As the population ages, the health of the elderly deserves more attention. This is inseparable from advanced medical technology and equipment.
It goes without saying that the importance of precision medical devices and biocompatible metals in the current medical industry. There are a wide range of metal injection molding medical applications, such as orthopedic implants, medical devices, and surgical tools.
Contents
Metal Injection Molding Overview
Metal injection molding is a special powder metallurgy process. You may know that MIM originated from ceramic powder injection molding. Because the technologies are similar, they are collectively referred to as PIM.
MIM has the following steps.
- Mixing
During mixing process, workers mix metal powder and binder in a powder mixer. Adding binders is to make the metal powder fully mixed more evenly.
- Injection molding
Then the metal powder is melted into liquid and injected into the mold to achieve the desired shape. Usually the weight of the injected metal no more than 100g.
- debinding
Degreasing is to remove the binder. Degreasing methods include thermal debinding, solvent debinding, and vacuum debinding.
- Sintering
MIM sintering process is similar to conventional powder metallurgy process. The finished product density is generally greater than 95%.
Medical Metal Powder Characterization
High Purity
Impurities may be detrimental to the performance and biocompatibility of metals.
Tighter Particle Size
MIM requires smaller particle sizes and tighter distribution. For stainless steel, the particle size should be less than 22μm. For titanium and titanium alloys, it should be less than 45μm.
Spherical Powder
You might already know that spherical powder has lower friction, better fluidity, and less sintering shrinkage. Generally, we produce spherical powders through gas atomization process. The picture below shows the titanium alloy spherical powder under the microscope.
MIM Metals
Here are some common mim materials.
Ferroalloy
Ferroalloy is a frequently utilized metal in medical applications for the following reasons:
- Easy to manufacture
- High ductility
- High hardness
- Non-toxic
- Biodegradable
Iron is also a blood compatible and biocompatible metal. Therefore, it can serve as a temporary cardiovascular stent to open blocked blood vessels and prevent them from narrowing.
Iron is also suitable as a material for bone tissue engineering applications because it has good mechanical properties.
However, pure iron degrades rather slowly. Alloying iron with other metals degrades iron faster and more evenly.
Titanium Alloys
Among all metals, titanium alloys offer some distinct benefits:
- Low elastic modulus
- High specific strength
- Perfect corrosion resistance
- Good biocompatibility
In the medical industry, titanium alloys are often used in dental and orthopedic implants. For example, dentists utilized Ti-6Al-7Nb bone screw implants to fix and repair broken tooth shafts.
In addition, titanium alloys are also applied in pacemakers, knee joints, fixing screws, and artificial hip joints.
However, the titanium alloy powder employed in MIM has high precision requirement (≤45μm).
Stainless Steel
Stainless steel, such as 420, 316L, and 440C, is a common metal for medical devices due to:
- High strength
- Good wear resistance
- Good biocompatibility
- Better manufacturability
MIM can make 316L stainless steel products with a density higher than 98%. This can provide products with excellent mechanical properties for medical applications.
Magnesium Alloy
Magnesium is another biodegradable metal. It has these features:
- Lightweight
- Excellent biocompatibility
- Biodegradable properties.
It can be employed in cardiovascular stents, which have proven to perform well without inflammation or thrombosis.
When Magnesium utilized in cardiovascular stents, it has shown to perform effectively without causing inflammation or thrombosis.
Magnesium has mechanical properties comparable to human bones and is lighter in weight. So it is also suitable for temporary bone tissue or orthopedic devices, including orthopedic screws.
Shape Memory Biomedical Alloys
Shape memory biomedical alloys have a wide range of biomedical applications, for instance:
- Dentistry
- Treat fractures
- Cardiovascular self-expanding stents
Metal Injection Molding Medical Applications
Medical Device
MIM has the capability to manufacture small and complicated components for some medical devices, like:
- Knee rehabilitation device
- Laser surgery machine
- Arthroscopic surgery device
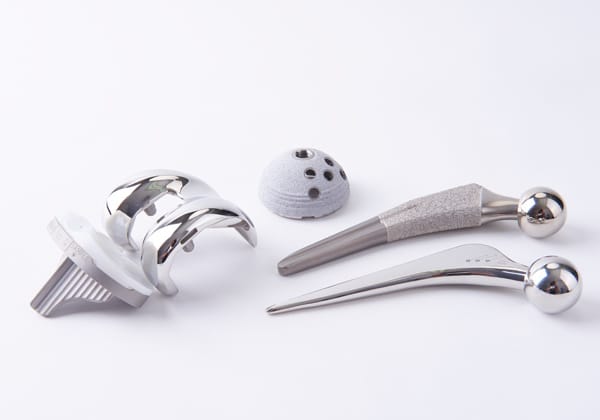
Metallic Orthodontic Brackets
MIM orthodontic brackets have high strength, good biocompatibility and precise fit. Orthodontic brackets are usually made of 316L stainless steel.
Besides, MIM could manufacture screw dental implants, ultrasonic endodontic, and scaler tips in dental treatment. This is so beneficial for orthodontic results.
Surgical Fixation Devices
The articulation gears for surgical fixation devices made through the MIM process perform exceptionally well. They are crafted from 17-4PH stainless steel, featuring a density greater than 7.65 g/cm³, an ultimate tensile strength of 900 MPa, and a hardness of 25 HRC.
Surgical Tools
Traditional surgical instruments, such as surgical knife handles, forceps, pliers, are mostly made by forging and precision machining. MIM provides a better and more economical way to manufacture these instruments. Surgical stapler jaws are a typical case.
Vascular Stents
MIM can manufacture stents for the treatment of cardiovascular diseases. These stents have complex structures and are made through braiding or laser cutting techniques, which is very expensive to manufacture. MIM could produce these stents in an affordable way without sacrificing product performance.
According to the report of the Transactions of Nonferrous Metals Society of China, researchers successfully implanted MIM 316L stainless steel stents into animal arteries. This proves the feasibility of clinical use of MIM vascular stents.
Hearing Aids
The picture below shows a highly complex hearing aid component. Its function is to enhance sound frequencies and improve hearing. It is made of 316 stainless steel through the MIM process. Compared to other methods, it can save about 20% in cost.
Metal injection molding also has the following applications in the medical industry:
- Scissors and sewing units
- Drug delivery devices,
- Surgical clamps
- Knife shaft tools
- Oxygen concentrators
Advantages of MIM in Medical Field
- High sintering density
Since MIM uses very fine metal powder, the sintered density of MIM products can easily exceed 98%.
- Improve biocompatible
The medical industry has a great demand for biocompatible materials that are harmless to the human body. Metal injection molding has a wide range of material options to manufacture metal injection molding parts.
- High product design freedom
Metal injection molding parts in very small sizes (typically up to 60 mm) that are often difficult to manufacture using other processes. This provides medical professionals with more design freedom to create more compact and efficient parts.
- Extremely high part precision
Traditional metal manufacturing processes, like machining and casting, are limited to achieve tight tolerances. Metal injection molding makes it possible to make complex, small, high-precision products.
We provide precision metal injection molding services tailored to the medical industry’s strict performance and biocompatibility requirements. We deliver high-density MIM parts with tight tolerances and smooth surface finishes using materials such as stainless steel and titanium.