Powder Metallurgy Tooling Supplier - BLUE
With more than 20 years of experience and deep technology, BLUE has the ability to manufacture a variety of powder metallurgy tooling including oil pump gears and rotors, sprockets, pulleys, flanges, etc. Free mold design for all our clients.
Why Choose BLUE?
BLUE is your trusted manufacturer, offering premium powder metal tooling with strict quality control and comprehensive inspection reports before delivery.
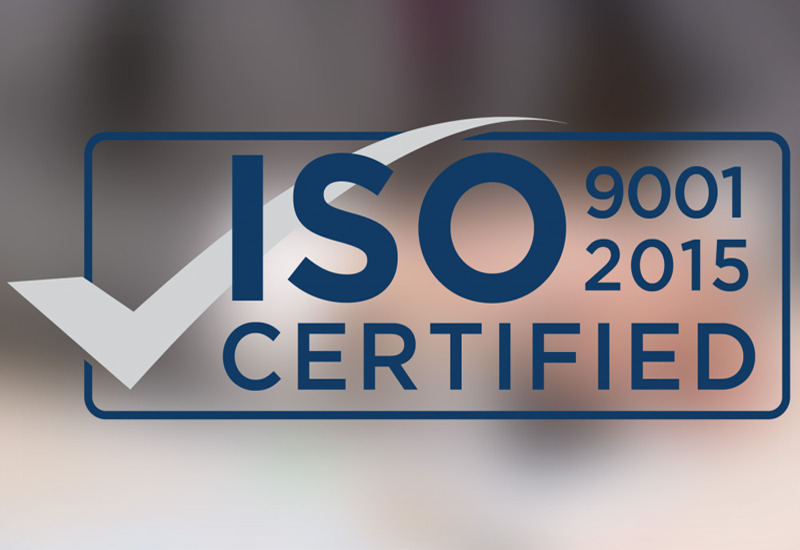
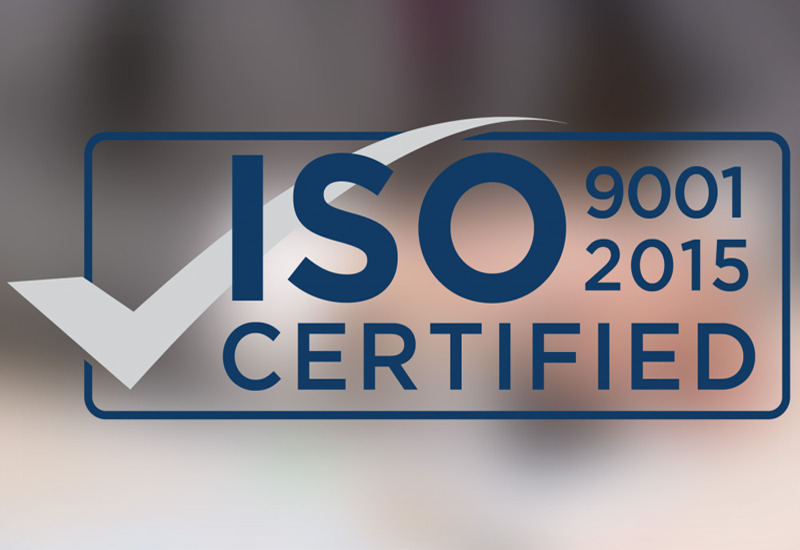
BLUE Quality Standards
BLUE assures your product quality with ISO 9001:2015 certified quality management system. We provide a one-year warranty on your products.
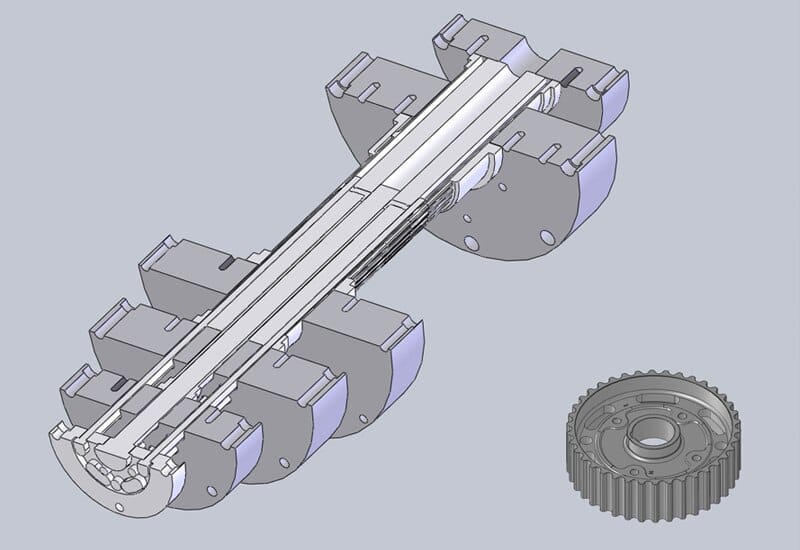
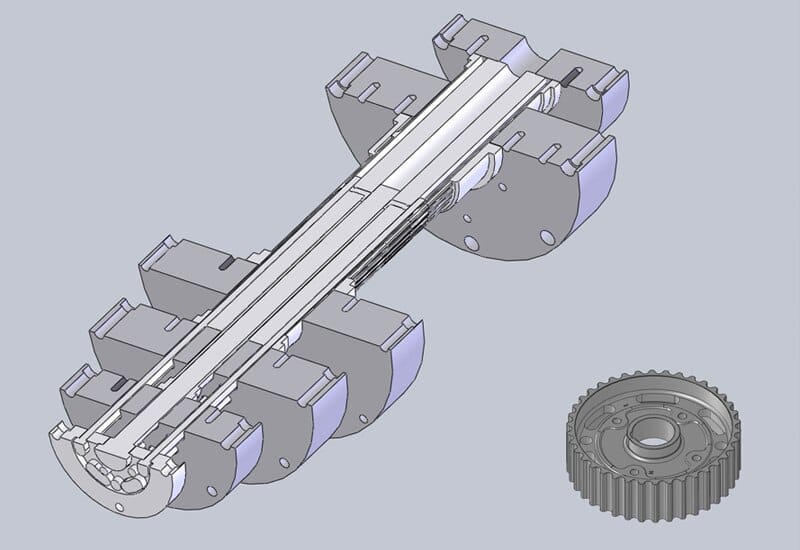
Free Mold Design Service
With over 20 years of expertise in mold design, BLUE offers free, high-precision mold design services to meet your customized needs. Let our experience work for you!
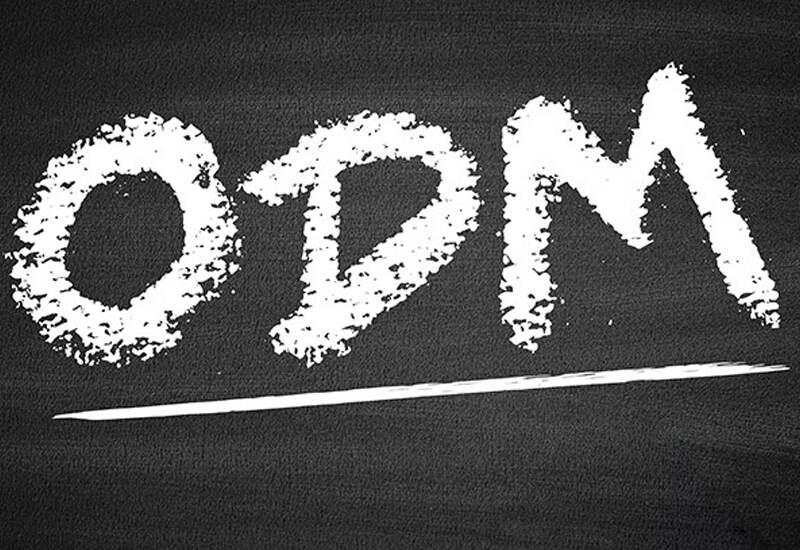
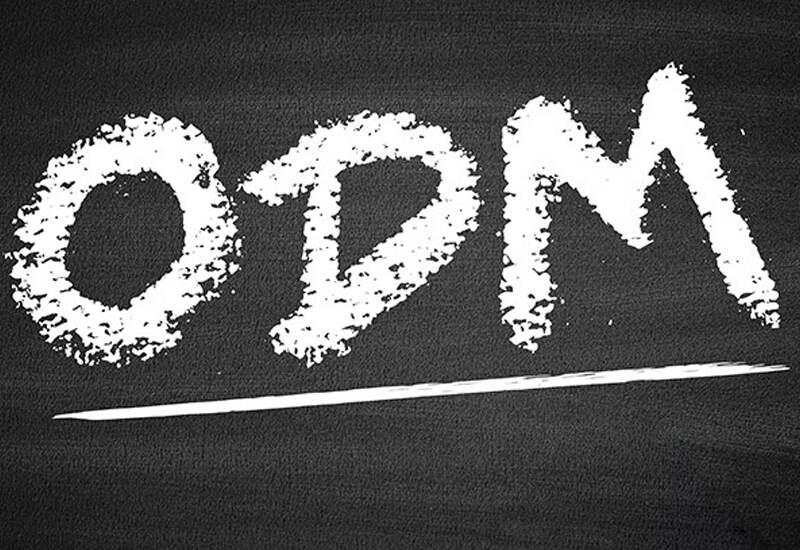
OEM/ODM Services
Using advanced equipment, we provides free mold design based on your drawing and offers assistance with your cotomized product processing.
All Kinds of Powder Metallurgy Tooling
Below are examples of powder metallurgy tooling we have manufactured.
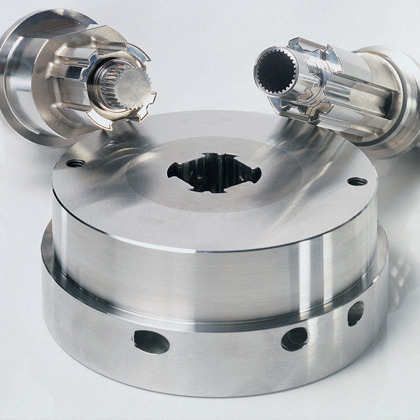
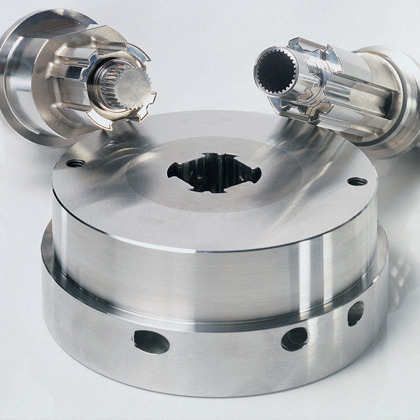
Sintering Mold-Inner Gear
Sintering mold includes upper punch, lower punch, die and core rod, and the service life of the mold is determined by the material and process.
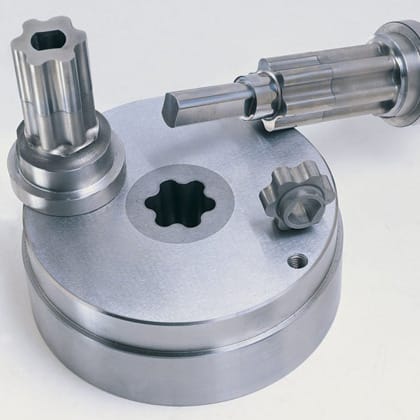
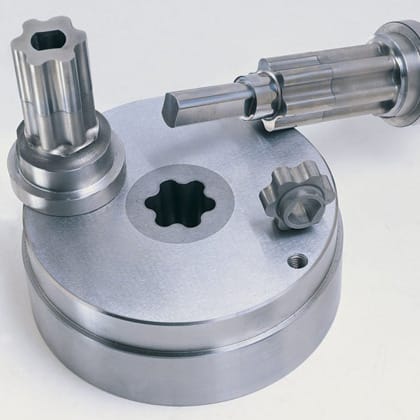
PM Tooling-Oil Pump Rotor
The materials of sintered molds include SKD11, DC53 and YG15. In order to increase wear resistance, the surface will be treated with titanium plating.
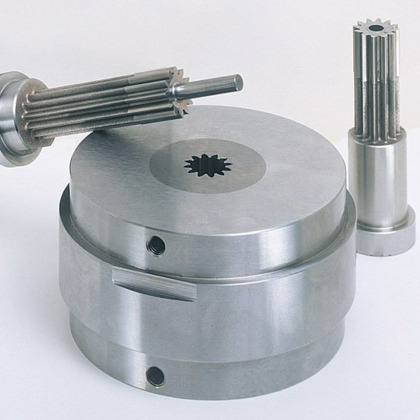
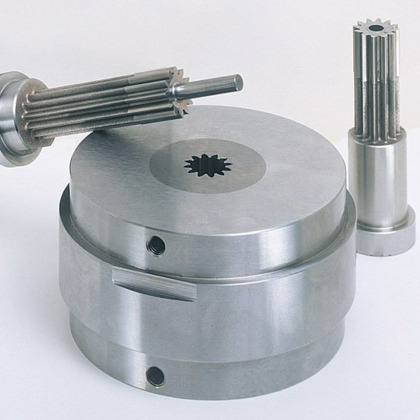
Sintering Die-Spur Gear
BLUE has the capability to manufacture sintering dies with a minimum modulus of 0.1 for spur gears, which require extremely high precision in wire-cutting processes.
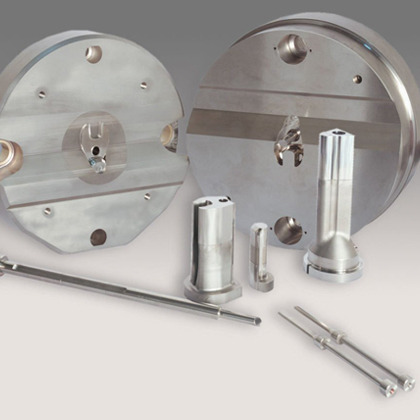
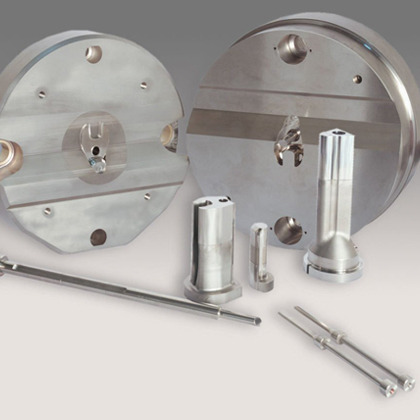
Powder Metal Tooling-Structural Part
The sintered dies produced by BLUE go through a strict carburizing heat treatment process, resulting in a surface hardness of HRC58-62.
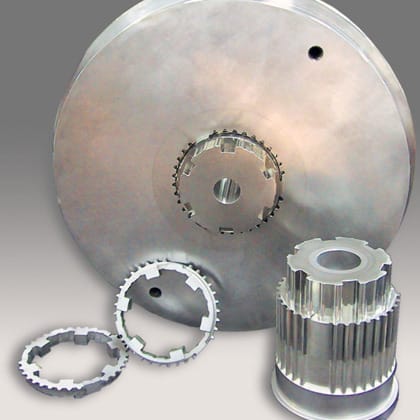
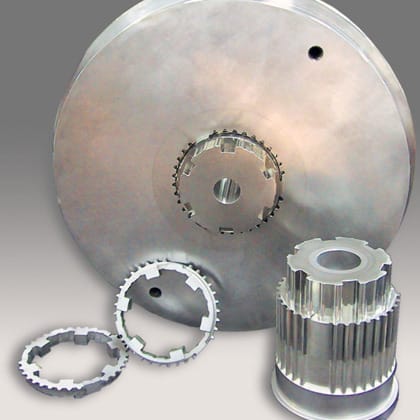
Sintered Metal Die-ABS Sensor Ring
Powder metal tooling can be installed on different compacting equipment, so we it have to design the conversion accessories in advance.
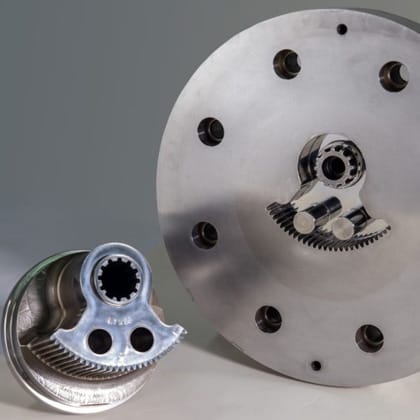
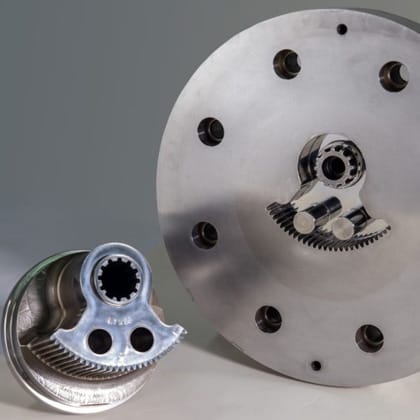
Powder Metallurgy Die-Sector Gear
BLUE's powder metallurgy dies are suitable for 5-ton, 20-ton, 50-ton, 100-ton, 140-ton, 200-ton, 300-ton and 500-ton powder compaction equipment.
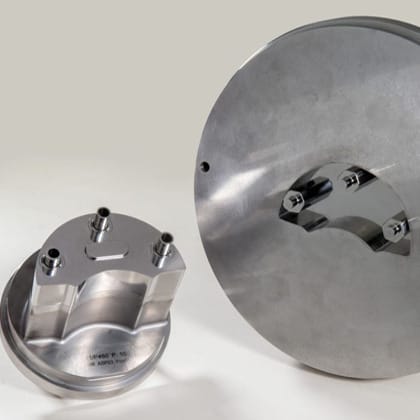
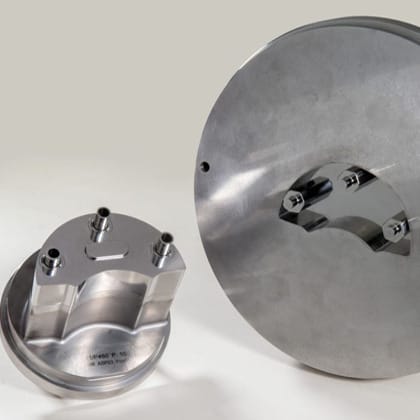
Powder Metallurgy Tooling-Valve Plate
The sintered dies produced by BLUE go through a strict carburizing heat treatment process, resulting in a surface hardness of HRC58-62.
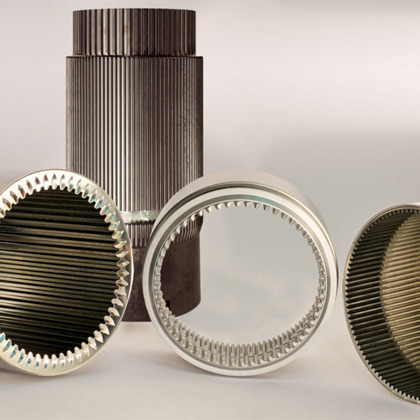
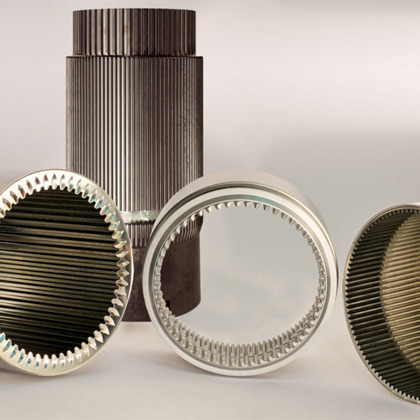
Sintered Compaction Mold-Gear Ring
Powder metal tooling can be installed on different compacting equipment, so we it have to design the conversion accessories in advance.
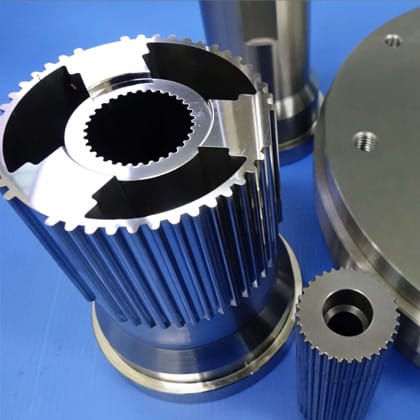
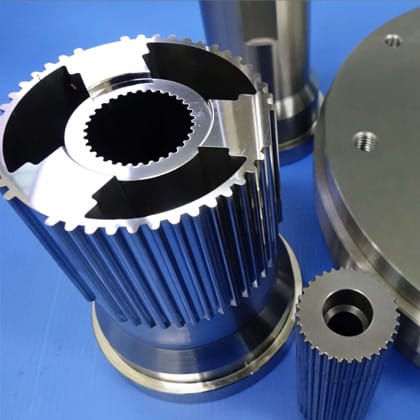
Powder Metallurgy Mold-Synchronous Gear Hub
BLUE's powder metallurgy dies are suitable for 5-ton, 20-ton, 50-ton, 100-ton, 140-ton, 200-ton, 300-ton and 500-ton powder compaction equipment.
Sintering Mold Materials
Powder Metallurgy die cavity must withstand the vertical pressure from the punch and the lateral force from powder extrusion, requiring high strength, hardness, and excellent wear resistance.
Therefore, we typically use materials like D2, M2, SKD11, CPMV10, DC53, YG15, and C11 for most powder metallurgy die inner cores.
The upper and lower punches need good toughness and fatigue resistance, so we primarily use tool steels such as A2, SKD11, SKD12, and DRM2.
Since the core rod is long, it must have high tensile strength. For this, we use high-tensile tool steel like SKH9.
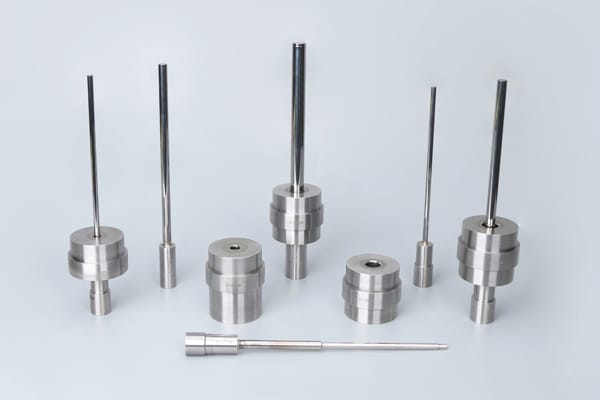
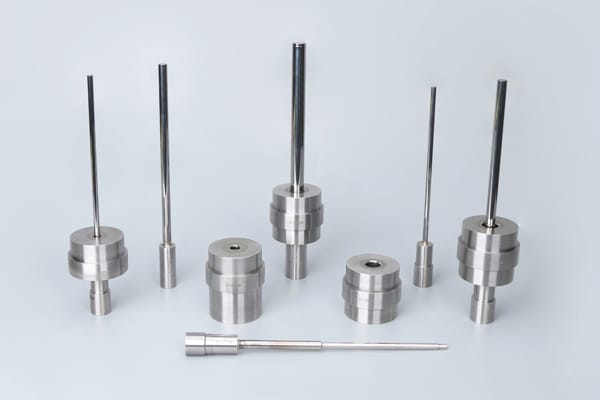
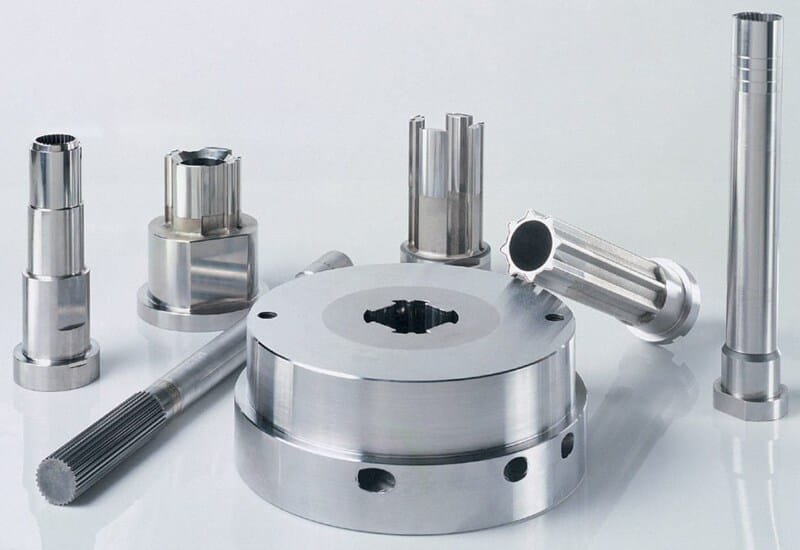
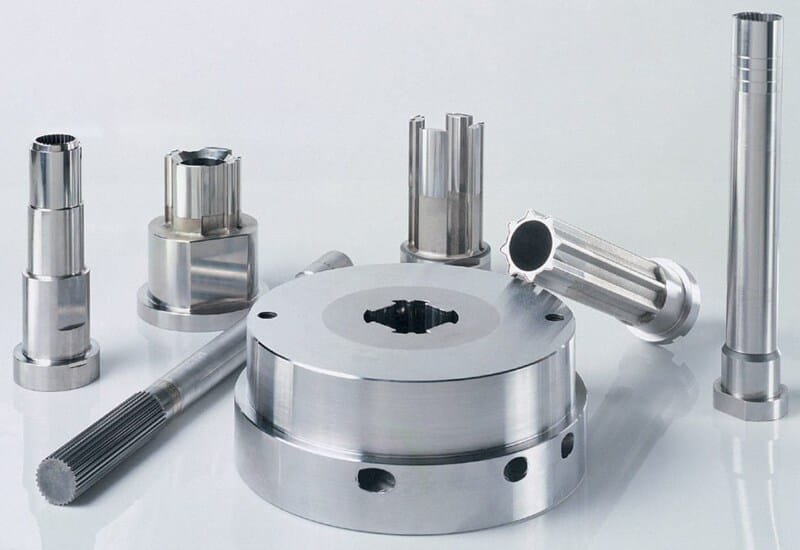
Powder Compation Tooling
With over 20 years of experience, BLUE is capable of designing and manufacturing molds for various powder metallurgy parts, including oil pump gears & rotors, oil impregnated bushings, water pump flanges, sprockets, shock absorber accessories, etc.
Our powder compaction tooling size tolerance can reach ±0.002mm, surface finish is Ra0.2-0.4μm, and position accuracy is within 0.003mm.
When designing your powder metal mold, we will fully consider various factors including expansion during demoulding, shrinkage or expansion during sintering, and the reserve of sintered products.
Powder Metallurgy Sizing Die
Sizing is an important secondary operation for powder metallurgy parts after sintering.
Sizing can not only improve the linear tolerance of sintered parts to within ±0.01mm, but also improve the surface finish of the product and the surface sealing of oil impregnated bushings.
The shape of the sizing die is generally simple compared to the compacting die. Generally, sizing is for a specific size of inner diameter, outer diameter, or height.
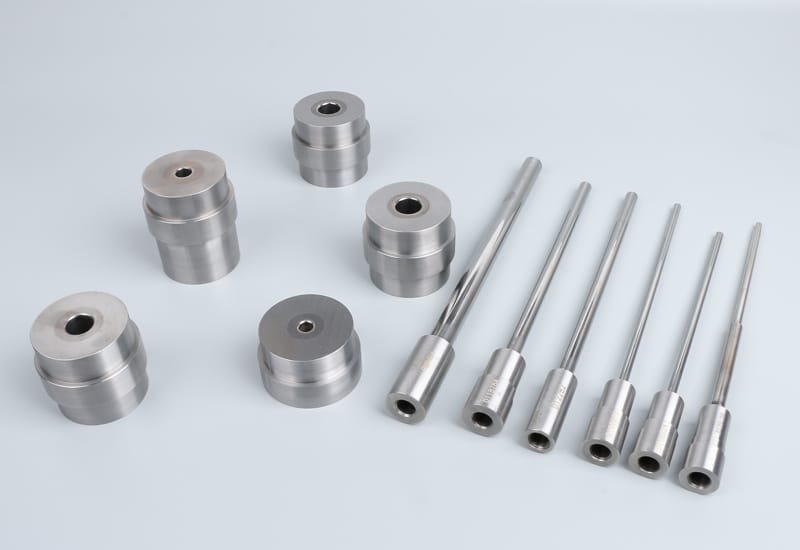
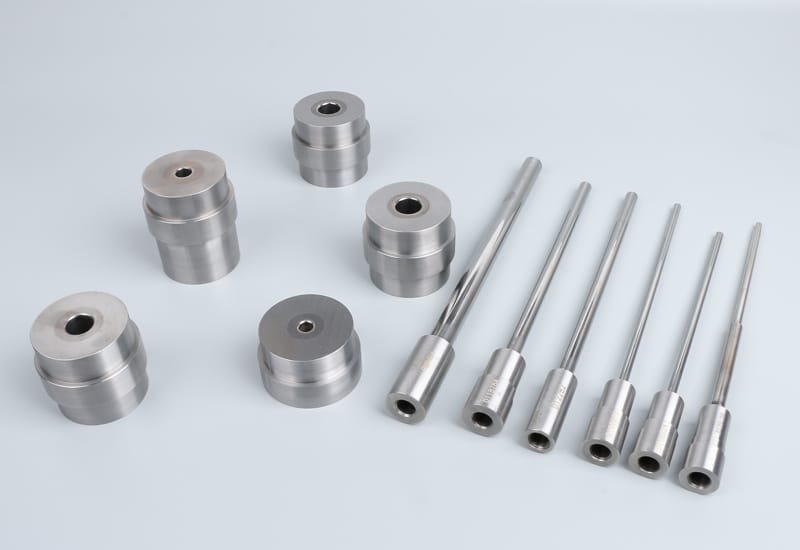
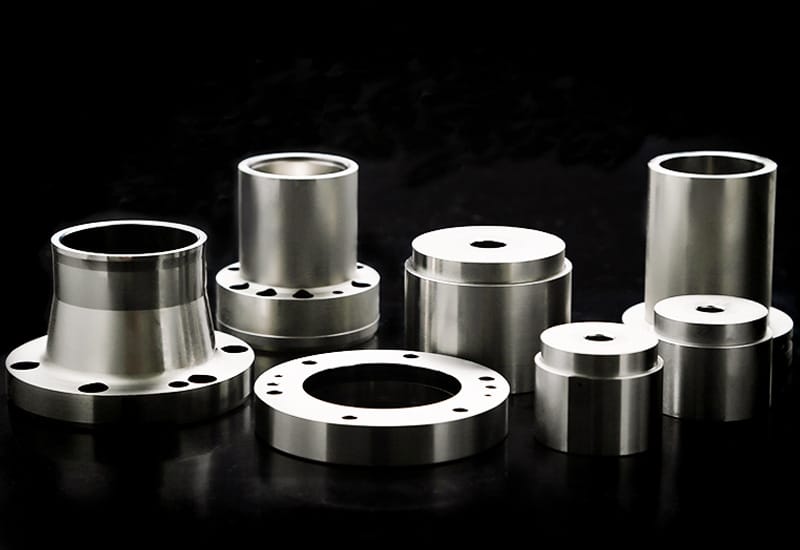
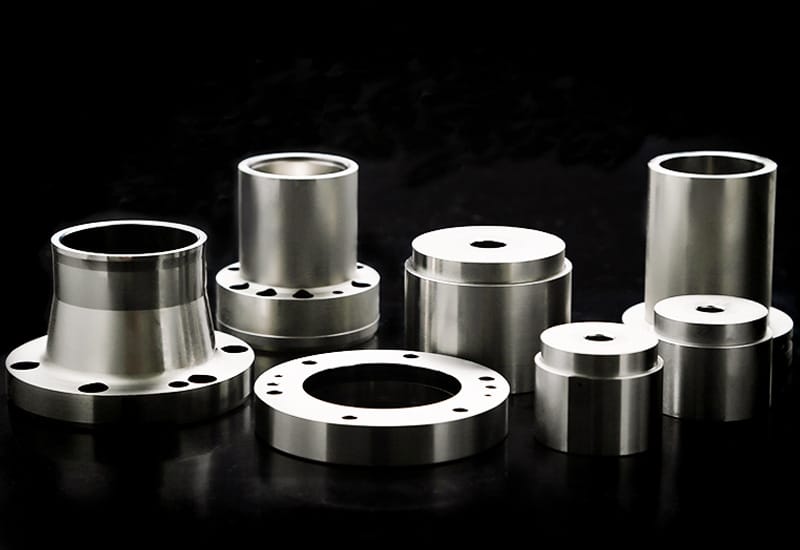
Powder Metallurgy Tooling Accessories
In addition to powder metallurgy compacting and sizing molds, we can also provide a range of powder metallurgy mold accessories, including:
- Upper punch support plate
- Guide pillars
- Die template
- Die holder
- Bottom mold base
- Sliding plate
- Core rod fixing ring
- Core rod support plate
Handcrafted Polishing Process
BLUE is committed to manual polishing and trial fitting for every powder metallurgy tooling we produce.
This meticulous process achieves micron-level precision in matching the upper punch, lower punch, core, and die, ensuring high-quality products that perform reliably in the field.
Our attention to detail allows us to identify potential issues during production and make necessary adjustments, guaranteeing that our customers receive molds of the highest quality.
So, if you need a custom powder metallurgy tooling, you can rely on BLUE to deliver the quality and performance you need for success.
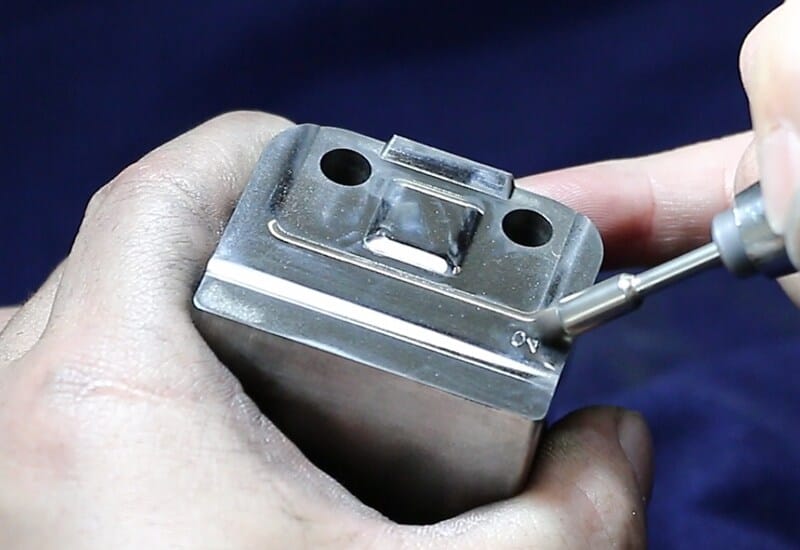
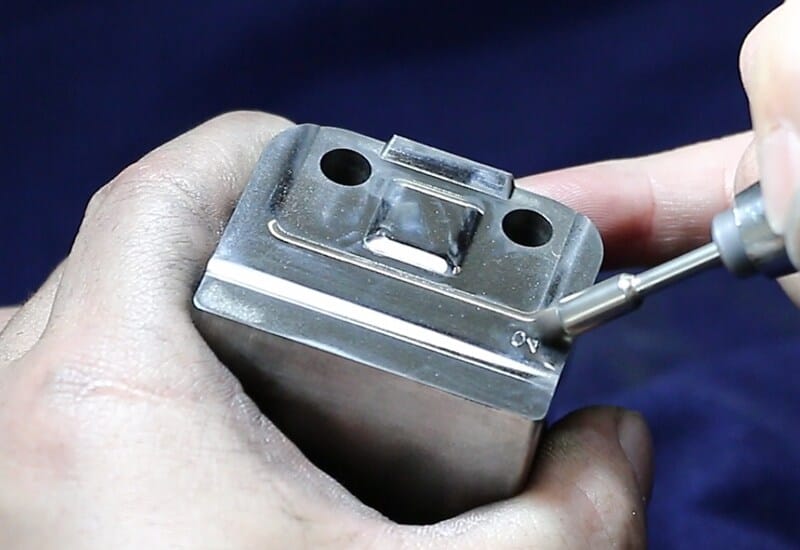
Various Powder Metallurgy Tooling Designed by BLUE
The following pictures are some of the powder metallurgy tools we designed. We use SolidWorks, ProE, UG and AutoCAD software to design your molds.
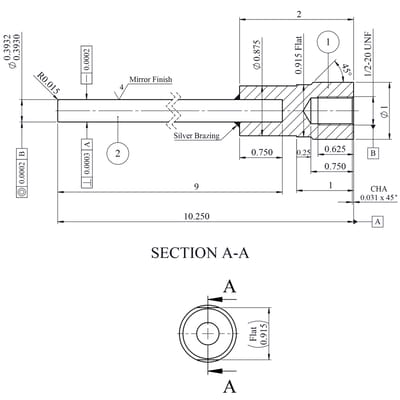
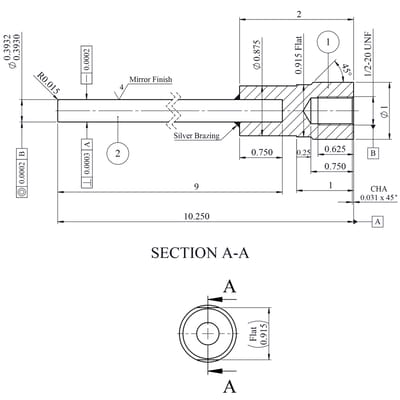
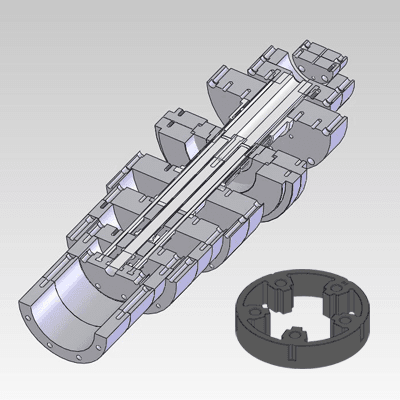
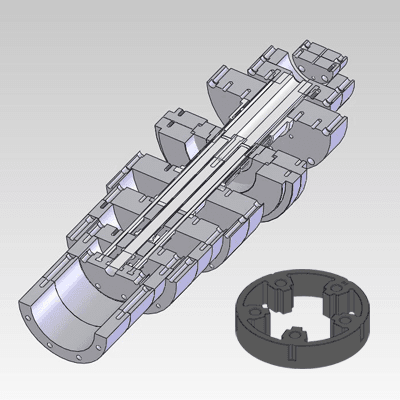
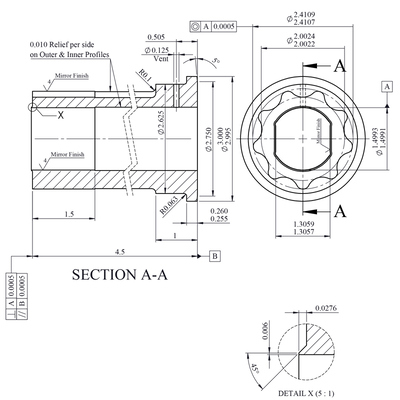
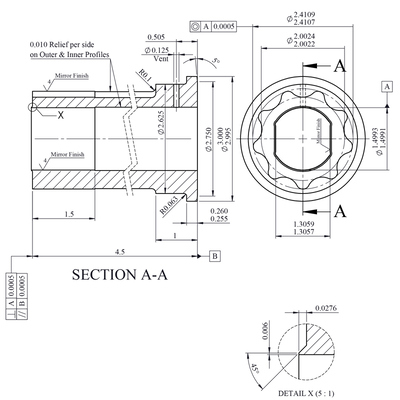
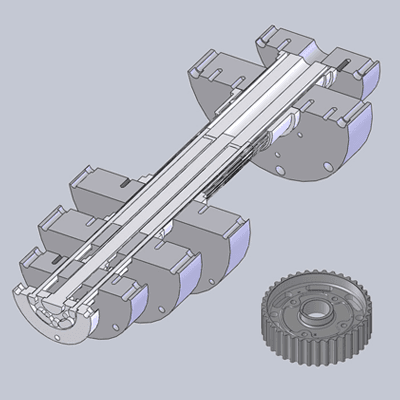
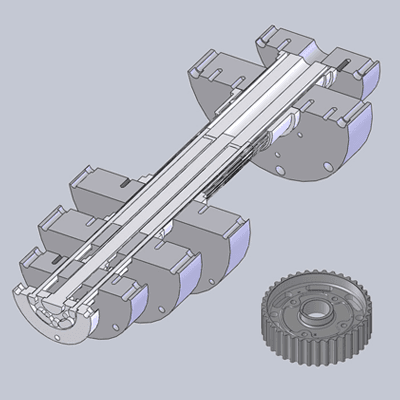
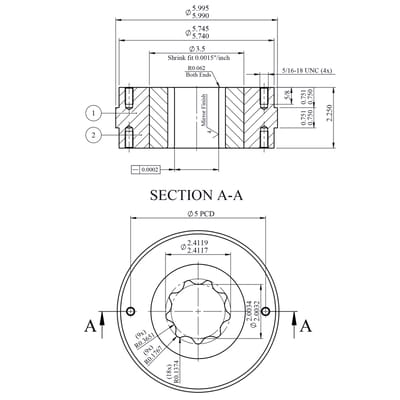
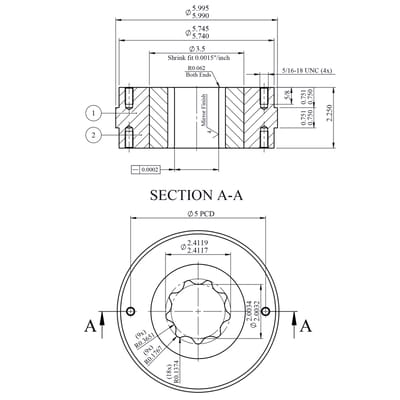
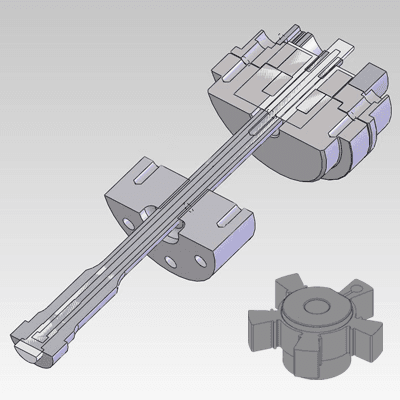
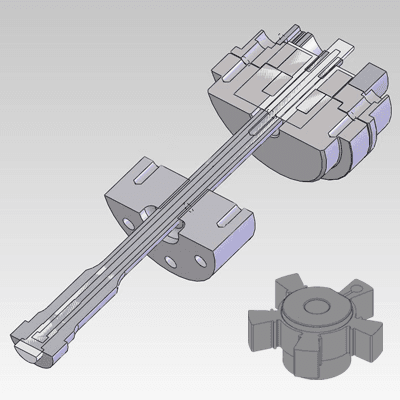
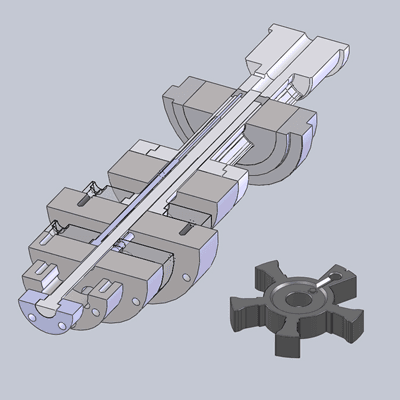
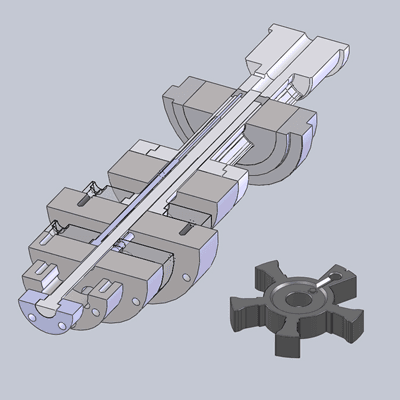
BLUE Sintering Mold Production Equipment
BLUE uses high-standard raw materials and advanced and complete mold production equipment to manufacture your powder metal tooling to ensure high quality.
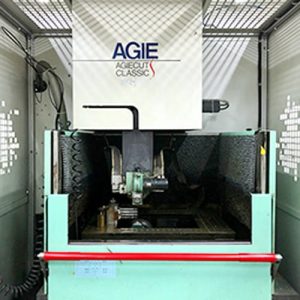
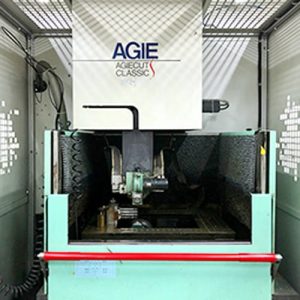
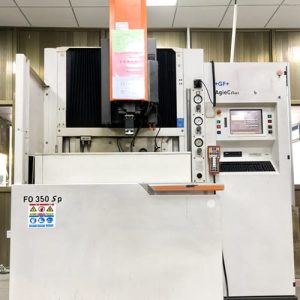
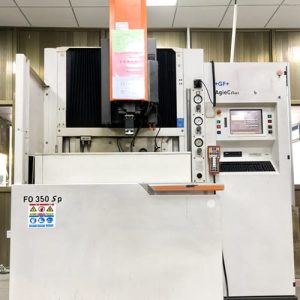
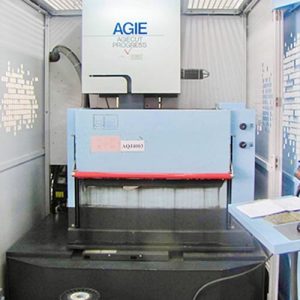
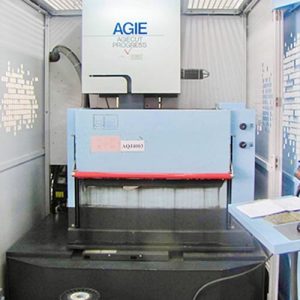
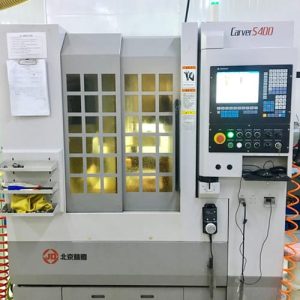
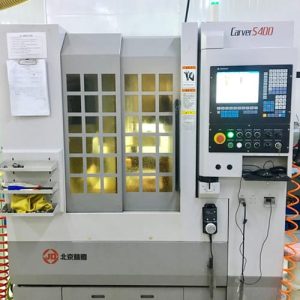
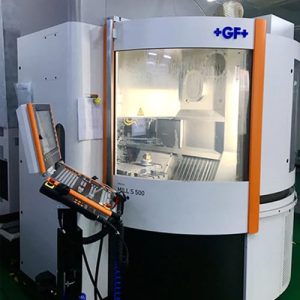
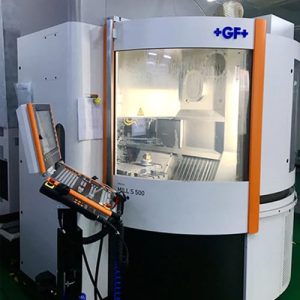
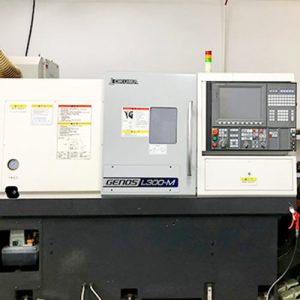
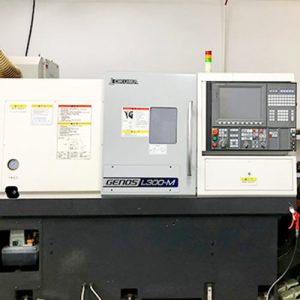
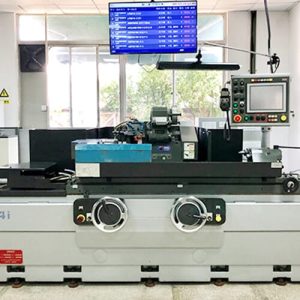
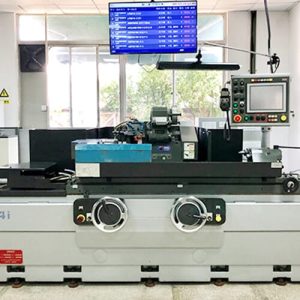
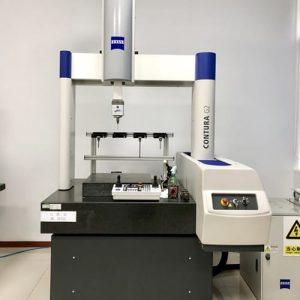
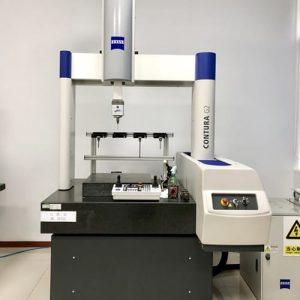
FAQ's
Here are some of the questions we get asked often. If yours isn’t answered, don’t hesitate to contact us, we’re happy to help!
Powder metal tooling is used to mold powder metallurgy parts with extremely high dimensional accuracy.
Powder is placed into a mold and compressed under high pressure to form the desired shape. The resulting “green” compact is then placed in a furnace for sintering, which fuses the metal particles together and strengthens the structure.
The advantages of powder metal tooling include the ability to produce complex shapes, achieve high precision, and use less material compared to traditional manufacturing methods.
The powder metallurgy molds manufactured by BLUE can press approximately 500,000 pieces.
- Visual inspection: Conduct a visual inspection of the tooling to identify any surface defects or dimensional irregularities.
- Dimensional measurements: Use precision measuring instruments(CMM) to verify the tooling’s dimensional tolerance, including its diameter, length, height and assembly.
- Hardness testing: Perform a hardness test to ensure the tooling has the appropriate hardness and is not too brittle or too soft.
- Microstructure analysis: Examine the microstructure of the tooling to verify that it has been processed correctly and has the appropriate grain size and distribution.
- Surface roughness analysis: Measure the surface roughness of the tooling to ensure that it is within acceptable limits and won’t cause issues during the production process.
- Functionality testing: Test the tooling in a simulated production environment to ensure that it is functioning as expected and can produce quality parts.
- Fatigue testing: Test the tooling for fatigue resistance to verify that it can withstand repeated use without degrading or failing.
- Wear testing: Conduct wear testing to evaluate the tooling’s resistance to wear and identify any areas that may require additional surface treatment or coatings.
- Destructive testing: Conduct destructive testing to identify any defects or weaknesses in the tooling that may not be visible through other inspection methods.
- Maintaining powder metal tooling is crucial to ensuring that it performs at its best and lasts for a long time:
- Clean the tooling after each use to prevent any buildup of dirt, grime, or powder metal residue.
- Inspect the tooling regularly for any signs of wear or damage, such as cracks or chips.
- Lubricate the tooling before each use to prevent excessive wear and tear.
- Store the tooling in a cool, dry place to prevent corrosion or rust.
The amount of time it takes to produce powder metal tooling can vary depending on a number of factors, including the complexity of the design, the size of the mold, and the materials being used.
In general, the process of designing and manufacturing powder metal tooling can take several days to several weeks.
At BLUE, we strive to complete all mold production and processing within 15 days, and our mold design can typically be completed within 3 days.