Forging is known for producing parts with great strength. Do you consider combine these process? Powder metallurgy (PM) is a popular processing that make near net shape parts. That is the point.
Combine conventional “press and sinter” method and forging process, this is referred to powder forging, or powder metal forging.
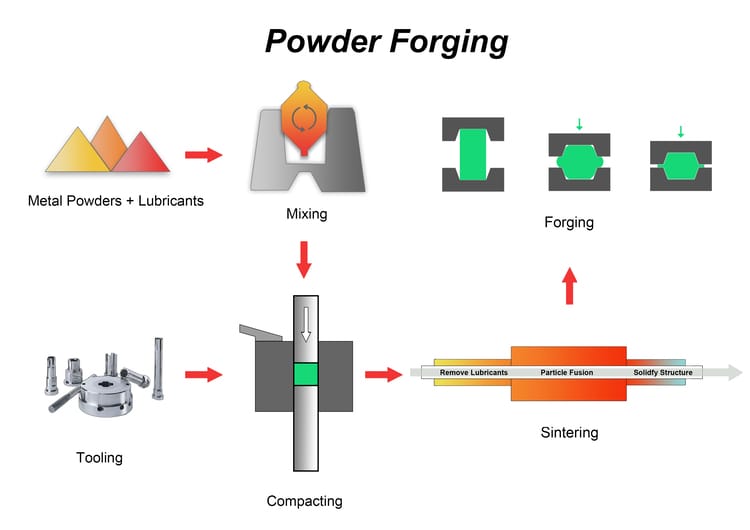
Contents
Powder Forging Process
Select Raw Materials
Powder forging requires high material purity and low oxygen content so that the finished parts can have sufficient strength and toughness. During the sintering and forging process, since alloying elements are difficult to diffuse evenly, manufacturers usually use pre-alloyed powder.
Mixing
The powder mixing process usually takes about an hour to obtain a uniform mixed raw material. In this process, some additives are usually added to ensure adequate mixing and lubrication of compacting process.
Pressing
Compaction is the process where the metal powder is formed, and you need to pay attention to the following points.
If the green density is too low, cracks will appear during forging. If it is too high, it can damage the mold and hinder the densification of the parts.
Sintering
After the metal powder is formed, you feed the part into a conveyor furnace. Sintering takes place at a temperature below the melting point of the metal. The sintered part is then sent to the next process.
Forging
You then place the preform into a forging die and apply high pressure using a forging press. This process further compacts the material, increasing its density and enhancing its mechanical properties.
You may know that forging can be categorized by temperature into cold forging and hot forging. Besides, based on the mold type, forging can be classified into open die forging and closed die forging.
Powder Forging Methods
Common powder forging methods usually include the following:
Cold Powder Forging
Powder cold forging is the process of forging sintered parts with a density of 75% to 85% at room temperature. After cold forging, the surface of the parts is smooth and the size is easy to control.
This process requires that the sintered parts have sufficient strength. Generally, in order to increase the density of sintered parts, they often go through the copper infiltration. Luckily, through the powder cold forging process, the density of the parts is fully improved, and no additional infiltration process is required.
Hot Powder Forging
- Direct Powder Forging after heating
In this process, the compacted powder is heated and shaped and then directly forged. This method is simpler than others, does not require sintering, and can save more energy. Moreover, it is not affected by the production speed of the sintering furnace and has the fastest production speed.
- First sintering and then forging
This process is to reheat the sintered parts to about 1100℃ for hot forging. Heating enhances the ductility of the material, making it more malleable for the forging process. And it is often done in a controlled atmosphere to prevent oxidation and contamination.
Advantages of Powder Metallurgy Forging
High Part Precision
The precision of sintered parts is very high, and the error can even be less than 0.05mm. Therefore, powder metallurgy forging does not require more secondary processing like forging.
High Production Efficiency
Powder forging has high production efficiency. One is because powder metallurgy process and forging process mostly use fully automated and semi-automated processes. Another is that powders can be quickly pressed into shape.
Good Material Utilization
The material utilization rate of powder forging is generally greater than 80%. For ordinary forging due to the existence of flash and burr, the material utilization rate is about 50%.
Low Cost
The common die forging process basically includes forging the heated blank with multiple rollers, and then forging it on a press. Then, multiple processes such as trimming, punching, and correction are performed.
However, powder forging uses one-time forging to form the blank, eliminating multiple processes and greatly improving production efficiency, which can reach 12~15 pieces/min. This reduces a lot of equipment and labor investment.
In addition, due to the presence of pores, the deformation resistance of sintered parts during forging process is relatively small, so the required forging heating temperature is lower than that of ordinary forging.
Good Mechanical Properties
After forging process, the density of sintered parts can be increased to more than 98%. This can effectively reduce the porosity and improve the strength and toughness of the parts. In addition, the internal structure of powder forged parts is uniform and isotropic.
Long Mold Lifespan
Powder forging has low temperature, no burrs, less die surface wear, and the forging unit pressure is much lower than ordinary die forging. Therefore, compared with ordinary die forging, its die lifespan can be increased by more than 10 times.
Factors Affecting Powder Forging
Forging temperature
In the powder forging process, the forging temperature can improve the density of the parts within a certain range.
During the powder forging process, the forging temperature can improve the density of parts within a certain range. Studies have shown that when the forging pressure of iron-based parts is 510MPa, the forging temperature increases from 900℃ to 1000℃, and the density of parts increases from 99.0% to 99.3%.
However, when it increases to 1100℃, the density of parts increases little.
Alloying elements
Carbon is an important alloying element. It has a significant impact on the hardness, tensile strength, wear resistance, etc. of the material.
Application of Powder Forging
By minimizing material waste and enhancing grain structure, powder forging creates lightweight yet durable parts. It is particularly advantageous in automotive applications.
Powder Forged Connecting Rod
Powder forged connecting rods are widely used in automotive engines, with about 60% of them produced using this technology. These rods offer numerous benefits, including high strength, precision, excellent performance, and reduced weight.
BLUE is a professional powder metallurgy manufacturer, offering a full range of powder forged connecting rod solutions for gasoline engines and diesel engines. Our forged powder metal connecting rods feature tight tolerances, high dimensional consistency, and a density close to that of forged steel (>7.80 g/cm³), resulting in excellent fatigue strength and load-bearing performance.
Powder Forged Cam
Powder forged cams excel in meeting the performance demands of automobile engine cams while offering significant material savings and reduced production costs.
Synchronizer Gear Rings
Iron-based powder forged synchronizer gear rings have a 40% lower cost than traditional copper-based gear rings.
Powder forging effectively achieves the densification of parts, for example, steel can reach 7.85g/cm³. It has the advantages of high efficiency, low cost and large-scale production of high-performance products.
Compared with traditional forging process, powder forging can produce parts with higher precision and lower roughness. The following table is their comparison.
Parameter | Forged parts | Powder Forged [arts |
---|---|---|
Dimension fluctuation / 100mm (mm) | ±1.5 | ±0.2 |
Dimensional accuracy (mm) | IT13 to IT15 | IT6 to IT9 |
Surface roughness (μm) | ≥12.5 | 0.8 to 3.2 |
Oxide scale / Burr | Have | Don’t have |
Mold lifespan /10,000 pieces | 0.4 | 4 to 10 |