MIM Parts Supplier - BLUE
With over 10 years of experience in designing and manufacturing MIM parts, BLUE delivers high-quality products to customers in Europe and the United States. Our metal injection molding parts serve diverse industries, including automotive, power tools, medical, and electronics.
Why Choose BLUE?
BLUE delivers high-quality metal injection products, supported by advanced production machines, strict quality control, and free mold design—your trusted choice!
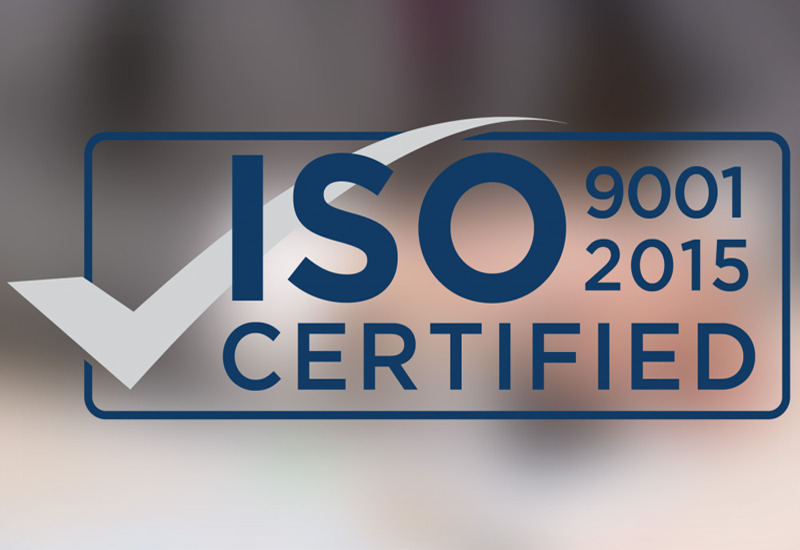
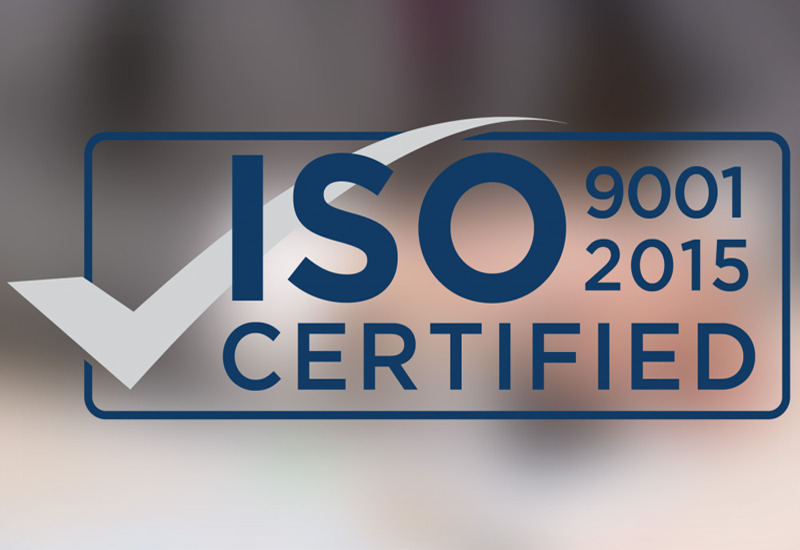
BLUE High Quality Standards
BLUE assures your product quality with ISO 9001:2015 certified quality management system. We provide a one-year warranty on your metal injection molding products.
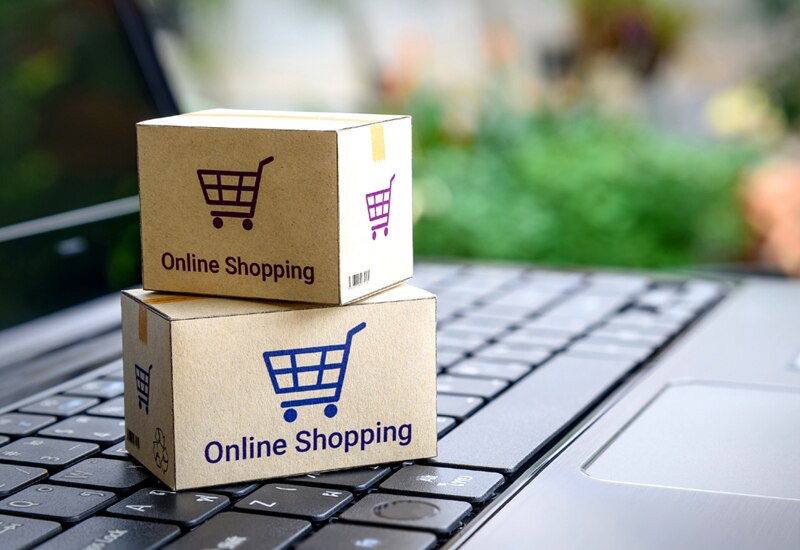
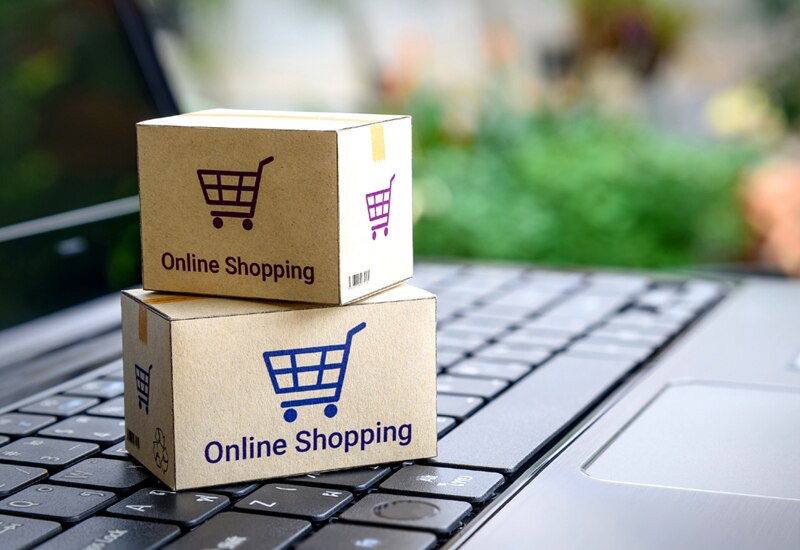
Free Mold Design
With over 20 years of expertise in mold design, BLUE offers free, high-precision mold design services to meet your customized needs. Let our experience work for you!
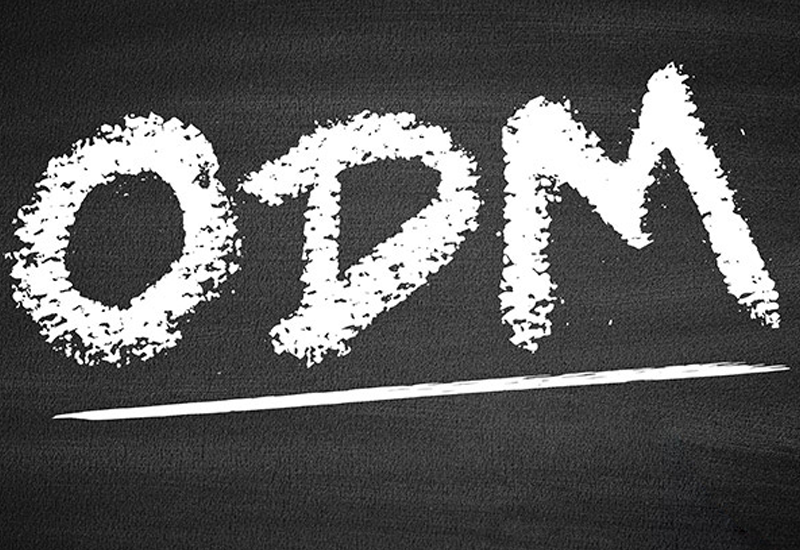
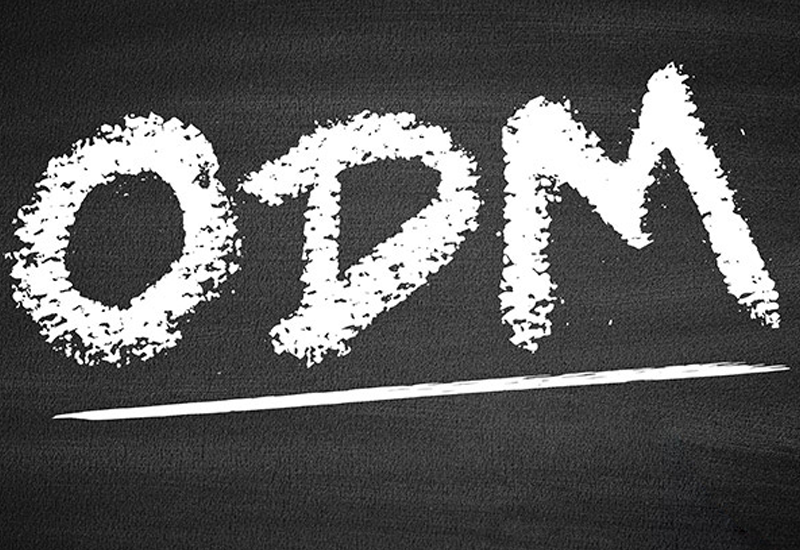
OEM/ODM Services
Using advanced equipment, we provides free mold design based on your drawing and offers assistance with your cotomized product processing.
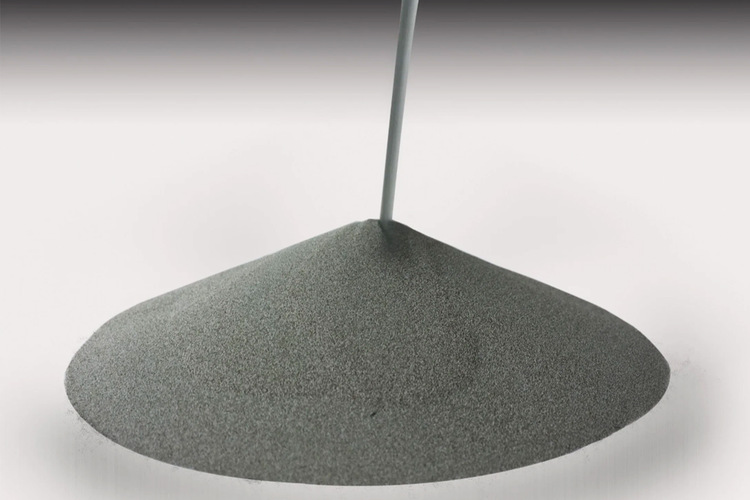
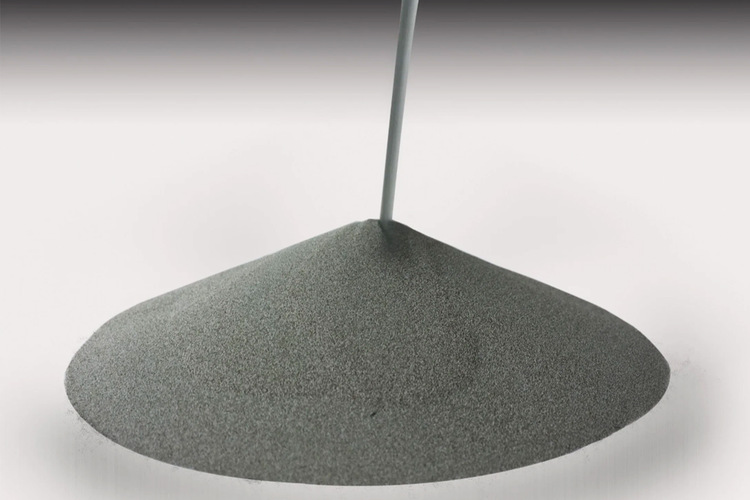
Metal Injection Molding Materials
As a leading metal injection molding suppliers, BLUE has the ability to manufacture your precision component using the following materials:
- Stainless steel: 316L, 304, 420, 440C, 17-4 PH
- Tool steel: M2, T15, S7
- Aluminum alloy: 6061 aluminum alloy
- Titanium alloy: Ti-6Al-4V, Ti-6Al-7Nb
- Nickel Alloys: Inconel 625, Inconel 718
- Tungsten alloys: tungsten-copper, tungsten heavy alloys
- Hard materials: cobalt-chromium, WC-Co, Fe-TiC
BLUE's MIM’ Manufacturing Capabilities
- Parts Mass: BLUE is capable of producing MIM parts weighing from 0.2 to 100g.
- Size: Part diameters of 1 to 30mm are available.
- Wall Thickness: In most cases, we can manufacture parts with a minimum wall thickness of 0.5mm, while some products can reach a wall thickness of 0.25mm. Avoid components over 12.5 mm thick.
- Tolerance: For most metal injection molded parts, we can control the tolerance within ±0.5%, and for particularly small products, we can achieve ±0.2%.
- Density: The density of most MIM parts can be achieved 98%.
- Surface Finish: Typically, the surface roughness of our manufactured MIM parts can reach 1 μm Ra, and 0.3 to 0.5 μm Ra is also possible.


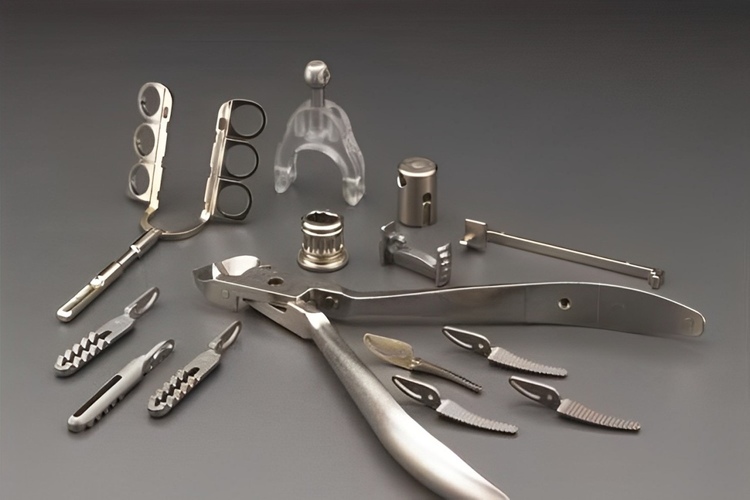
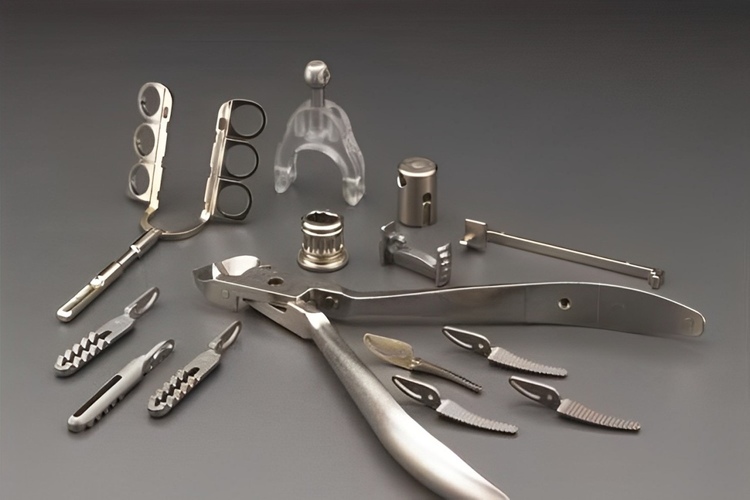
BLUE MIM Parts Applications
The metal injection molding products we produce have served a variety of industries, including:
- Automotive Industry: gearbox parts, seat adjustment brackets, engine components, and car door lock parts.
- Medical Industry: scalpel components, medical equipment parts, medical implants, and surgical tools.
- Electronics: mobile phone camera frames, lens brackets, charging slots, home appliance components, and laptop hinges.
- Tools: power tool nuts, reciprocating saw parts, and electric hammer components.
Benefits of MIM
- Metal injection molded parts can be shaped in one step, eliminating secondary processing costs.
- MIM parts have a fine surface finish, making them ideal for products with high aesthetic requirements, such as watches and mobile phones.
- Metal injection molded products have a higher density than conventional powder metallurgy parts.
- MIM is suitable for mass production and for manufacturing complex parts with intricate features.
- MIM achieves a material utilization rate of over 95%, saving resources and costs.
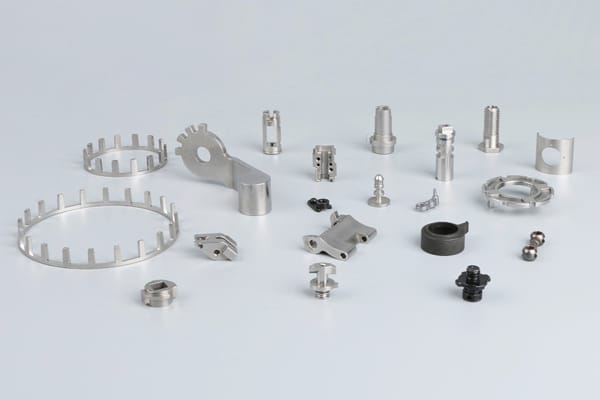
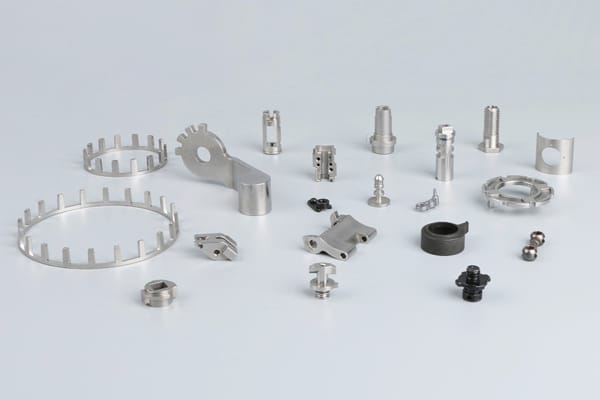
Metal Injection Molding Parts Gallery
Below are some of the metal injection molded parts BLUE has produced.


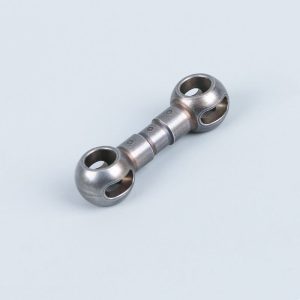
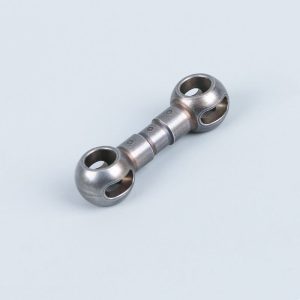
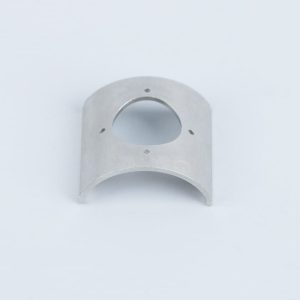
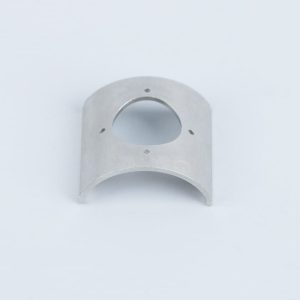
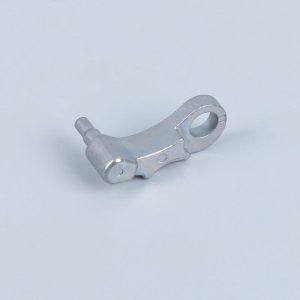
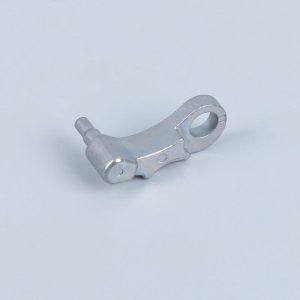


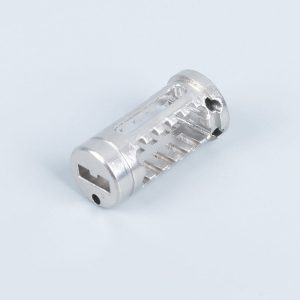
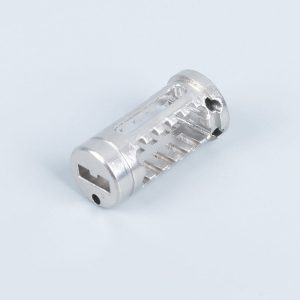
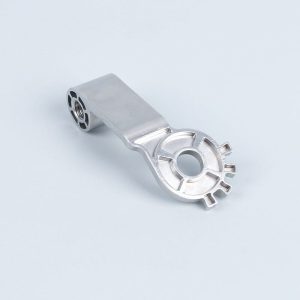
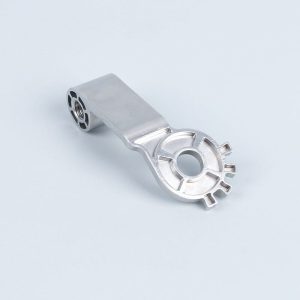
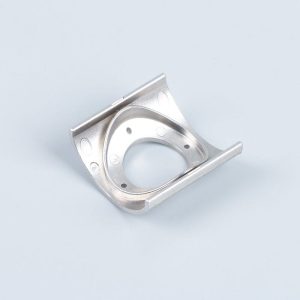
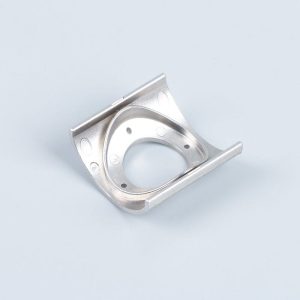
MIM Parts Manufacturing Process
Metal Injection Molding (MIM) process consists of multiple and complex steps. Fortunately, BLUE has over 10 years of experience in designing and manufacturing MIM parts. Our products are widely used in the automotive, power tools, medical, and electronics industries, delivering exceptional quality and precision for your needs.
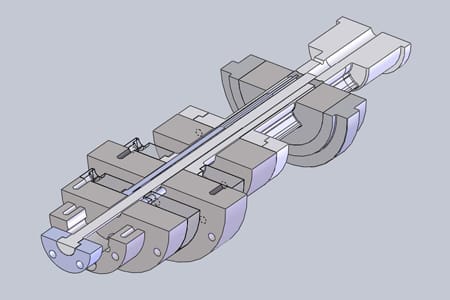
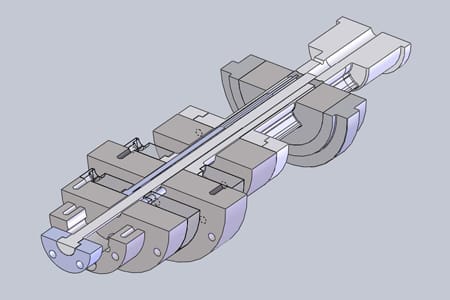
Designing
MIM parts design needs to consider numerous factors such as material selection, part geometry, wall thickness, sintering shrinkage, etc.
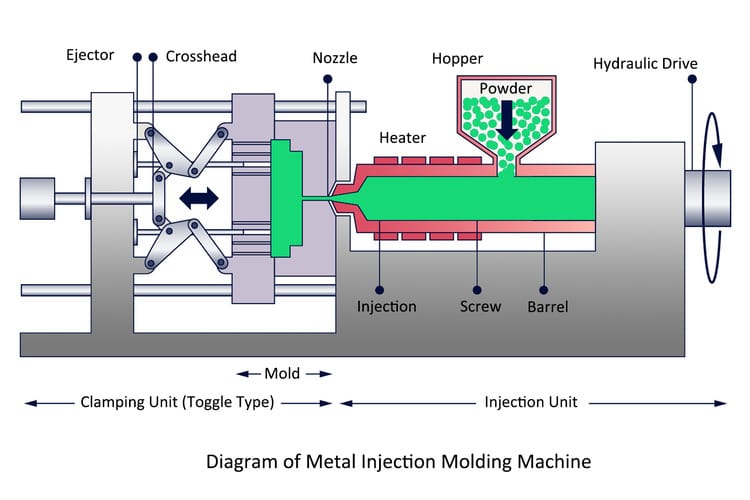
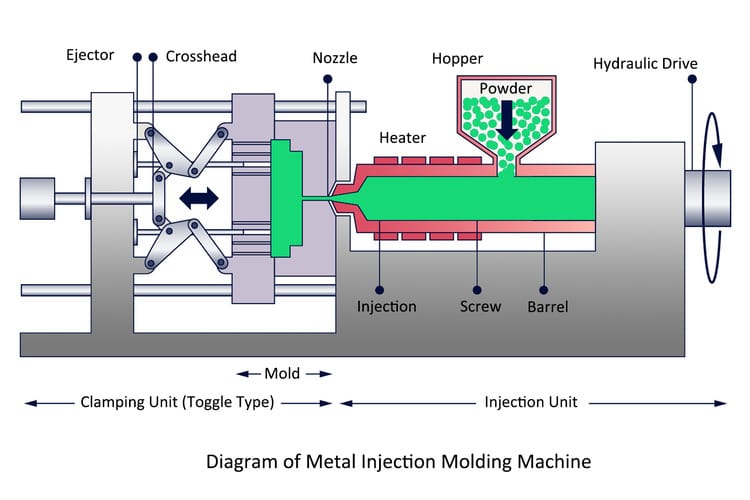
Tooling
The feedstocks enter the hopper, pass through the feed barrel, and are injected into the mold by the injection molding machine to form green parts.
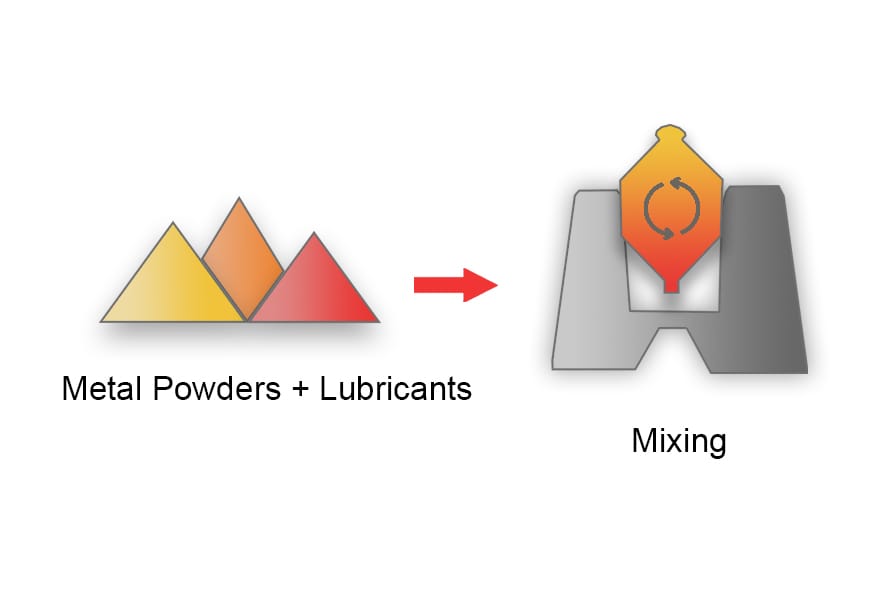
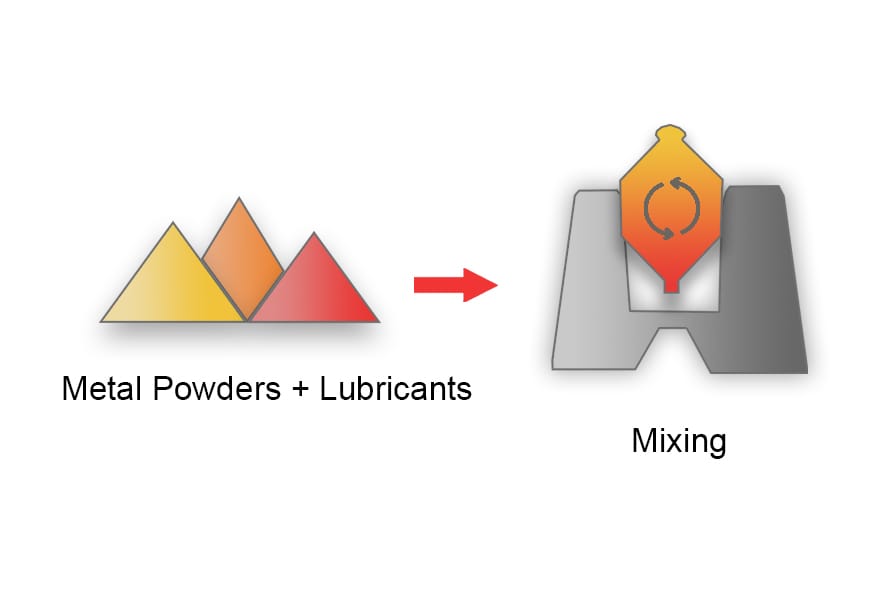
Mixing
Metal powder and binder are mixed in a ratio of 60:40 to form the raw material, called "feedstock". Binder makes metal powder have better fluidity and adhesion.
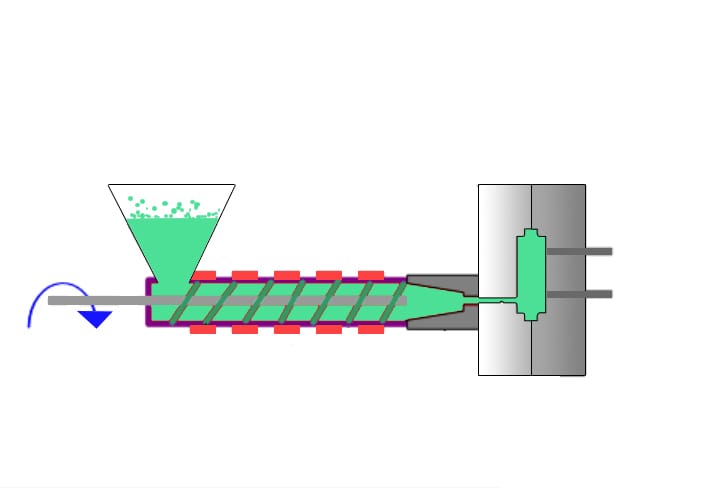
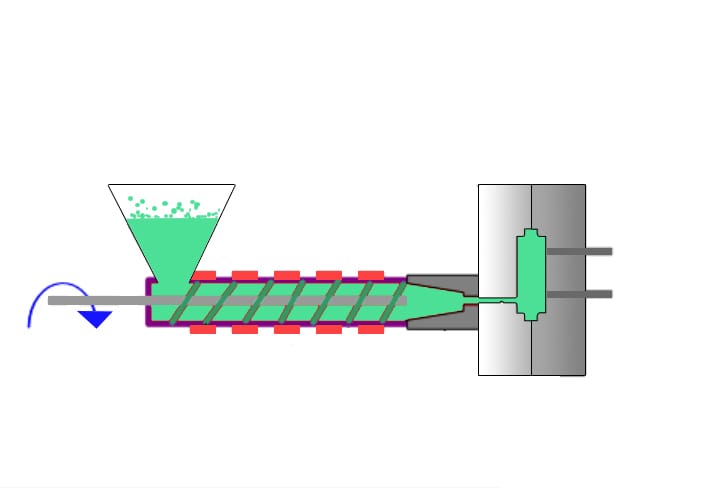
Injecting
The feedstocks enter the hopper, pass through the feed barrel, and are injected into the mold by the injection molding machine to form green parts.
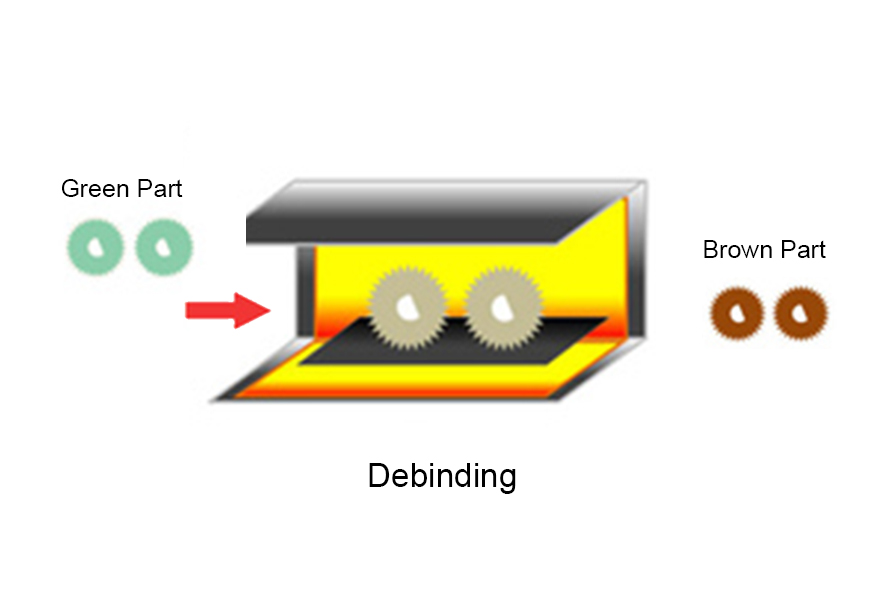
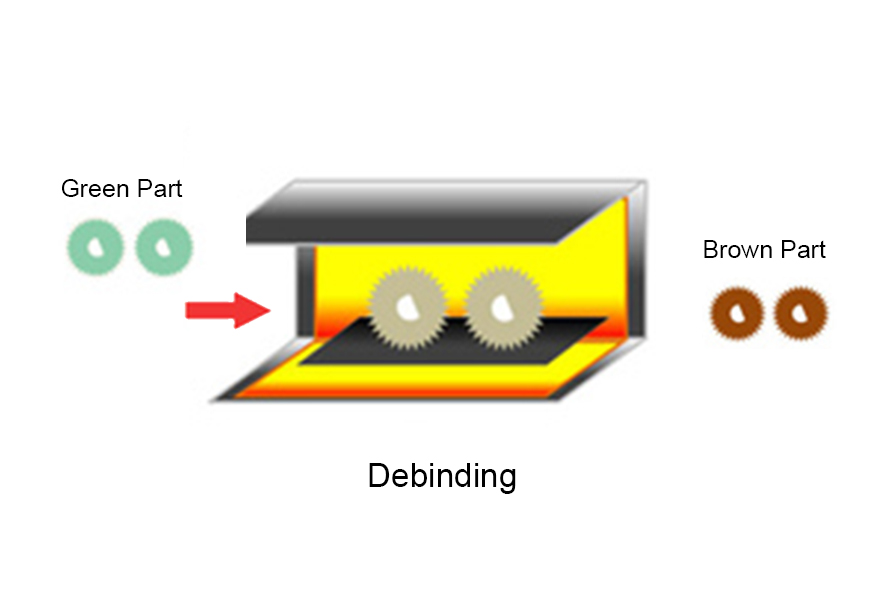
Debinding
Debinding is to remove the binder in the green parts. Debinding processes include thermal debinding, solvent debinding, catalytic debinding, etc.
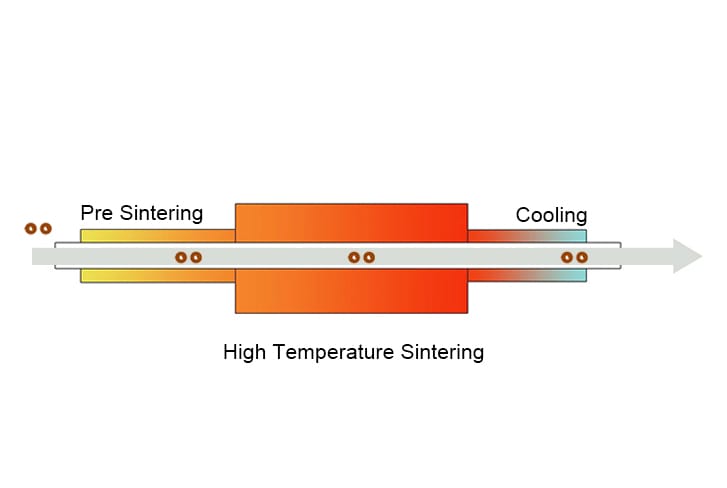
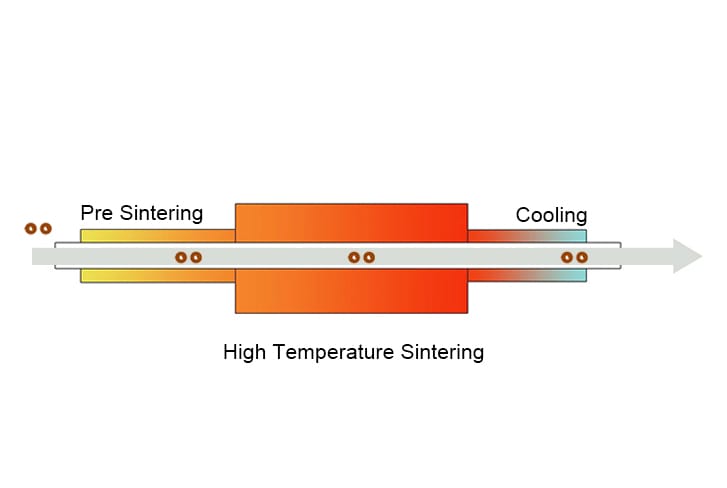
Sintering
Sintering heats the components to a temperature below its melting point in a controlled atmosphere to obtain the desired mechanical properties.
BLUE's Other Manufacturing Capabilities
BLUE covers the full range of powder metallurgy processes, providing one-stop customization for powder metallurgy parts, MIM parts, sintered filters, and sintered ceramic components with strict quality control.
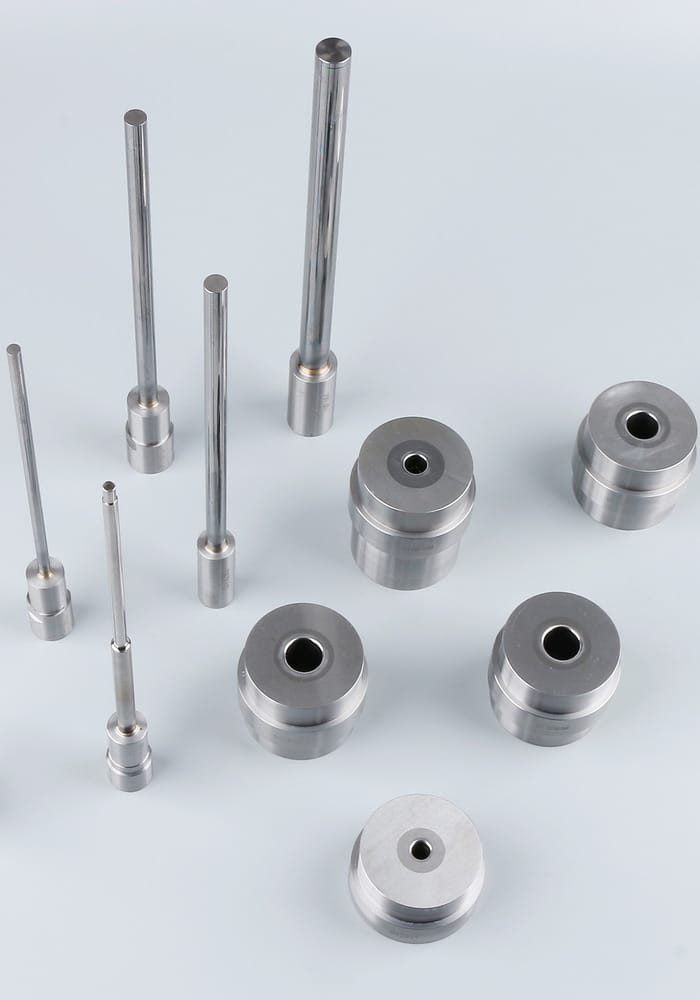
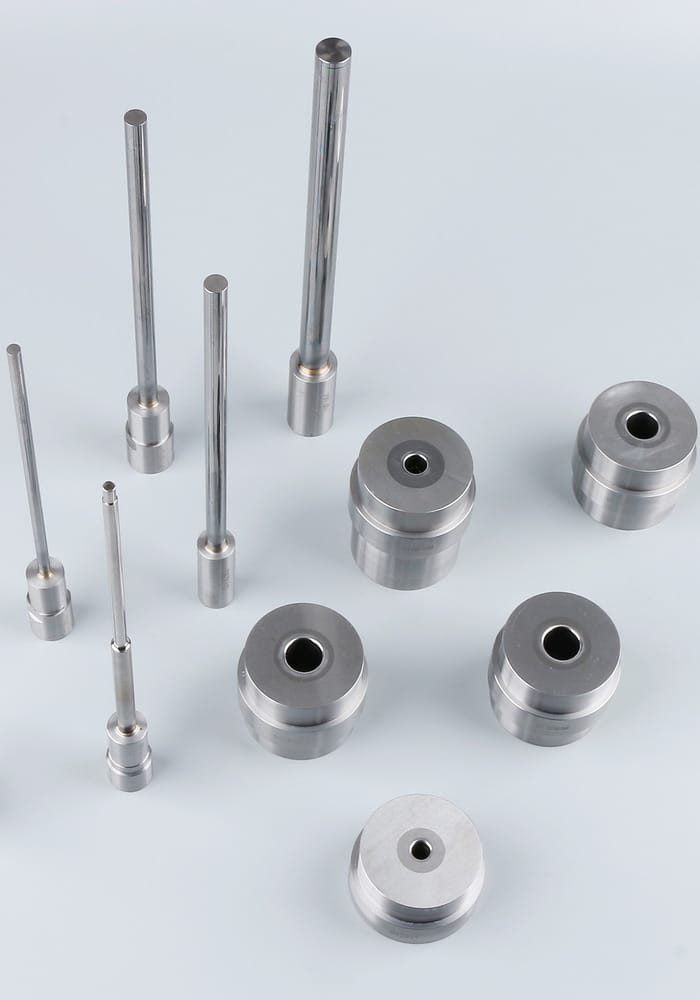
PM Tooling
BLUE has over 20 years of experience in powder metallurgy tooling design and production, with a service life of up to 500,000 cycles.
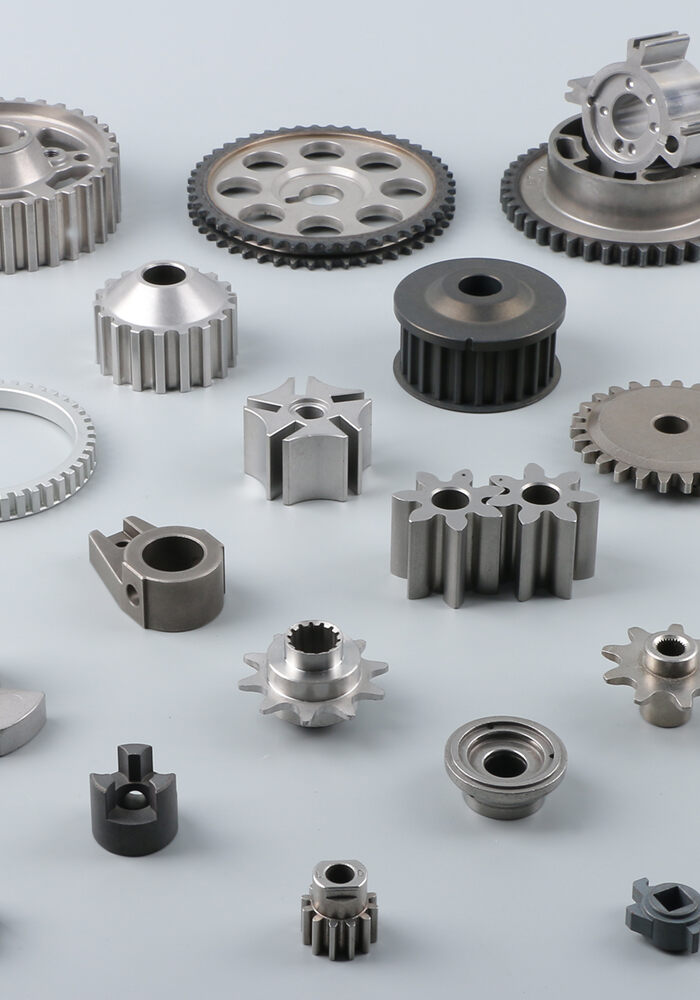
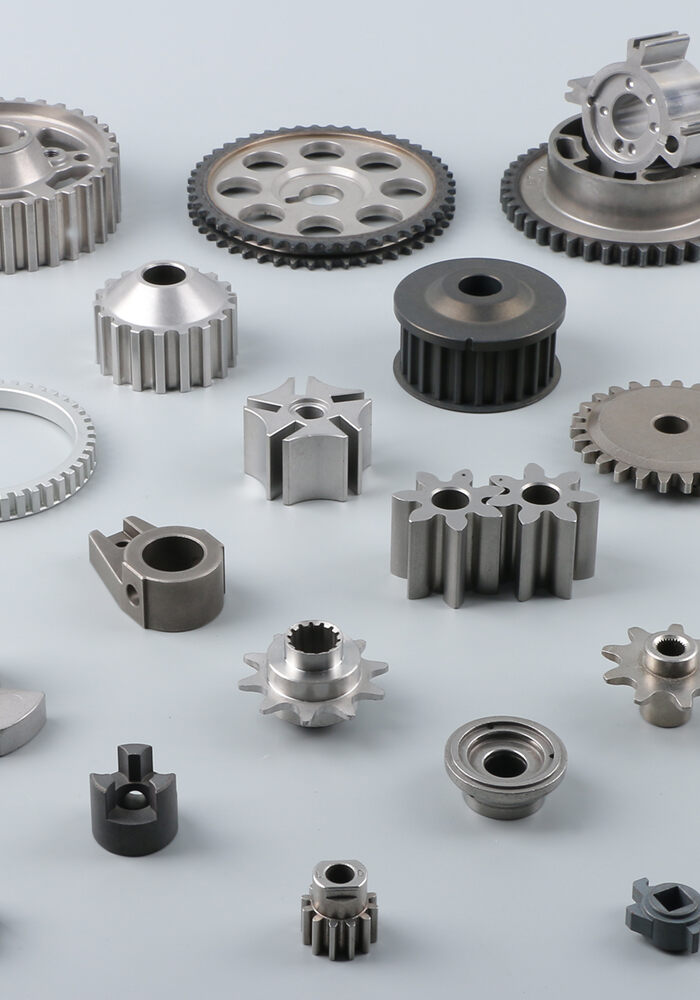
PM Parts
BLUE offers high-precision, strong powder metallurgy parts, customized to meet strict quality standards for various applications.
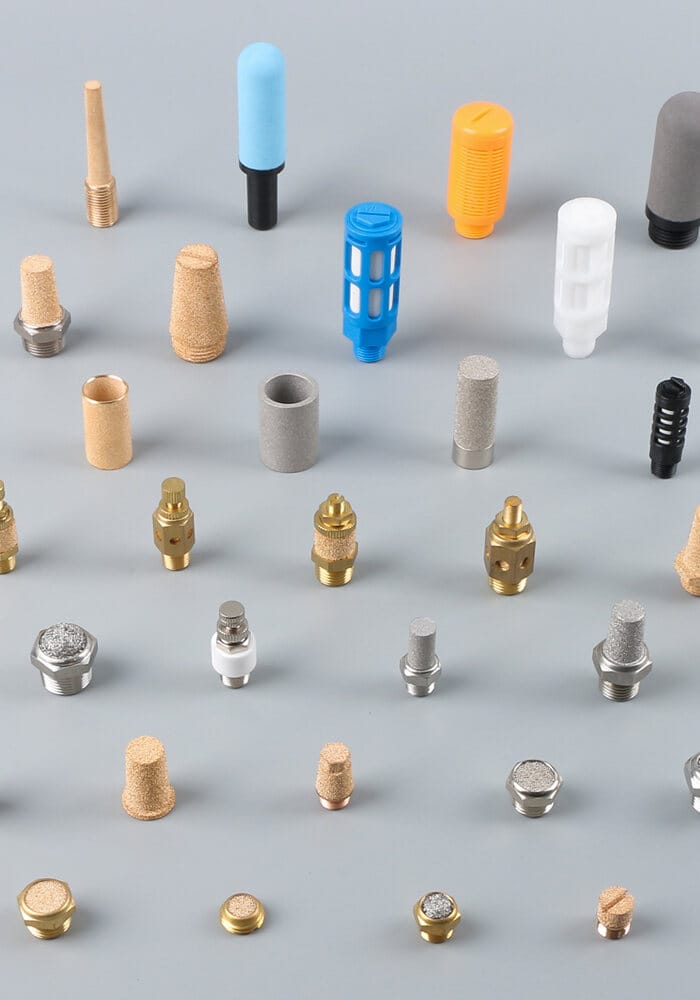
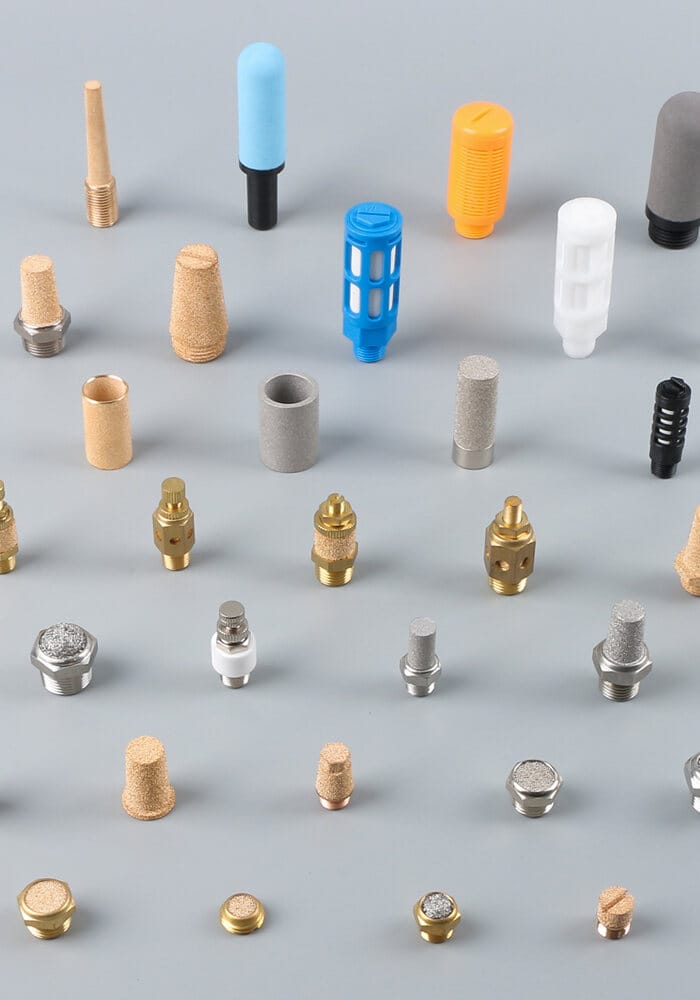
Sintered Filters
BLUE's sintered filters are designed to resist corrosion, so it can perform reliably and durable even in harsh chemical environments.
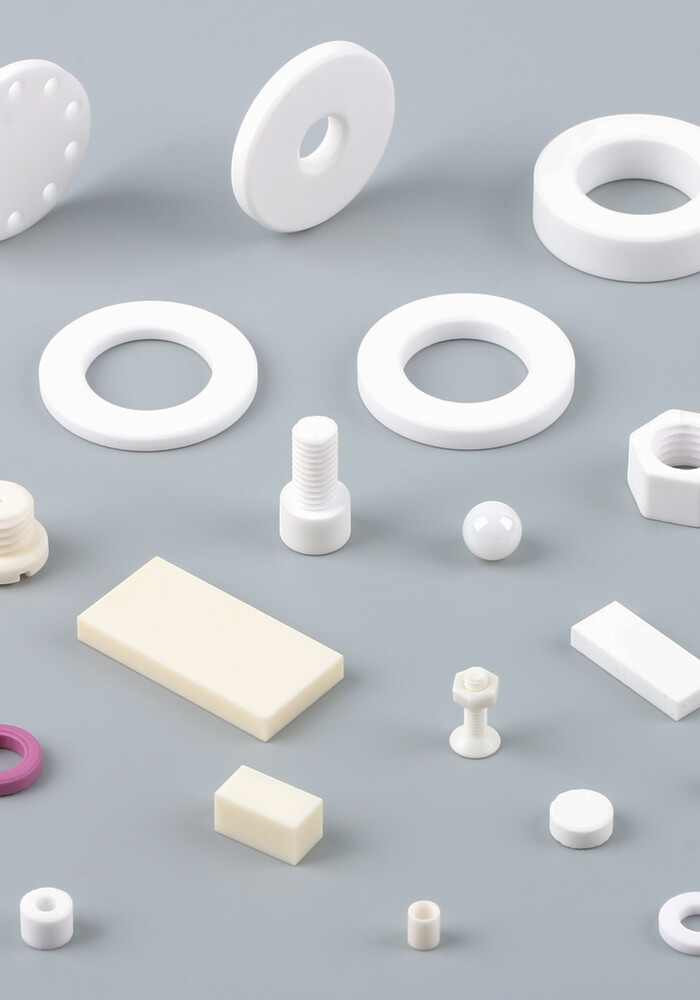
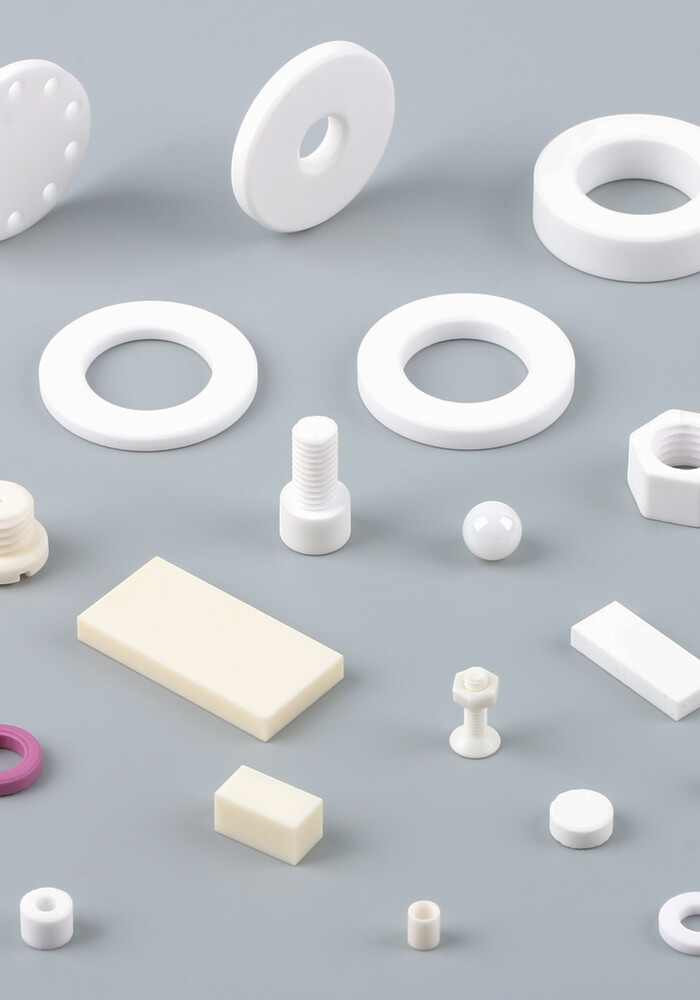
Sintered Ceramics
BLUE's sintered ceramics offer excellent resistance to high temperatures and corrosion, along with good strength, hardness, and surface finish.
FAQ's
Here are some of the questions we get asked often. If yours isn’t answered, don’t hesitate to contact us, we’re happy to help!
Metal injection molding covers multiple processes, such as mixing, injection, degreasing, sintering, secondary processing, etc., and it takes about 20-30 days
MIM parts utilize fine metal powder and high-cost molds, making the initial investment substantial. Additionally, the required equipment includes injection molding machines, degreasing units, sintering furnaces, and secondary processing machines. Consequently, MIM offers a price advantage primarily in mass production scenarios.
MIM parts utilize fine metal powder and high-cost molds, making the initial investment substantial.
We use secondary operations to improve the mechanical properties, dimensional accuracy and surface appearance of sintered MIM parts, including machining, heat treatment, embossing, machining, surface treatment and hot isostatic pressing.
- Avoid using components thicker than 12.5 mm or thinner than 0.5 mm.
- Avoid components weighing more than 100 grams.
- Avoid long pieces without a draft angle of at least 2° to allow for ejection.
- Avoid holes with a diameter less than 0.1 mm.
- Avoid uneven wall thicknesses.
- Avoid sharp corners; use radii greater than 0.05 mm.
- Avoid internal closed cavities.
- Avoid internal undercuts.