Bearings are one of the most basic mechanical components, which reduces friction, supports mechanical shafts and carries loads. Bearing enables controlled and smooth rotational or linear motion of shafts under varying loads and speeds. A bearing typically consists of an inner ring and an outer ring, with rolling elements positioned between them. These rolling elements can be either balls or rollers. Bearings are widely used in various industries, from refrigerators and automotive gearboxes to large wind turbines.
Contents
What do Bearings Do?
- Bearings are considered key components for a stable operation by supporting either radial loads.
- Bearings prevent unwanted movement of parts of a machine by controlling their motion for specific directions, such as sliding or rotating.
- Bearings reduce heat buildup by minimizing the friction which improves the machines efficiency and makes the machine more reliable.
Types of Bearings
Ball Bearings
Ball bearings, as the name suggests these bearings use spherical rolling elements in order to minimize friction. Ball bearings can handle mainly radial loads, and depending on their type, may also support axial loads. Not only this, these bearings offer compact design with minimal maintenance that’s why they are considered cost effective. Despite all these, ball bearings have limited load-bearing capacity and can have noisy operation under certain conditions such as misalignment or insufficient lubrication.
Ball Bearing Types
Deep‑Groove Ball Bearings
Deep groove ball bearings typically feature deep, symmetrical raceways. These raceways offer excellent support for moderate loads at high speed. The deep groove bearings are known for their high-speed capability, low friction and simple design. Deep groove ball bearings are primarily designed for radial loads, but they can also support moderate axial loads in both directions. They come in two designs, such as single or double-row designs, which are available in open, sealed, or shielded configurations.
Angular‑Contact Ball Bearings
These are the types of ball bearings that usually have raceways on both the inner and outer sides of rings, which are offset to form a contact angle to the axis. As a result, they can handle combined load by supporting both axial and radial forces. These bearings offer high rotational accuracy, due to which these are considered suitable for precise shaft positioning. Angular contact bearings are usually used in pairs to carry axial loads in both directions. However, angular contact bearings must usually be used in pairs or sets to support axial loads in both directions.
Miniature Bearings
Mini ball bearings have a compact design that’s why these are used in machines where space is limited. These bearings offer low torque and support high-speed operations. Since these are usually made with stainless steel that’s why they are quite durable, but not suitable for heavy-duty applications.
Thrust Ball Bearings
Thrust ball bearings support only axial loads, which is why they are also referred to as axial bearings. These bearings consist of two raceways with a set of balls, which are arranged in a cage. This arrangement is responsible for smooth rotation under low to moderate axial forces. These bearings come in two variants including:
- Single-direction thrust bearings
- Double-direction thrust bearings
Duplex Ball Bearings
These bearings consist of two angular contact bearings, which are mounted as a match set. These bearings are used to improve load capacity and rigidity. These bearings can support multiple combinations of radial, axial and moment load depending upon their arrangement. These can be arranged in three different ways such as:
- Back-to-Back (DB)
- Face-to-Face (DF)
- Tandem (DT)
Duplex ball bearings find their application where precise alignment and stiffness are required, such as in CNC spindles and gearboxes.
Roller Bearings
Roller bearings are similar to ball bearings, but they contain cylindrical or tapered rolling elements instead of balls. Not only this, these bearings can have multiple rows of rolling elements, increasing their load-bearing capacity. Not only they can handle heavy loads, but some roller bearings, such as cylindrical and tapered, can support high-speed operations as well. Roller bearings are commonly used in heavy-duty machines such as gearboxes, construction equipment, conveyors, and railways, and also in some electric motors requiring higher load capacity.
Roller Bearing Types
Tapered Roller Bearings
These bearings come with tapered inner and outer ring raceways as well as tapered cylindrical rolling elements. They are designed in such a way that their conical surfaces converge at a common point on the bearing axis. This design allows them to support rolling motion smoothly without sliding and internal stress. Tapered roller bearings are arranged in pairs, such as back-to-back or face-to-face, to support bi-directional axial loads.
Spherical Roller Bearings 1
These roller bearings have a spherical outer raceway and a cylindrical inner raceway that accommodates two rows of rollers. This typical design allows them to handle axial and radial loads. These bearings are used where shaft misalignment or deflection is possible due to their self-aligning capability. Spherical roller bearings usually come with cylindrical or tapered bores, in sizes ranging from 20mm to 900 mm.
Cylindrical Roller Bearings
The rolling element of cylindrical roller bearings remains in contact with the raceways, offering high radial load capacity. However they can not support significant axial loads unless guiding flanges are present. Their rolling elements are slightly crowned at the ends, which helps in the reduction of stress and improving performance. Although these are considered excellent for handling radial loads, they can also support limited axial loads when it comes to flanges on both the inner and outer rings.
Needle Roller Bearings
Needle roller bearing uses long, slender rollers, which enables these bearings to support low to moderate speed operations. These are constructed in such a way that their mating shafts or housings act as raceways. This eliminates the need for separate inner or outer rings, such as in drawn cap needle rolling bearings.
Sintered Bearing
Sintered bearing is a porous bearing formed by compacting metal powders (such as bronze, iron-based alloys, or stainless steel) and sintering them at high temperatures. After vacuum oil impregnation, sintered bearings provides self-lubrication. Commonly used in motors, small fans, home appliances, and office equipment where low noise and maintenance-free operation are essential.
BLUE is an advanced sintered bearing manufacturer, supplying a wide range of standard sintered bearings, including sleeve bearings, flanged bearings, ball bearings. You can browse and compare these parts directly in our Sintered Bearing Shop. If you don’t find an exact match, we also provide custom solutions to meet your specific needs.
Plain Bearings
These bearings work on the principle of reducing friction by sliding as they do not use any sort of rolling elements. These sliding bearings fit into the housing, where they support the smooth linear or rotatory motion of the shaft. The friction between the bearing and shaft interface is reduced by incorporating a lubricating sheet or by using a self-lubricated plain bearing.
What makes the bearings remarkable is their simple design, high load support and self-lubricating properties. Plain bearings are considered ideal for oscillating or intermittent motion, whereas rolling bearings would wear quickly.
Fluid Bearings
Fluid bearings support the load by using a lubricating film, which is usually a pressurized fluid, either liquid or gas. This film separates the moving components by eliminating the direct contact between them. This reduces the friction and minimizes the wear. These bearings are known for their low friction, reliability and high stiffness. Despite all these, the fluid bearings often require a complex fluid control system.
Types of Fluid Bearings
Hydrostatic Bearings
These bearings use an external pump to supply fluid pressure regardless of shaft movement. These are considered suitable for high load capacity at low speeds.
Hydrodynamic Bearings
The hydrodynamic bearings rely on relative motion between moving surfaces to generate the fluid film. These are suitable for continuous high-speed operation but experience wear during start-up and shutdown.
Magnetic Bearings
Magnetic bearings, as the name suggests, use magnetic force to support the motion of shafts without any physical contact between the bearing and moving parts. These bearings work on the principle of electromagnetic suspension. These bearings levitate the moving shaft, usually by active magnetic forces. At the same time, the passive magnetic bearings are far less common for handling axial loads. Magnetic bearings are used where clean operation, zero lubrication, high rotational speeds, and low vibration are essential.
Active Magnetic Bearings (AMB)
These bearings use electromagnets, sensors and a control system. Here, the sensor detects the electromagnetic signal and sends it to the control system in real-time, adjusting the position of the shaft during operation.
Passive Magnetic Bearings
This magnetic bearing uses a permanent magnet to produce a static magnetic field in order to levitate shafts. This results in a more cost-effective solution but limits the load capacity.
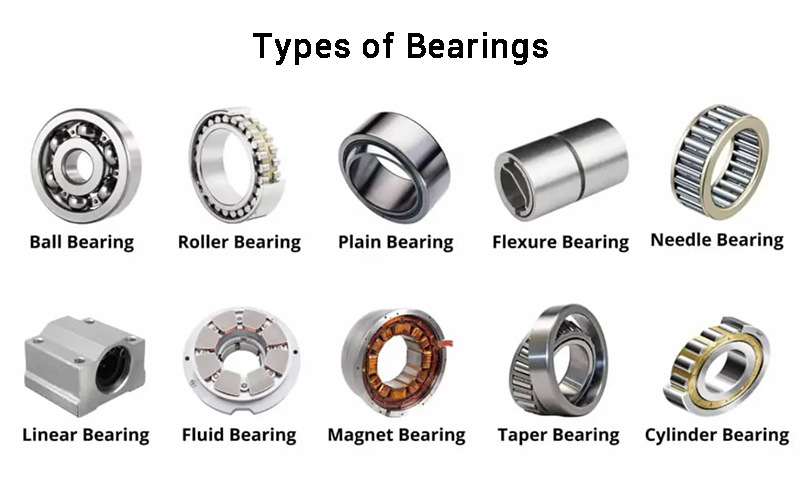
Materials Used in Bearings
High Carbon Steel
High-carbon chromium steel, offering excellent hardness and fatigue resistance, is used for most ball and roller bearings.
Stainless Steel
Due to its exceptional corrosion resistance, stainless steel is used in marine bearings.
Bronze
A self-lubricating alloy of bronze is used in plain bearings and bushings for high-load, low-speed applications.
Composites/Graphite-Based Materials
These are used in dry-running and high-temperature bearings for their self-lubricating and thermal resistance properties.
Plastic and Polymers
Plastic is also used for bearings cages to work under certain conditions. Polymers such as acetal and nylon are also utilized for manufacturing plastic bearings.
Uses of Bearings
Aerospace Industry
Bearings are widely used in the aerospace industry as ball bearings are utilized in jet engines, and tapered roller bearings are used in aircraft fuel pumps.
Automotive industry
Bearings also find their applications in the automotive industry for smoother motion, such as:
- Tapered roller bearings are used as vehicle wheel bearings.
- Plain bearings are used in internal combustion engines of vehicles.
Heavy Machinery
Due to the high load-supporting capacity, bearings are used in heavy machinery such as:
- Cylindrical roller bearings are used in crane winches and gearboxes
- Needle roller bearings are applied in hydraulic pumps and drilling machinery,
Electronics
Bearings are used in electronics where they support motion under high speed and loads, such as:
- Ball bearings are used in electric motors, fans, and conveyors.