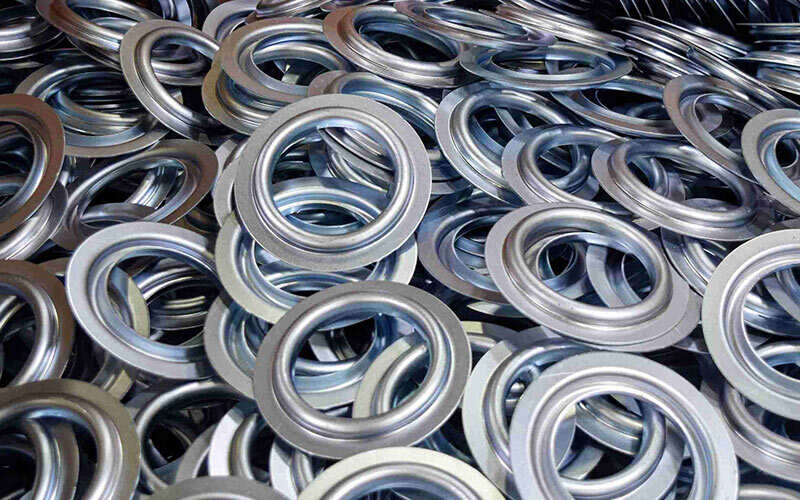
Contents
History of Zinc Plating
Electroplating of zinc started in 1827 when Dr. John W. Revere elaborated on the protective qualities of zinc coating. However, at this time, the process was slow and had many limitations, such as nonuniformity in the coating. By 1916, alkaline zinc cyanide baths were developed, significantly improving the quality and speed of plating. Modern zinc plating now uses powerful direct current (DC) systems capable of depositing large amounts of zinc quickly.
How does Zinc Plating work?
Zinc plating protects the base metal in two main ways:
Galvanic Protection
Zinc is more reactive than steel or iron. When the component is exposed to corrosive environments, zinc corrodes preferentially to the base metal. Even if the coating is scratched or damaged, the zinc effectively sacrifices itself.
Physical Barrier
The zinc layer acts as a physical shield that isolates the underlying metal from moisture, oxygen, and other corrosive elements. This shield prevents exposure of steel to the harsh environment preventing it from getting corrosion.
Zinc Plating Process
Cleaning and Surface Preparation:
This step is crucial in order to ensure the defect-free adherent zinc coating.
Alkaline cleaners: Caustic Soda or Caustic Potash.
Sandblasting: Sandblasting is done to specific SSPC surface preparation standards
Surface Activation: For a proper zinc deposition, surface activation is carried out through acid pickling. Here, the parts are often briefly dipped in an activation solution such as dilute acid HCl or H2SO4.
Zinc Deposition
Zinc deposition is carried out through an electroplating process, where substrates are immersed in a zinc-containing electrolyte bath, and an electric current is applied. At the anode, zinc gets oxidized, releasing Zn²⁺ ions into the solution:
Zn (s) → Zn²⁺ (aq) + 2e⁻
At the cathode, a reduction reaction occurs where zinc solidifies by taking electrons:
Zn²⁺ (aq) + 2e⁻ → Zn (s)
The process continues until a thin layer of zinc is produced on the substrate.
Typical plating is performed at:
- Low voltages ranging from 2-6 V
- High-purity zinc anodes
- Controlled current density of about 30.5 mA.
- pH: For Acidic baths( 4.8 and 5.5) whereas for alkaline cyanide bath(11-13)
Here, Zinc anodes are housed in baskets with anode bags to prevent contamination. Plating methods include
- Barrel plating for small bulk items, rack plating for larger or fragile parts
- Continuous strip plating for coils and wires.
Post Treatment
After the plating is done, to ensure the longevity and effectiveness of zinc plating, some post treatments are applied:
Passivation: In this step, a Chromate conversion coating is used. Chromate enhances the Zinc’s corrosion resistance.
Curing: The coating is dried in the oven or with the help of controlled hot air.
Types of Zinc Plating and Their Uses
Yellow Zinc Plating
It has a Bright yellow to iridescent gold appearance, which is the result of yellow chromate conversion coating. Such coating is done on automotive components to prevent them from coating in humid and aggressive environments.
Clear/Blue Zinc Plating
This coating is done by passivating zinc coating with a blue/clear chromate. As a result, it appears silvery. Due to its corrosion resistance properties it finds its applications in electronics, light automotive hardware, and general-purpose fasteners. It shows a lower level of corrosion protection, but is more environmentally friendly.
Black Zinc Plating
Black zinc plating typically has a matte or satin black finish due to the coating of black chromate over zinc. It shows medium to high corrosion resistance used in coating the construction hardwares and automotive parts.
Acid zinc plating
This process uses a chloride-based acidic electrolyte, typically containing zinc chloride and ammonium chloride. Acid zinc plating provides a bright, smooth finish and fast plating rates. All these combine to make it ideal for automotive parts, bolts, and decorative components. However, it offers lower throwing power, making it less suitable for complex geometries.
Alkaline Non Cyanide Zinc Plating
It uses a non-cyanide alkaline electrolyte which is composed of zinc oxide and sodium hydroxide. Such coating offers excellent throwing power and uniform plating. Though the finish is duller, it provides strong corrosion resistance and is more environmentally friendly. It finds its use in plating the Industrial parts, fasteners, and components with complex shapes.
Zinc Nickel Plating
Its coating contains 10–15% nickel with the remainder zinc. It shows superior corrosion and wear resistance; that’s why it is utilized for components that face harsh conditions and high temperatures, such as brake components and fuel systems in automotive and aerospace.
Corrosion Resistance: Superior; up to 10x greater than standard zinc.
Zinc Iron Plating
Zinc-iron plating is an alloy coating that typically contains 0.3–0.8% iron in the zinc matrix. The presence of iron increases the mechanical strength of the coating. It is commonly applied to fasteners, industrial tools, and components that benefit from black passivation finishes. It shows
good ductility and weldability.
Zinc Cobalt Plating
Zinc-Cobalt plating incorporates approximately 0.8–1.0% cobalt into the zinc layer. This addition significantly improves corrosion resistance and results in a bright. It is widely used for decorative hardware that demands a combination of surface appeal and long-term protection against rust and wear. Zinc-Cobalt plating imparts good lubricity, good ductility, weldability, anti-seize properties to the components surface. Due to its excellent protection against wear and corrosion it is used in aerospace and defense.
Zinc Plating Solution
Zinc plating baths differ in speed, safety, adhesion, and finish quality.
Zinc Plating Bath | Electrolyte Composition | Key Features |
---|---|---|
Acid Chloride Zinc | ZnCl₂ + NH₄Cl or KCl (pH ~5) | High efficiency, fast plating, good coverage, suitable for complex geometries |
Alkaline Non-Cyanide Zinc | ZnO + NaOH or KOH (pH ~12–13) | Environmentally friendly, moderate plating rate, uniform thickness |
Cyanide Zinc | NaCN or KCN + Zn(CN)₂ in NaOH/KOH (pH ~12–13) | Excellent throwing power, ductile, strong adhesion |
Boric Acid Based | Zn salt + boric acid + buffering agents (pH ~4.5–6.5) | Very smooth, even coatings, good for intricate or precision parts |
What Materials can be Zinc Plating?
Steel: It is the most frequently zinc-plated material. Zinc offers a strong barrier against rust, making steel components. Steel with zinc plating is suitable for automotive, construction, and industrial applications.
Iron: Since Iron is easily rusted if it comes in contact with moisture and oxygen, that is why it is coated with zinc to prevent it from rusting.
Factors affecting Zinc Electroplating
Ductility and Thickness
As the thickness of the coating increases, the plating becomes more ductile, such as thin Zinc Coatings (Fe/Zn 5, Fe/Zn 8) are more ductile. They perform well in applications where parts undergo bending, forming, or other mechanical stresses.
Bath Efficiencies:
A well-maintained bath ensures uniform coverage and high-quality deposits. Here are the factors that influence both efficiency:
Temperature
Affects the plating rate and the uniformity of the deposit. Higher temperatures typically increase the plating speed but may also increase the risk of poor deposit quality.
pH Level
A crucial factor in maintaining bath stability. Deviations in pH can lead to uneven plating or poor adhesion.
Concentration of Zinc
Insufficient zinc concentration can lead to poor coating efficiency and inadequate corrosion resistance.
Throwing Power and Deposit Distribution
Acid chloride baths offer high deposition rates but have lower throwing power, while alkaline baths, despite slower plating speeds, exhibit superior throwing power due to better current distribution.
Chromate Receptivity
A fine-grained, clean zinc surface allows optimal bonding and chemical interaction with trivalent or hexavalent chromates. If the zinc surface is contaminated, it can significantly reduce chromate adhesion, leading to flaking or uneven film formation.
Advantages and Disadvantages of Zinc Plating
Advantages of Zinc Plating
Excellent Corrosion Resistance
Zinc acts as a sacrificial anode, corroding in place of the base metal, which provides strong protection against rust.
Cost-Effective for Large-Scale Production
Zinc plating is relatively inexpensive compared to other protective coatings. The process requires moderate electrical power, and uses widely available raw materials, making it a cost-efficient choice.
Compatibility with Many Post-Treatments
Zinc coatings readily accept chromate conversion coatings (clear, yellow, black), sealers, and topcoats, which enhance corrosion resistance.
Good Adhesion and Appearance
Zinc coatings exhibit a uniform metallic appearance, which brighteners or post-treatments can further improve.
Disadvantage of Zinc Plating
Cyanide Toxicity and Regulatory Issues
Traditional alkaline cyanide zinc baths are highly toxic, resulting in high costs for waste treatment. .
Limited Ductility
Certain zinc bath chemistries, particularly acid chloride systems, can produce harder, less ductile deposits. This can result in microcracks or flaking if parts are subjected to forming or bending post-plating.
Less Durable Than Other Coatings
While zinc provides solid basic protection, it has lower wear and corrosion resistance compared to alloy platings like zinc-nickel or zinc-cobalt.
Risk of Hydrogen Embrittlement
During acid cleaning and electroplating, hydrogen can be absorbed into high-strength steels. This results in embrittlement and potential cracking under load. This is a critical concern for structural or safety-critical components.
Zinc Plating Vs Nickel plating
The table below compares zinc plating with nickel plating.
Attribute | Zinc Plating | Nickel Plating |
---|---|---|
Purpose | Primarily for corrosion protection; sacrificial coating | Corrosion and wear resistance; often decorative and functional |
Bath Types | Cyanide, Alkaline Non-Cyanide, Weakly Acidic Chloride | Electrolytic Nickel, Sulfamate Nickel, Electroless Nickel (Mid/High Phos) |
Substrate Compatibility | Steel, iron, and other ferrous metals | Steel, brass, copper, aluminum, die-cast zinc, etc. |
Corrosion Resistance | Sacrificial protection; zinc corrodes before substrate | Barrier protection; electroless nickel provides uniform, dense coating |
Appearance | Silvery or bluish-white; often passivated for color (blue, yellow, black) | Bright, semi-bright, matte; decorative finishes such as bright nickel-chrome |
Post-Treatments | Chromate conversion coatings, topcoats, sealers | Passivation, heat treatment (for hardness), topcoats |
Layer Thickness | Typically 5–25 microns | Electroless: 2.5–100 microns; Electrolytic: varies widely |
Wear Resistance | Poor to moderate | Moderate to excellent (especially with electroless nickel) |
Cost | Relatively low | Moderate to high (especially electroless nickel) |
Industry Usage | Automotive fasteners, hardware, general industrial components | Aerospace, automotive, electronics, chemical processing, molds, valves, medical devices |