Excellent Quality Sintered Ceramics
BLUE has the capability to handle the entire production process of sintered ceramics, including forming, sintering, precision machining, and testing, and can customize production according to your requirements.
Why Choose BLUE?
BLUE offers outstanding sintered ceramics, utilizing advanced production machines, stringent quality control, and comprehensive inspections—your trusted choice.
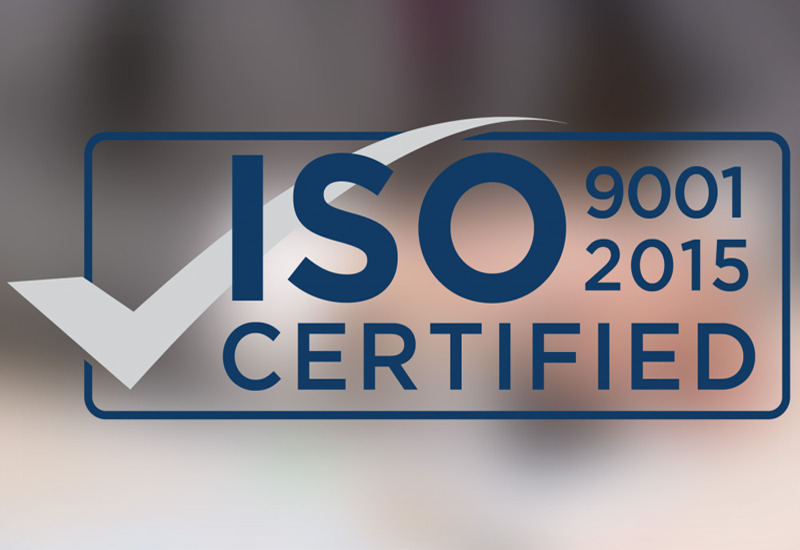
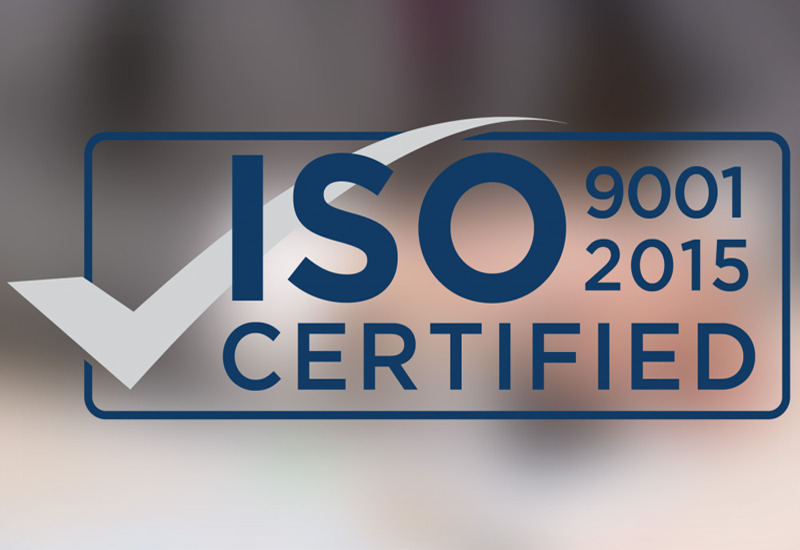
BLUE High Quality Standards
BLUE assures your product quality with ISO 9001:2015 certified quality management system. We provide a one-year warranty on your sintered ceramics.
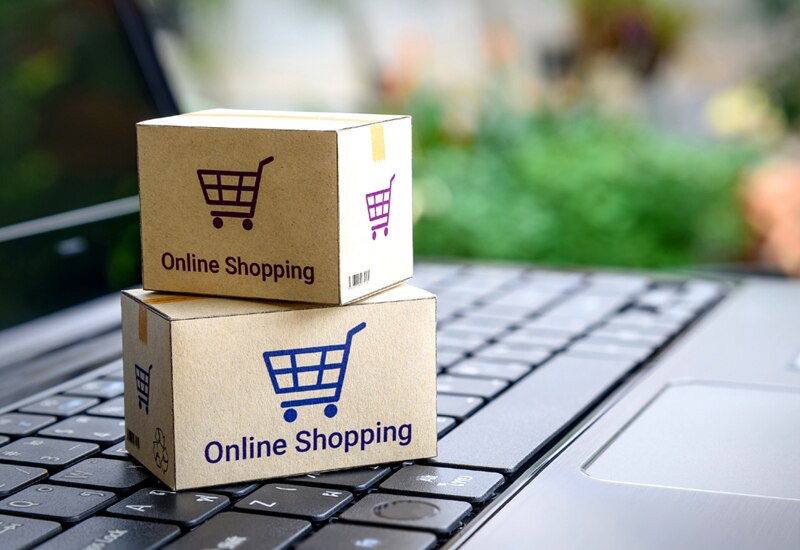
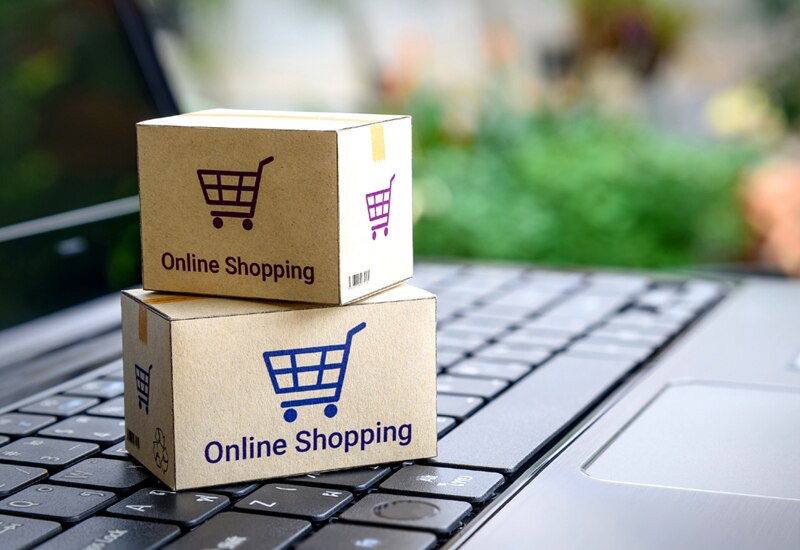
Standard Sintered Ceramics Shop
BLUE has a wide range of standard sintered ceramic in stock for quick delivery. Visit our stand parts shop to pick what you need.
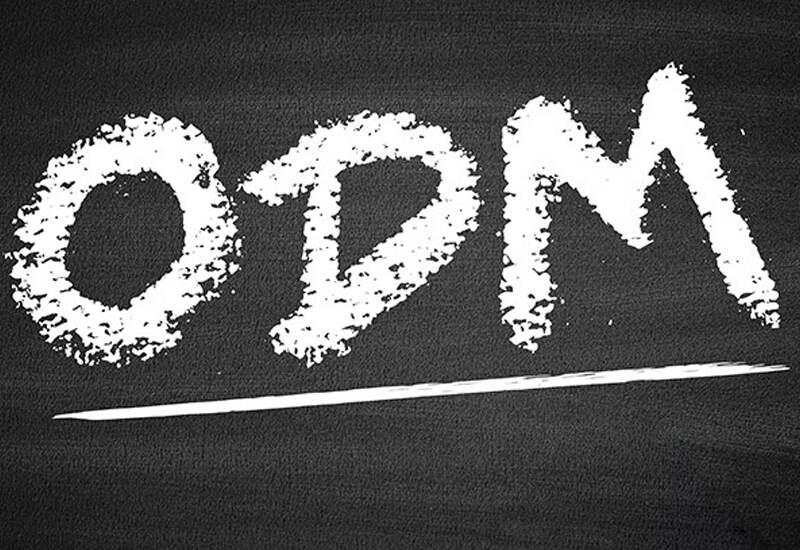
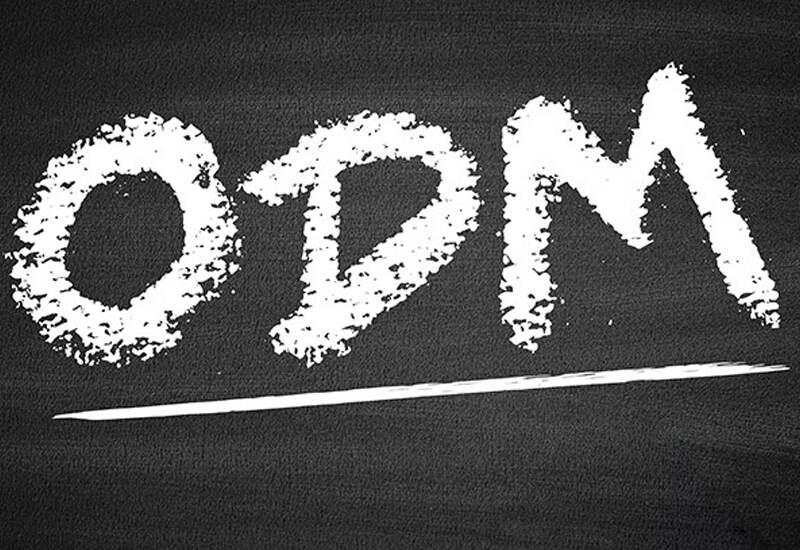
OEM/ODM Services
Using advanced equipment, we provides free mold design based on your drawing and offers assistance with your cotomized product processing.
BLUE's Sintered Ceramics
We offer a range of sintered ceramic products to you, including sintered alumina, sintered zirconia, sintered silicon carbide, sintered silicon nitride, and provide customized services according to your drawings.
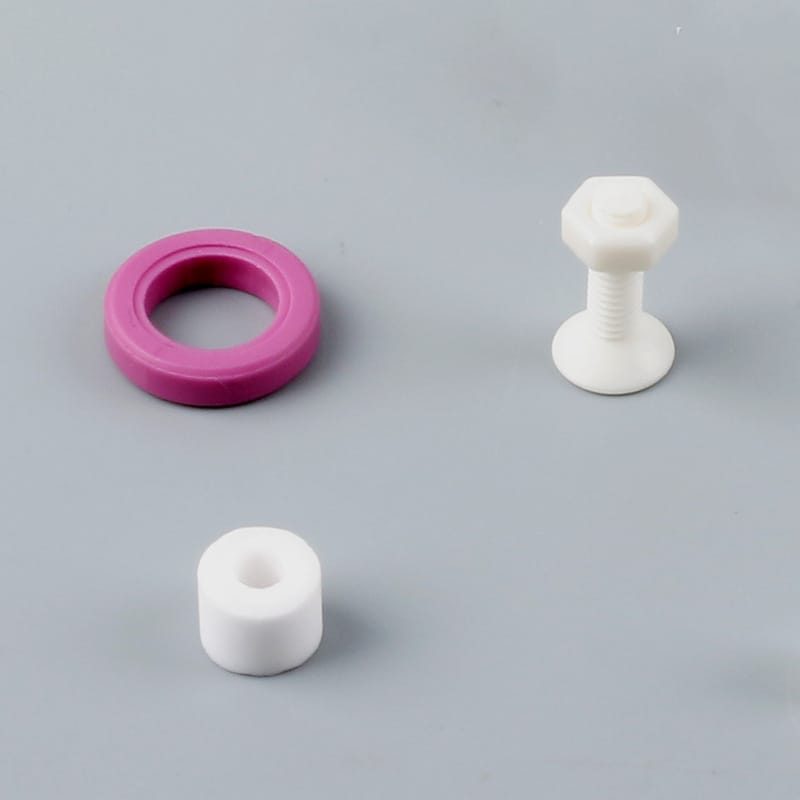
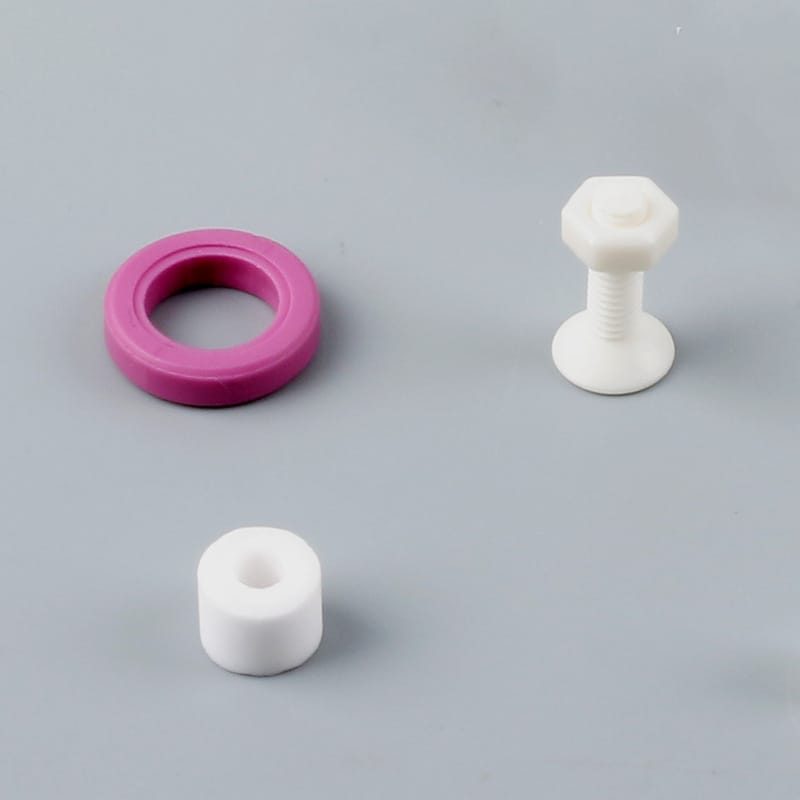
Sintered Alumina
Sintered alumina has high hardness, excellent wear and corrosion resistance, and good high temperature stability.
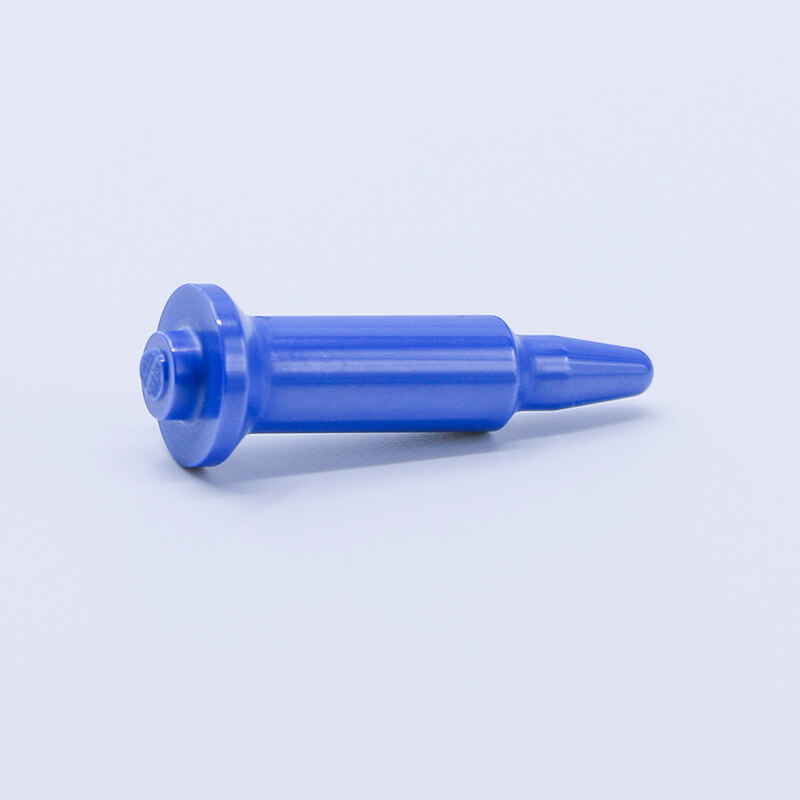
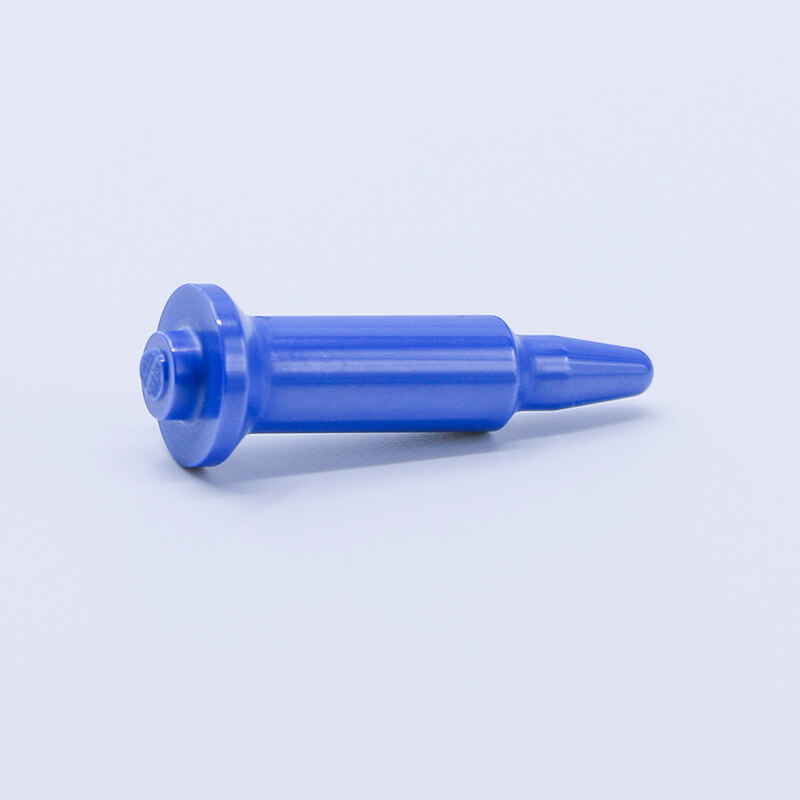
Sintered Zirconia
Zirconia offers high hardness, excellent wear resistance, a very high melting point, and low thermal conductivity.
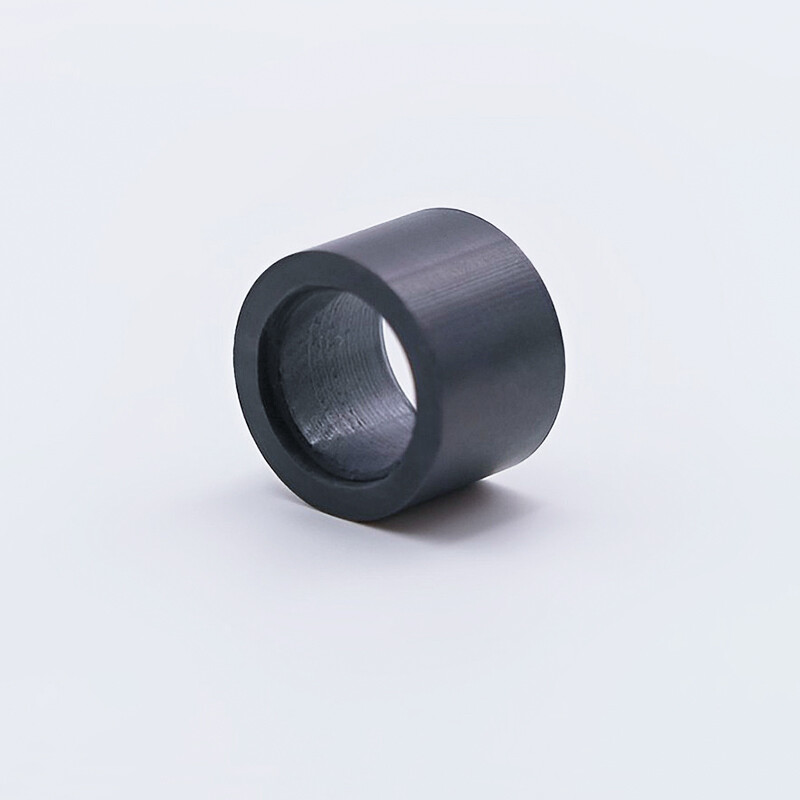
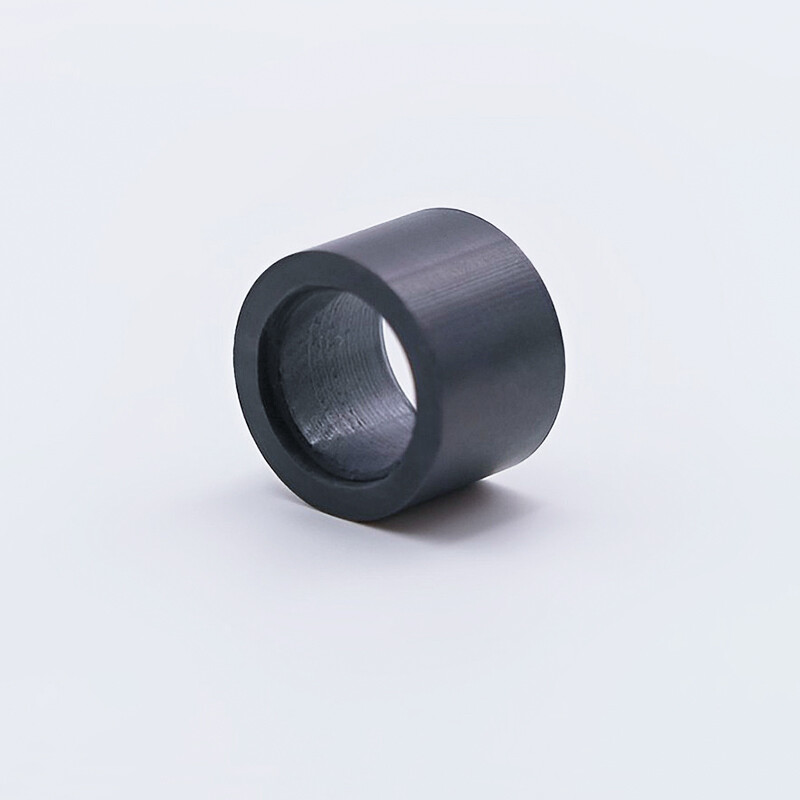
Sintered Silicon Carbide
Sintered silicon carbide is a lightweight, high-performance ceramic used in extreme conditions.
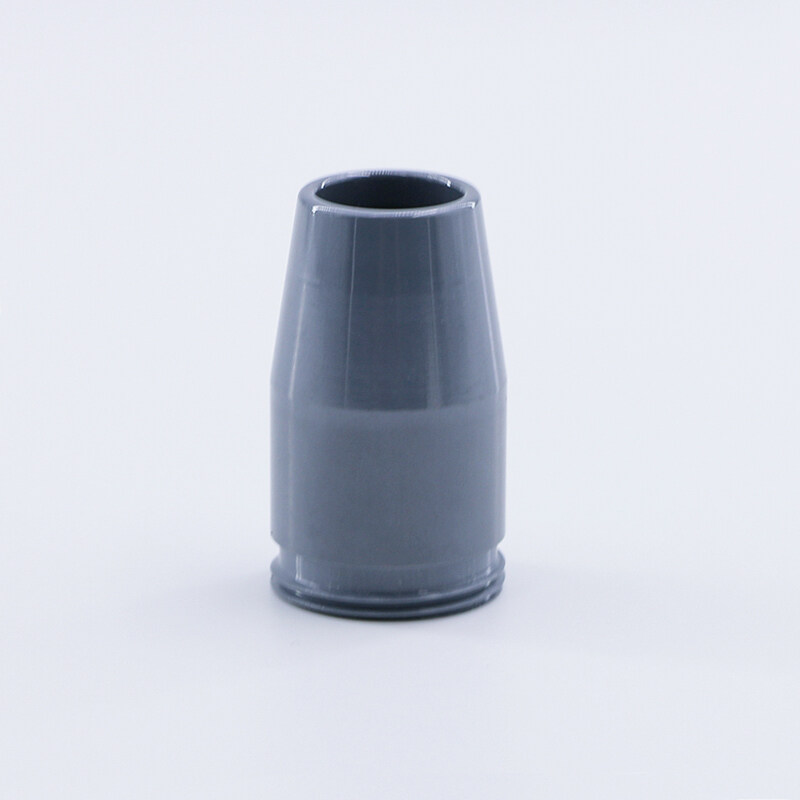
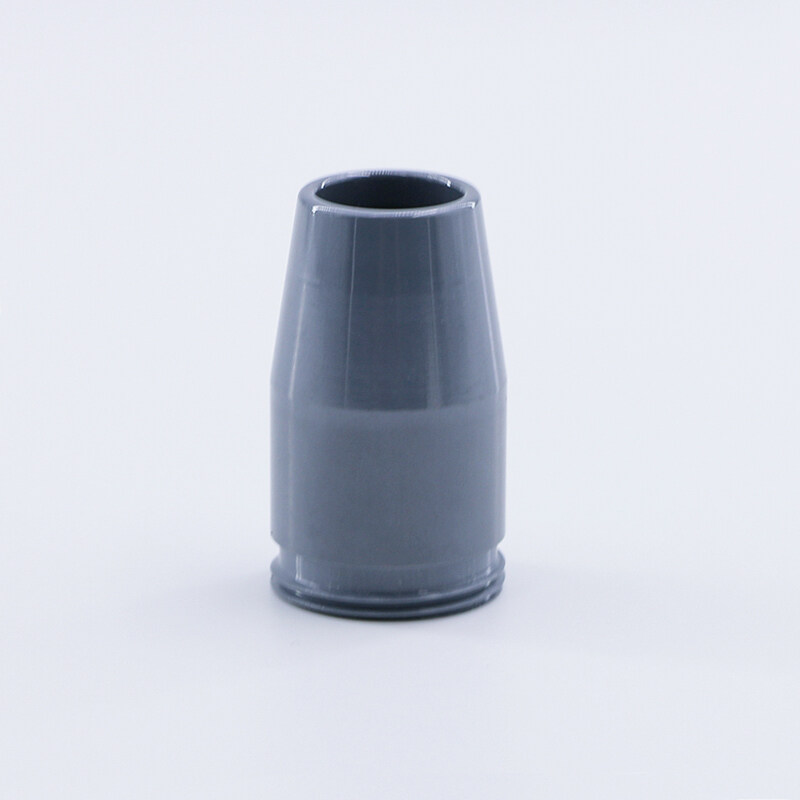
Sintered Silicon Nitride
Silicon nitride has low density, high strength, and thermal shock resistance and has a wide range of applications.
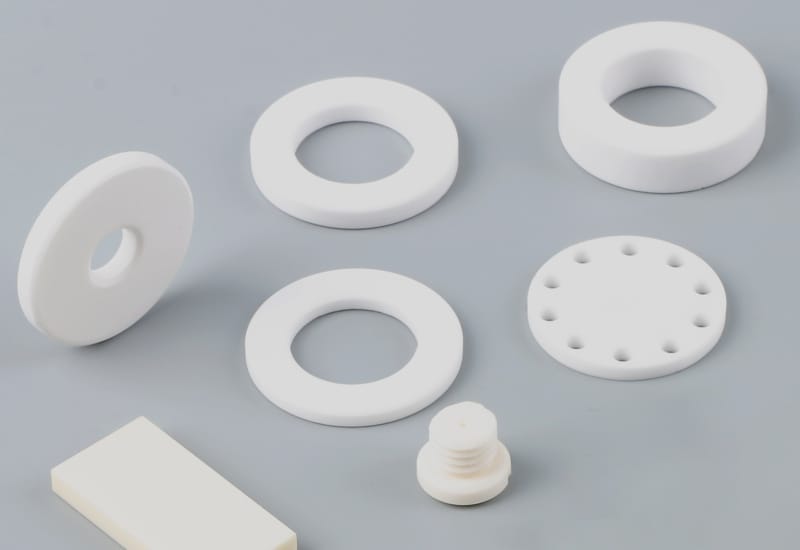
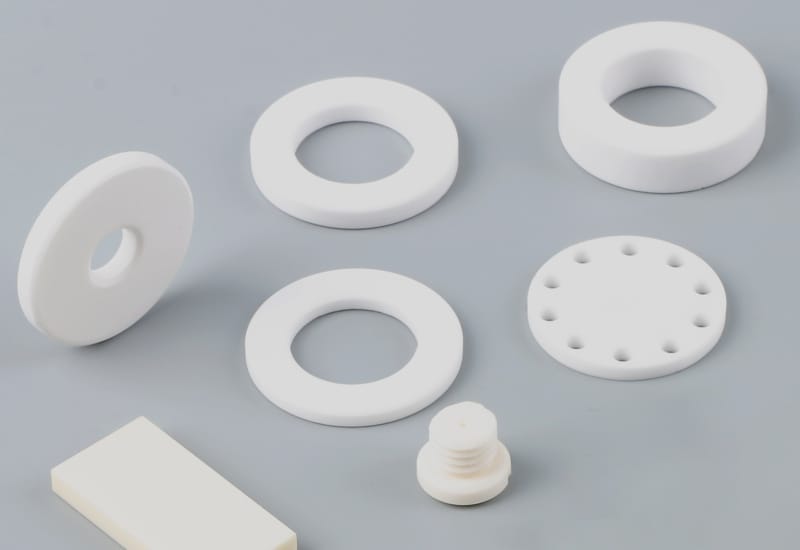
BLUE's Sintered Ceramics Advantages
As a leading sintered ceramic parts manufacturers, Blue offer custom ceramic parts, including ceramic ball bearing, ceramic bushing, ceramic valve.
BLUE has the ability to process a variety of ceramic materials, including alumina, zirconia, silicon carbide, silicon nitride, and boron carbide.
We have a full set of production equipment required for the complete production process of sintered ceramic products, including powder molding machines, isostatic pressing machines, injection molding machines, high-temperature sintering furnaces, CNC machining centers, and testing equipment.
All products will go thorough full inspection to ensure they are qualified, high-quality products delivered to you.
Sintered Ceramics Materials
Alumina ceramic has a low density of 3.9 g/cm³, extremely high hardness (HRA 80-90), and good high-temperature stability.
Silicon nitride offers low density, high bending strength, and excellent wear and corrosion resistance. It can also withstand thermal shock.
As a high-performance ceramic, silicon carbide has a low density (3.1 g/cm³), high strength (550 MPa), high hardness (28,000 MPa), and high thermal conductivity (120 W/(m·K)). It features good wear and oxidation resistance, as well as easy processing.
Zirconium oxide products exhibit good high-temperature stability, heat resistance, corrosion resistance, and tribological properties.
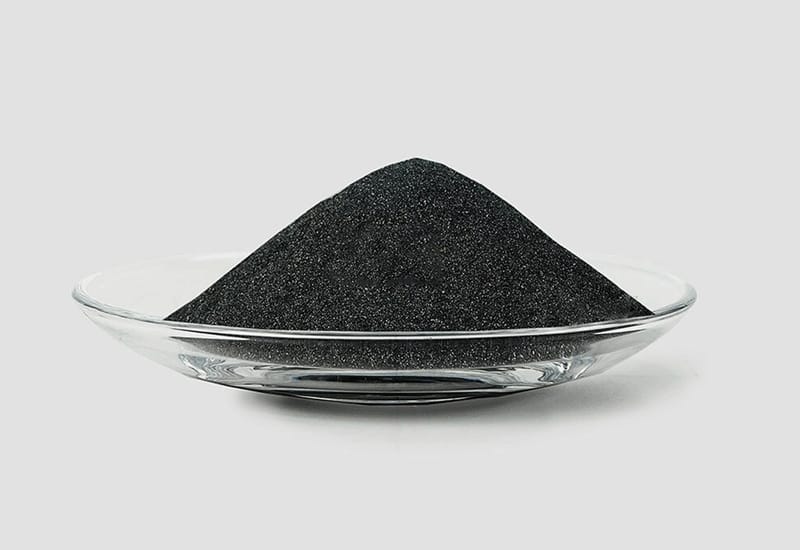
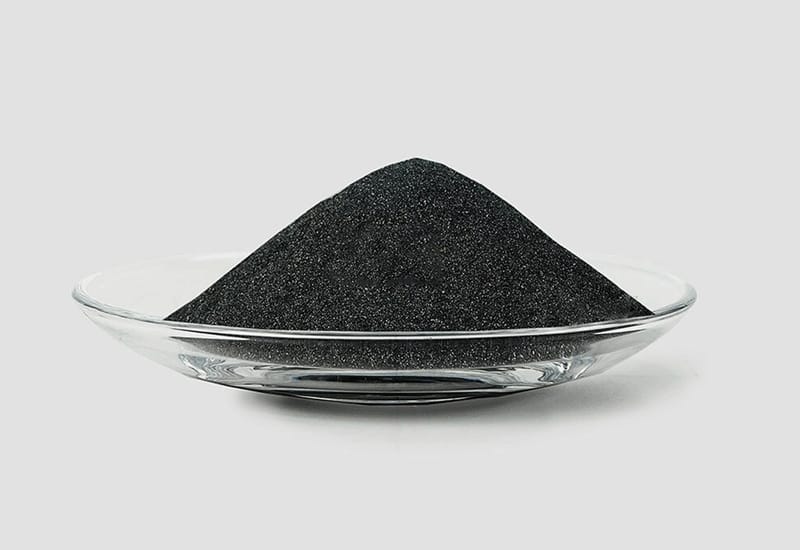
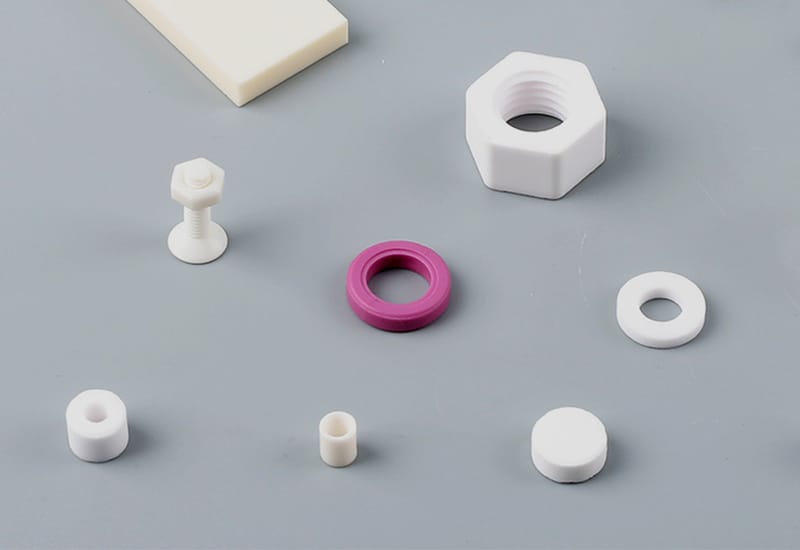
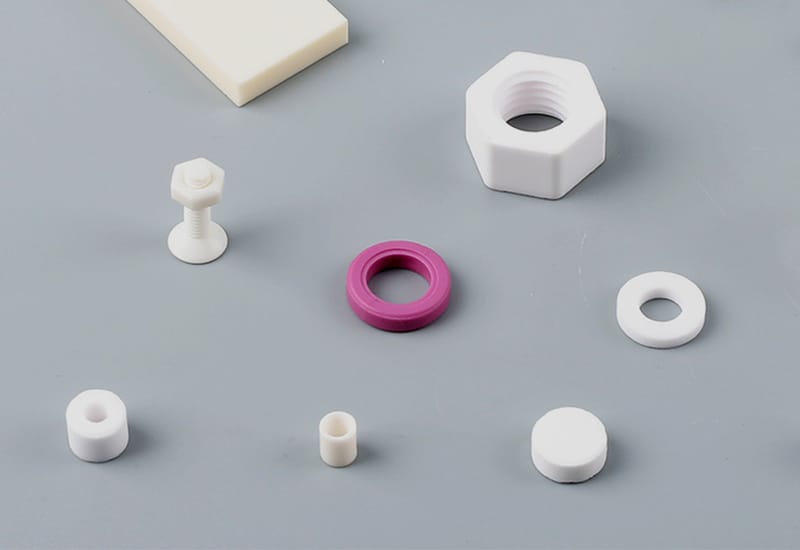
Benefits of Sintered Ceramics
- High hardness
- Low density
- Good corrosion resistance
- Excellent Surface Finish
- High temperature oxidation resistance
- Excellent wear resistance
- Low coefficient of thermal expansion
- High thermal conductivity
- Excellent thermal shock resistance
Applications of Sintered Ceramics
- Automotive: Sintered ceramic parts have excellent high temperature resistance and wear resistance, ideal for high-performance racing automotive engine parts.
- Aerospace: Sintered ceramics like silicon carbide have low density and excellent resistance to high temperatures and pressures, minimizing risks in high-speed aerospace operations.
- Medical: Sintered ceramics can be used as medical implants and exhibit good antibacterial and antiviral properties.
- Cutting Tools: Sintered ceramics, like silicon nitride (8.5 on the Mohs scale), provide high hardness and wear resistance, making them ideal for cutting tools and improving service life and speed.
- Electric Systems: Sintered ceramics like silicon carbide have high breakdown electric field strength and can withstand extreme voltages, making them ideal for circuit protection.
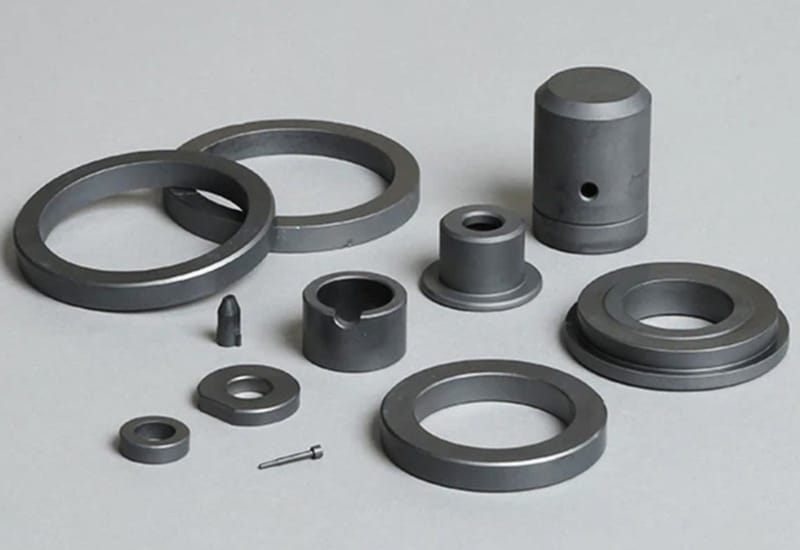
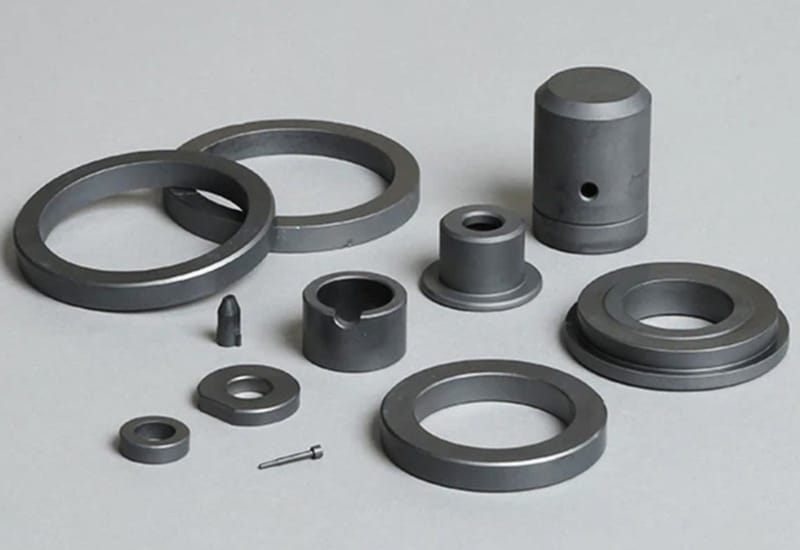
BLUE's Other Manufacturing Capabilities
BLUE covers the full range of powder metallurgy processes, providing one-stop customization for powder metallurgy parts, MIM parts, sintered filters, and sintered ceramic components with strict quality control.
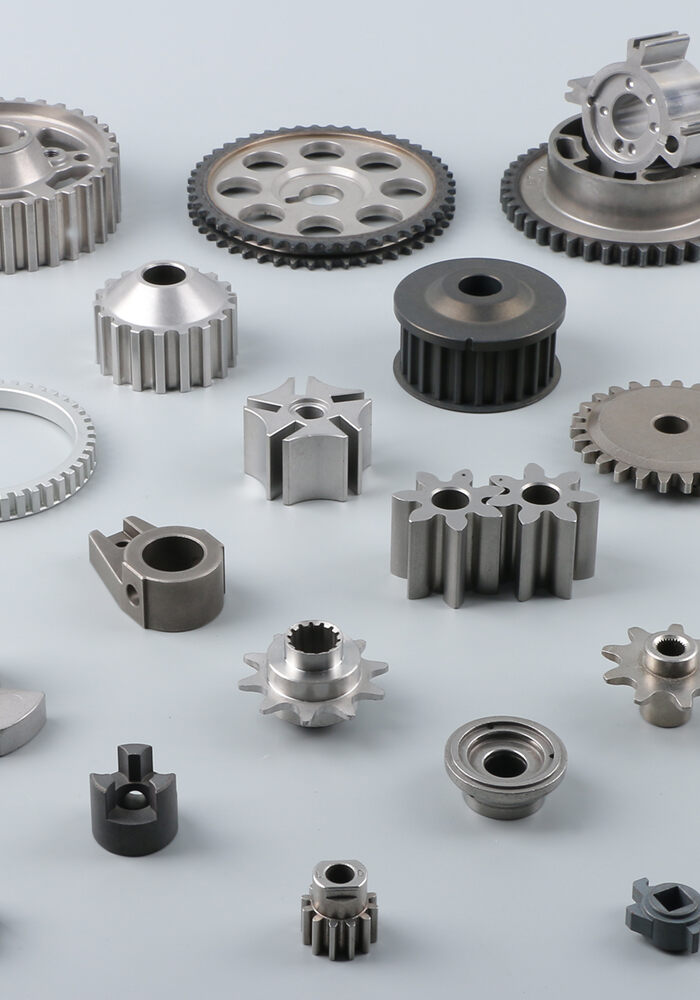
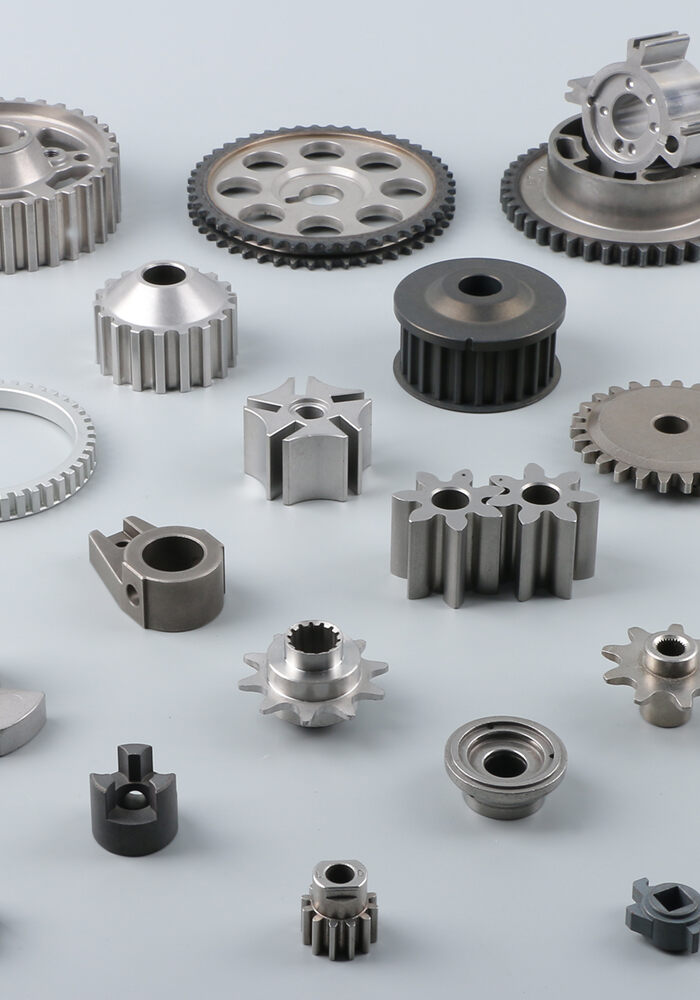
PM Parts
BLUE offers high-precision, strong powder metallurgy parts, customized to meet strict quality standards for various applications.
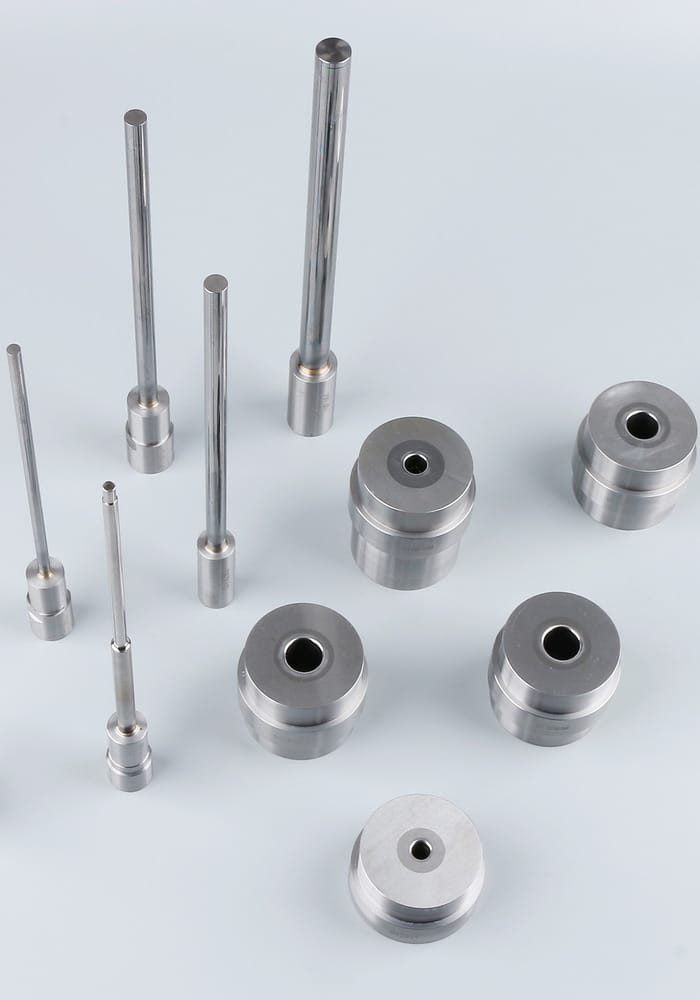
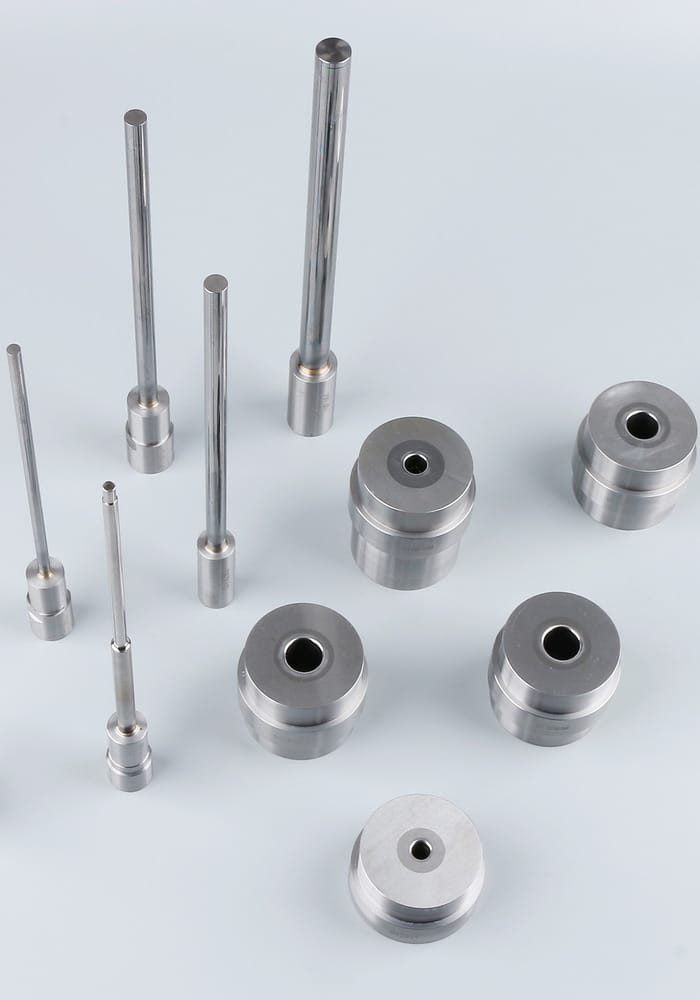
PM Tooling
BLUE has over 20 years of experience in powder metallurgy tooling design and production, with a service life of up to 500,000 cycles.
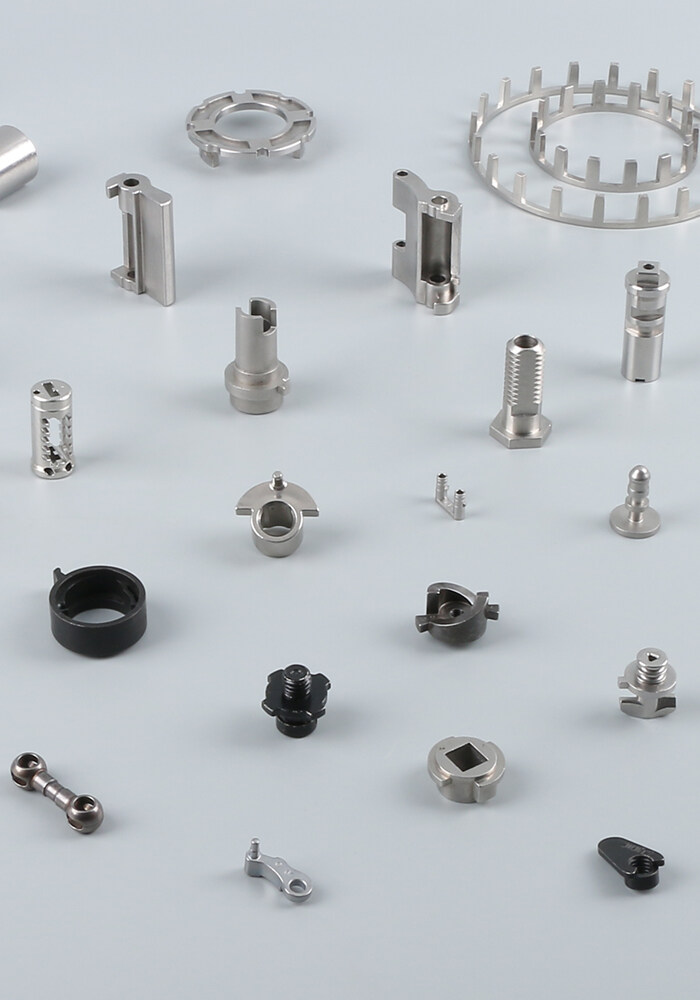
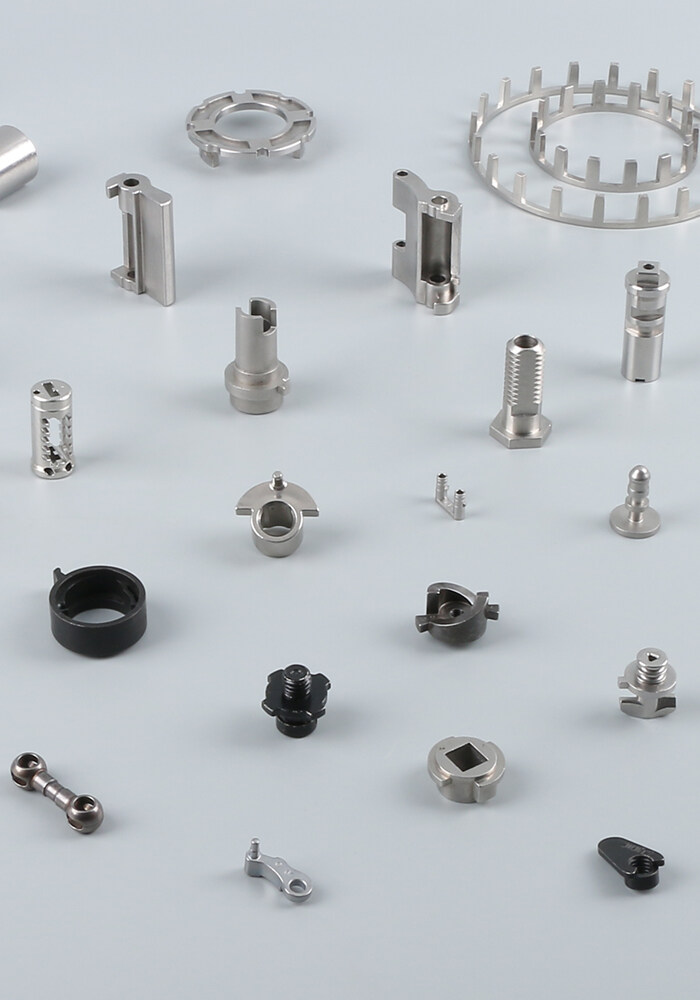
MIM Parts
BLUE's MIM parts feature flexible designs and top strength, produced with consistent quality for complex requirements.
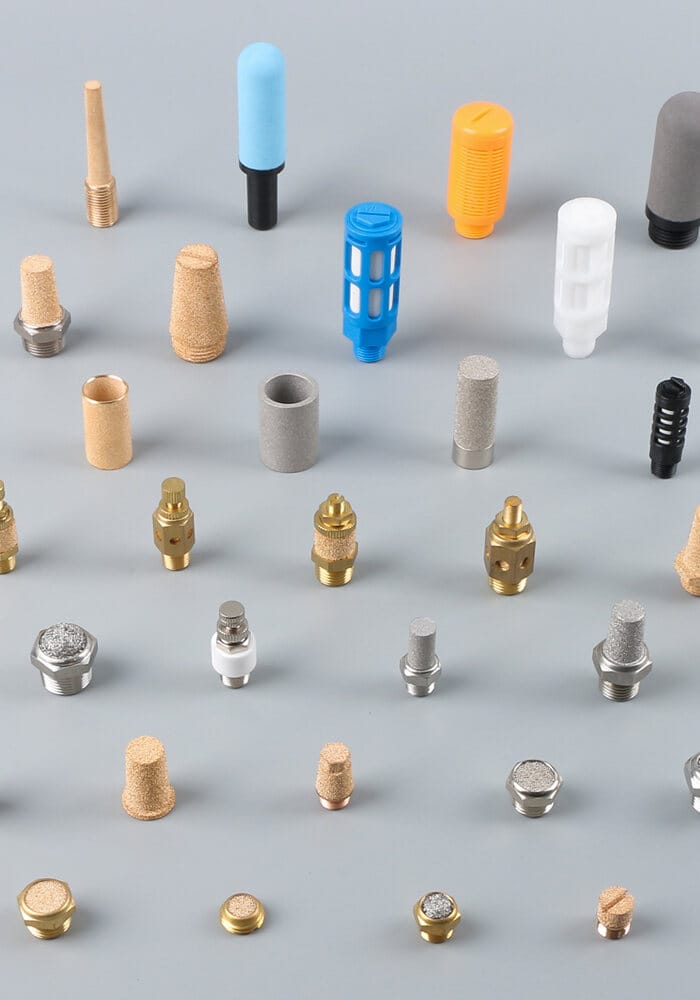
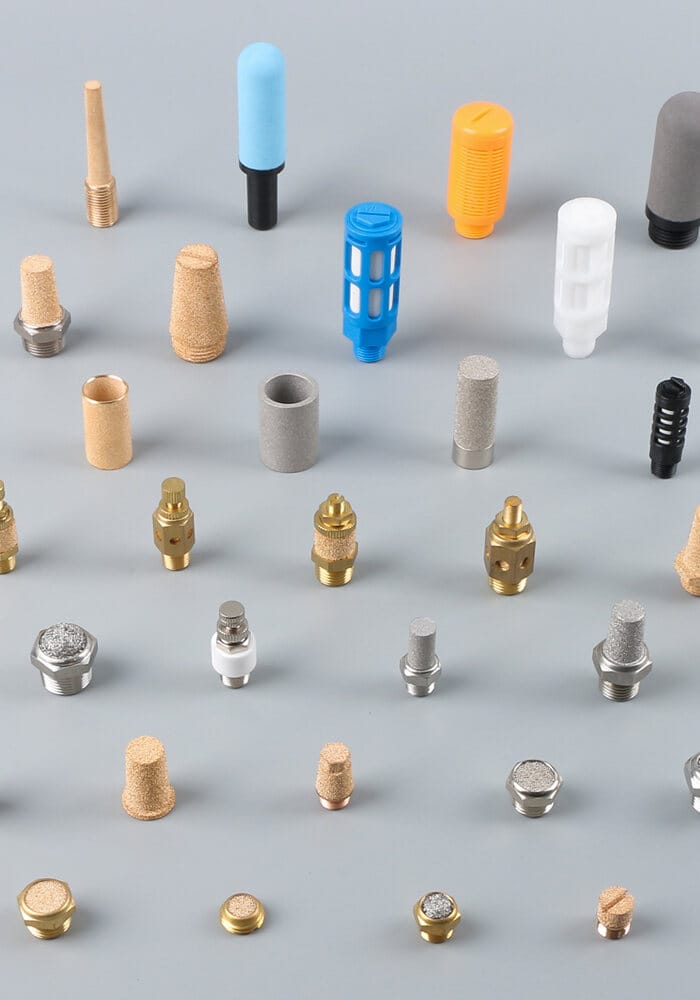
Sintered Filters
BLUE offers a wide range of standard sintered filters in various materials, sizes, and shapes, along with customized services to meet your needs.
FAQ's
Here are some of the questions we get asked often. If yours isn’t answered, don’t hesitate to contact us, we’re happy to help!
There are two main reasons why white alumina changes to pale yellow.
- The internal chemical composition of alumina changes due to sunlight exposure.
- The alumina may have deliquesced, producing hydrated alumina.
Dry Pressing
Dry pressing involves using a powder press to compact ceramic powder into shape, allowing for the manufacture of parts with heights ranging from 0.3 to 60 mm and diameters from 5 to 500 mm.
Powder Injection Molding
Ceramic powder injection molding is similar to metal injection molding, where ceramic powder is shaped using an injection machine.
The advantage of this method is its ability to create small, complex shapes, but it is not suitable for producing large-sized components.
Isostatic Pressing
Isostatic pressing is ideal for creating complex shapes or large, elongated products. This method can produce high-density and uniform parts.