Gears come in many shapes and designs, each suited for specific functions. By understanding the types of gears, you can choose the best solution for transferring motion and power in your projects. Here’s a clear look at the main gear types and what makes each one unique.
Contents
What are Gears?
Gears are the basic mechanical component used to transmit rotation and torque from a driving shaft to a driven shaft and to change the speed ratio between them. Gears come in various sizes and tooth alignment depending on the required applications. The teeth carved on these gears possess uniform spacing, allowing them to work smoothly under certain loads, preventing them from slipping.
How Do Gears Work?
Gears work by combining with shafts to transfer motion and torque. The gear teeth mesh with each other. When one gear rotates, it drives the connected gear by pushing its teeth, causing the second gear to rotate. This rotation is responsible for transferring speed, torque, and power depending upon the tooth count and pitch diameter.
Types of Gears
Different types of gears are produced through diverse gear manufacturing process, each chosen based on application needs and mechanical requirements.
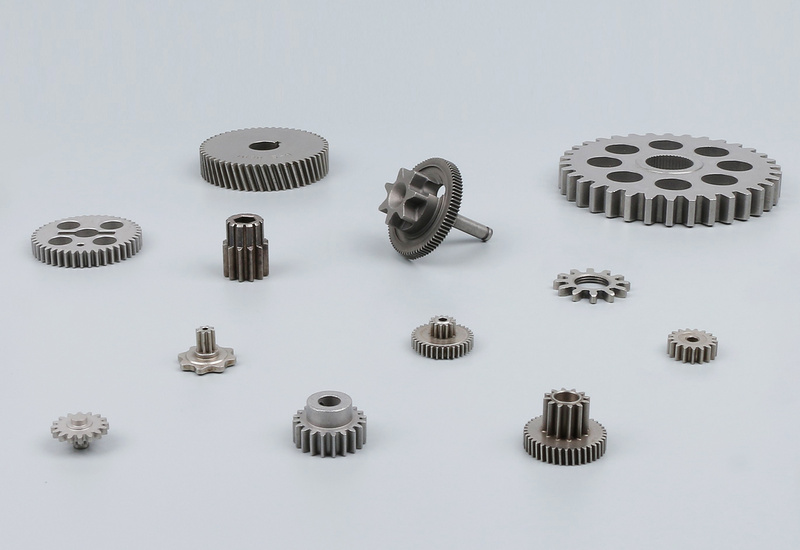
Spur Gear
Helical Gears
Helical gears are cylindrical gears with their teeth cut at a helix angle, forming a spiral shape around the gear body. These gears are used for transferring power and motion between parallel shafts. Their angled tooth design makes them different from the spur gears with straight teeth.
Why Helical Gears are Used
Smooth Power Transmission
The angled teeth of helical gears allow gradual engagement, resulting in a quieter operation with low noise and vibration.
High Load Capacity
Due to multiple teeth in contact at any time, these gears distribute load more evenly and handle greater torque than spur gears.
Efficient Operation
Since these gears offer better contact and rolling action that’s why they show high efficiency and low energy losses.
Durability
Helical gears have reduced backlash and lower impact forces, which increase gear life and system reliability.
Versatility
These gears can be used in a variety of applications requiring high speed, high torque, or quiet operation.
Types of Helical Gears
Single helical gears: Single helical gears have teeth cut in a single helix direction that can be either right-hand or left-hand. These are usually at angles between 15° and 45°.
Double helical gears: Double helical gears consist of two sets of helical teeth placed side-by-side with opposing helix angles, separated by a groove. They offer more smoother and stable operation compared to single helix gears. The design of these gears allows better tooth overlap, which enhances power transmission and reduces wear.
Bevel Gears
Bevel gears are also used for transferring torque and motion between intersecting shafts, which are commonly arranged at 90 degrees. These gears have a conical shape, due to which it’s easier to change the direction of motion while adjusting torque and speed. Bevel gears are typically used in systems that require compact and angled transmission setups.
What Makes Bevel Gears Stand Out?
- Torque and speed control: The increase in torque and speed can easily be controlled in bevel gears by adjusting the gear ratio and tooth count.
- Directional change: These are ideal for systems where shaft orientation needs to shift, usually at right angles.
- High efficiency: Bevel gears are highly efficient, and most of their types, such as straight, spiral, or Zerol bevel, can achieve 97-99.5% efficiency when properly aligned and lubricated.
- Load handling: These gears are capable of transmitting both radial and thrust loads.
Types of Bevel Gears
Straight bevel gears: Straight bevel gears have straight teeth that taper toward the apex of the cone. They are simple in design and cost-effective to manufacture. But these bevel gears generate higher noise and vibration due to sudden tooth contact.
Spiral bevel gears: Spiral bevel gears feature curved teeth that allow gradual engagement and higher tooth contact ratios. This results in smoother, quieter operation and greater load capacity
Zerol bevel gears: Zerol bevel gears combine features of both straight and spiral types, with curved teeth and a 0° spiral angle. Zerol gears are easier to align and often interchangeable with straight bevels without major design changes.
Planetary Gears
Planetary gears, which are also known as epicyclic gears, consist of a set of gears. These gears include a central gear, which is also known as the sun gear, and acts as a driving gear. This driver gear is further surrounded by driven gears, which act like planets around the sun gear within a ring gear.
Characteristics of Planetary Gears
- These gears show high torque density, which means they can transfer a large amount of load within a compact design.
- These gears show high performance due to their coaxial and symmetrical design.
- Planetary gears are considered highly durable due to their ability to efficiently distribute load among multiple planet gears.
- In a planetary gear set, you can tailor torque and speed by fixing or driving different members (the sun, ring, or carrier) or by selecting gears with alternate tooth counts.
- These gears offer smooth and efficient power delivery due to constant meshing and balanced transmission.
Types of Planetary Gears
Single-stage planetary gear set: This is the basic planetary gear, which offers high torque density and compactness. It is considered ideal for machinery where space and efficiency are required.
Multi-stage planetary gear set: This is the type of planetary gear which utilizes multiple planetary stages in series to increase torque and achieve higher gear ratios.
In-line planetary gear set: It is a planetary gear that features coaxial input and output shafts for direct alignment.
Hypoid Gears
Hypoid gears are just like the spiral bevel gears, which are responsible for transmitting motion between non-intersecting, offset shafts. These gears consist of:
- Hypoid Pinion: This is the smaller gear with a larger spiral angle. It engages the crown gear with offset alignment.
- Hypoid Gear: Larger gear in a hypoid pair that meshes with the hypoid pinion; sometimes called the ring gear in automotive axles.
- Bearing arrangement: The hypoid pinion is mounted between two tapered-roller bearings, which minimise shaft deflection and raise mesh stiffness; the ring gear is carried on its own hub bearings inside the axle housing.
Characteristics of Hypoid Gears
- The offset geometry of these gears allows for the support of both pinion and gear shafts on both ends. As a result, such gears show high rigidity and durability.
- Hypoid gears provide higher speed reduction than traditional bevel gears
- The smoother meshing of gear teeth results in a quieter operation.
- These gears also offer greater load-carrying capacity with larger tooth contact areas.
Internal Gears
Internal gears are a unique type of gear with teeth cuts inside the diameter of a cylindrical surface instead of external teeth. These gears are considered ideal for high-torque transmission in limited space, such as in planetary gearboxes. Whenever it works combined with external gears, they mesh and rotate in the same direction.
These gears offer:
- Smooth power transmission
- Allow for larger profile shifts than external gears
- High gear ratios in a smaller package
Face Gears
Face gears, which are also termed as crown gears, are the gears in which teeth project radially from the face. Due to this unique geometry, these gears can easily mesh with spur and helical pinions, mostly at a 90-degree shaft angle. The complex tooth shape of these gears often requires CNC machining and cutters like skiving or shaping tools for accurate profiles.
Why Choose Face Gears
Consistent Motion Transfer
These gears ensure uniform contact stress, which is helpful in the reduction of vibration and operational noise.
Enhanced Load Handling
Crown gears offer high load handling capacity due to the broad tooth engagement surface. As a result, they are used in heavy-duty applications like those in aerospace.
Reduced Bearing Strain
Since these gears generate minimal axial force, which lowers the load on supporting components, resulting in a higher reliability.
Space-Efficient Geometry
These gears are usually optimized for compact assemblies while enabling high gear ratios.
What Materials are Used in Gears?
Carbon steel
Carbon steel and its alloys are preferred for strong and durable gears, especially in high-load applications.
Cast Iron
Cast iron is also used for manufacturing gears due to its exceptional machinability and high compressive strength.
Bronze
Bronze is commonly chosen for worm gears because of its smooth, low-friction performance.
Nylon and Polymers
Nylon and polymers are considered best for lightweight gears, which are used in low-stress environments.
Applications of Different Gears
Automotive
In the automotive industry, gears are widely used depending upon the requirements, such as:
- Hypoid bevel gears are extensively used in rear axle differentials of cars and trucks because of their higher torque transmission and quieter operation.
- Spiral bevel gears are also used in automotive axles and high-performance drivetrains.
- Planetary gearboxes are used in automatic transmissions, DC motors, and servo motors.
Aerospace
- Helical gears are used in helicopter main and tail rotor gearboxes, where compact size, high load capacity, and smooth transmission are essential.
- Spiral bevel gears are utilized in aircraft transmissions and aircraft mechanical systems. These systems require precise motion control, low vibration, and high reliability.
Industrial machinery
- Straight bevel gears are used in industrial gearboxes and equipment with moderate speeds and static loads.
- Spiral and hypoid bevel gears find their application in heavy-duty machinery drives and precision gear reducers.
- Planetary gears are used in industrial pumping systems for their quiet operation, high durability, and efficiency.
Robotics and Automation
Gears are also widely used in robotic systems such as:
- Planetary gears are used in servo-driven robotic systems due to their compact size, high torque output, and rigid structure.
- Face gears are used in robotic joints for precise motion.